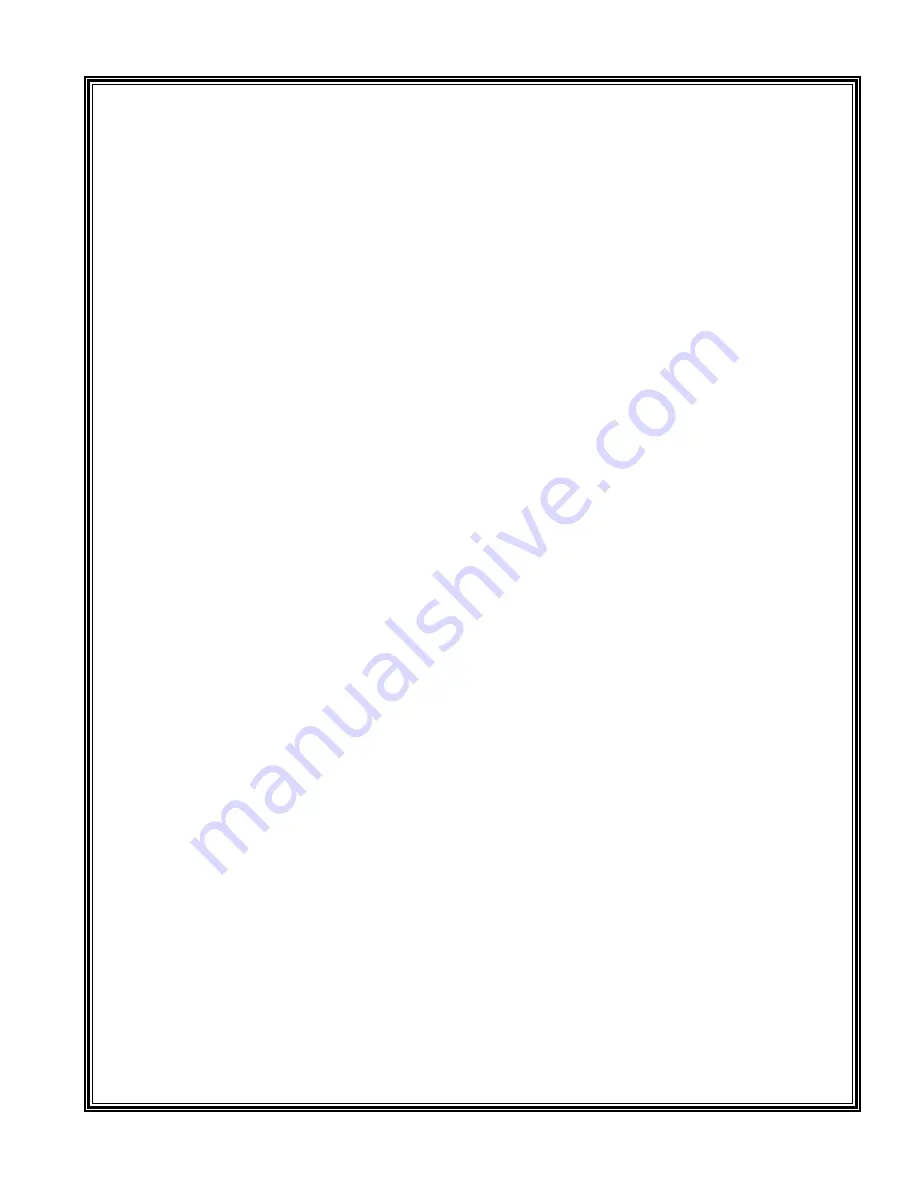
LIMITED WARRANTY
This warranty applies to all ECHO Bear Cat
®
Outdoor Power Equipment manufactured by Crary
®
Industries, Inc. and does not
include gas engine or electric powered pressure washers under the ECHO Bear Cat brand. See ECHO Bear Cat Pressure
Washer Limited Warranty for complete warranty details on those products.
