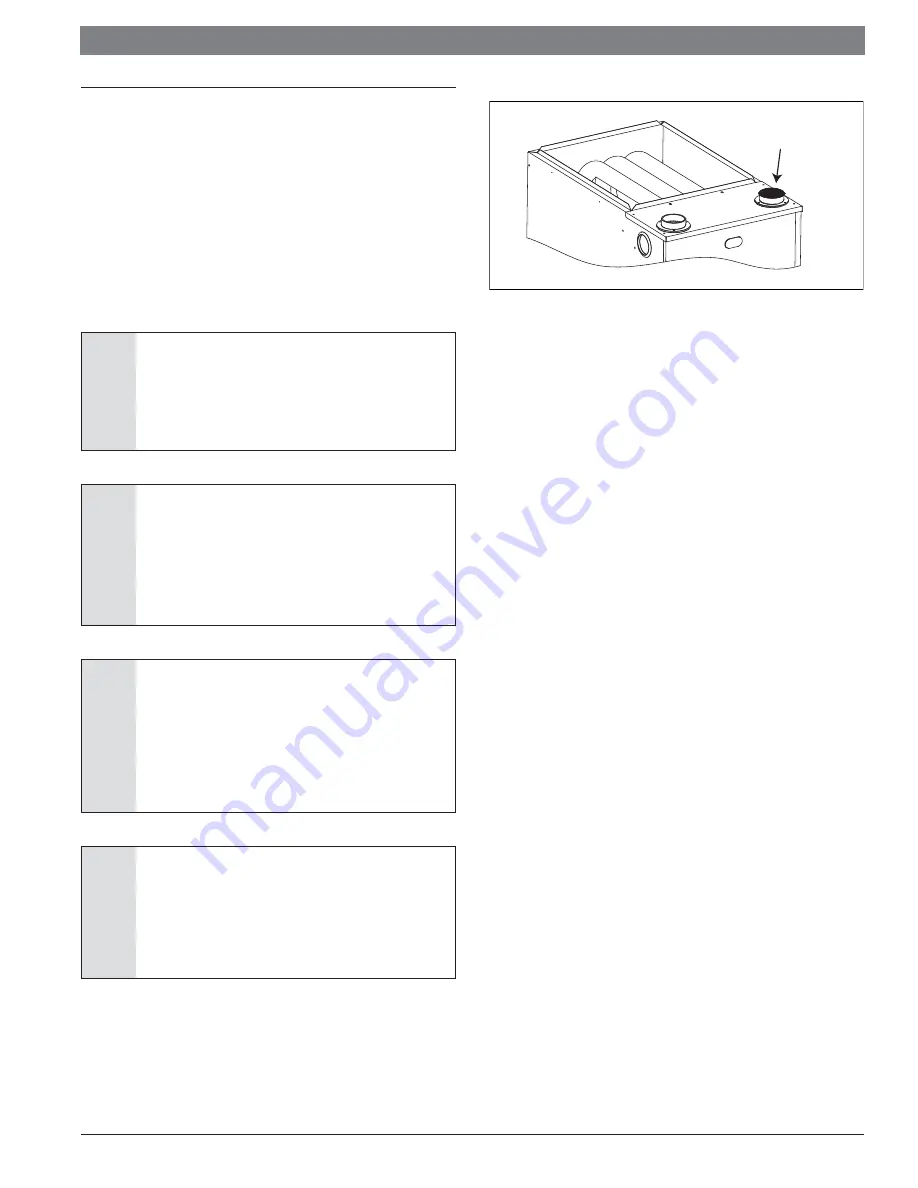
2 6 |
E
coer
96%
A
F
UE
Gas Furnace
Installation, Operation & Maintenance
07-2021
|
E
coer
I
nc
.
Data subject to change
8 Combustion Air and Vent System
8.1 Combustion Air and Vent Safety
This Category IV, dual certi
fi
ed (AHRI and ETL) direct vent furnace is designed for
residential applications. It may be installed without modi
fi
cation to the condensate
system in a basement, garage, equipment room, alcove, attic or any other indoor
location where all required clearance to combustibles and other restrictions are
met. The combustion air and the venting system must be installed in accordance
with Section 5.3, Air for Combustion and Ventilation, of the National Fuel Gas Code
Z223.1/NFPA 54 (latest edition), or Sections 7.2, 7.3 or 7.4 of CSA B149.1,
National Gas and Propane Codes (latest edition) or applicable provisions of the
local building code and these instructions.
NOTICE:
The “VENT SYSTEM” must be installed as specified in these
instructions for Residential and Non HUD Modular Homes.
The direct vent system is the only con
fi
guration that can be
installed in a Non HUD Modular Home.3.
NOTICE:
Do not discharge exhaust gases directly into any chimney
or vent stack. If vertical discharge through an existing
unused chimney or stack is required, insert piping inside
chimney until the pipe open end is above top of chimney
and terminate properly. In any exterior portion of chimney,
the exhaust vent must be insulated.
NOTICE:
When combustion air pipe is installed above a suspended
ceiling or when it passes through a warm and humid
space, the pipe must be insulated with 1/2” Armaflex or
other heat resistant type insulation if two feet or more of
pipe is exposed. Vent piping must be insulated if it will be
subjected to freezing temperatures such as routing through
unheated areas or through an unused chimney.
NOTICE:
Prior to installing the exhaust vent pipe, ensure that the
black plastic cap is removed from the coupler on furnace
cabinet. The cap is only used to prevent debris from
falling into the vent opening and into the inducer during
installation. Refer to Figure 21.
Figure 21
Remove cap
Protective Cap Removal
8.2 Combustion Air/Vent Pipe Sizing
The size of pipe required will be determined by the furnace model, the total length
of pipe required and the number of elbows required. Table 5, "Maximum Equivalent
Pipe Length" lists the maximum equivalent length of pipe allowed for each model of
furnace. The equivalent length of elbows is shown in Table 7, "Equivalent Length of
Fittings".
The equivalent length of the vent system is the total length of straight pipe PLUS the
equivalent length of all of the elbows. The following rules must also be followed:
1.
Long radius (sweep) elbows are recommended. Standard elbows may
be used, but since they have a longer equivalent length, they will reduce
the total length of pipe that will be allowed. Short radius (plumbing vent)
elbows are not allowed. The standard dimensions of the acceptable elbows
are shown below.
2.
The maximum equivalent length listed in Table 5, "Maximum Equivalent
Pipe Length" is for the vent piping and the air intake piping separately. For
example, if the table allows 60 equivalent feet for a particular model, then
the vent can have 60 equivalent feet of pipe, AND the combustion air intake
can have another 60 equivalent feet of pipe.
3.
Three vent terminal elbows (two for the vent and one for the combustion air
intake) are already accounted for and need not be included in the equivalent
length calculation.
4.
All combustion air and vent pipes and
fi
ttings must conform to American
National Standards Institute (ANSI) and American Society for Testing and
Materials (ASTM) standards, D1785 (Schedule 40 PVC), F441 (Schedule
40 CPVC), D2665 (PVC-DWV), F891 (PVC-DWV Cellular Core), D2661
(ABS-DWV) or D1527 (Schedule 40 ABS). Pipe cement and primer must
conform to ASTM Standard D2564 (PVC), F493 (CPVC) or D2235 (ABS). If
ABS pipe is to be used, any joint where ABS pipe is joined to PVC pipe must
be glued with cement that is approved for use with BOTH materials. As an
alternate, use all purpose cement, to bond ABS, PVC, or CPVC pipe when
using
fi
ttings and pipe made of the same materials. Metallic materials must
not be used for venting or air intake.
5.
If
a
fl
exible connector is used in the vent system, it must be made of
a material that is resistant to acidic exposure and to at least 225° F
temperature. Flexible connectors are also allowed in the combustion air
pipe.
6.
All models are supplied with 2" vent connections. When the pipe must be
increased to 3" diameter, the transition from 2" to 3" must be done as close
to the furnace as possible. For up
fl
ow models, the transition from 2" to 3"
should be done immediately above the furnace. For down
fl
ow or horizontal
models, the transition from 2" to 3" pipe should be done immediately after
exiting the furnace.