Crary Industries, Inc. warrants to the original owner each new ECHO Bear Cat product to be free from defects in material and
workmanship, under normal use and service. The warranty shall extend, from date of purchase, 3 years (U.S. and Canada
only (2 years outside U.S. and Canada)) for Consumer use of the product, 1 year for Commercial applications and 6 months
for Rental applications. Replacement parts and accessories are warranted for (90) days from date of installation. Batteries for
Inverters and Generators are warranted for ninety (90) days from the date of purchase.
“Consumer” defined as: complete unit for personal, residential or non-income producing use.
“Commercial” defined as: complete unit for commercial, institutional, property management, agricultural, horticultural or income
producing use.
“Rental” defined as: complete unit for rental purposes to produce income.
*Models SC2163, SC2170, SC3206 & SC3208 are classified as Consumer grade products and will not qualify for warranty
coverage if used for Commercial or Rental purposes.
The product is warranted to the original owner by either a completed warranty registration on file at Crary Industries, Inc. and/or
proof of sale. Warranty coverage begins on the date of purchase. The warranty registration can be registered on-line by visiting
bearcatproducts.com/Product-Support/Product-Registration or the paper card completed and returned to Crary Industries, Inc.
In the event of a failure, return the product, at your cost, along with proof of purchase to the selling ECHO Bear Cat dealer. Crary
Industries, Inc. will, at its option, repair or replace any parts found to be defective in material or workmanship. Warranty on any
repairs will not extend beyond the product warranty. Repair or attempted repair by anyone other than an authorized ECHO Bear
Cat dealer as well as subsequent failure or damage that may occur as a result of that work will not be paid under this warranty.
Crary Industries, Inc. does not warrant replacement components not manufactured or sold by Crary Industries, Inc.
1. This warranty applies only to parts or components that are defective in material or workmanship.
2.
This warranty does not cover normal wear items including, but not limited to: batteries, bearings, belts, pulleys, filters,
chipper blades, shredder flails or knives.
3. This warranty does not cover normal maintenance, service or adjustments.
4. This warranty does not cover depreciation or damage due to misuse, negligence, accident or improper maintenance.
5. This warranty does not cover damage due to improper setup, installation or adjustment.
6.
This warranty does not cover damage due to unauthorized modifications of the product.
7. Engines are warranted by the respective engine manufacturer and are not covered by this warranty.
ECHO Bear Cat’s Demo Fleet Warranty Program includes the following distributor guidelines. On the first day the machine is
used for demonstration, all demo units must be registered to the distributor. A demo unit is under warranty to the distributor as
long as it is in the demo fleet, a term which cannot exceed two years. If delivery date to the distributor is more than one year prior
to the date unit enters the demo fleet, the warranty is expired. All units sold to customers within the demo period will be granted
a six month commercial warranty or one year consumer warranty. In order for these warranties to be effective, all registrations
must be changed to new owner once units are sold. Should unit be sold to customer outside of the demo period, no warranty
is offered by the manufacturer.
Crary Industries, Inc. is not liable for any property damage, personal injury or death resulting from the unauthorized modification
or alteration of an ECHO Bear Cat product or from the owner’s failure to assemble, install, maintain or operate the product in
accordance with the provisions of the Owner’s manual.
Crary Industries, Inc. is not liable for indirect, incidental or consequential damages or injuries including but not limited to loss of
crops, loss of profits, rental of substitute equipment or other commercial loss.
This warranty gives you specific legal rights. You may have other rights that may vary from area to area.
Crary Industries, Inc. makes no warranties, representations or promises, expressed or implied as to the performance of its
products other than those set forth in this warranty. Neither the dealer nor any other person has any authority to make any
representations, warranties or promises on behalf of Crary Industries, Inc. or to modify the terms or limitations of this warranty
in any way. Crary Industries, Inc., at its discretion, may periodically offer limited, written enhancements to this warranty.
CRARY INDUSTRIES, INC. RESERVES THE RIGHT TO CHANGE THE DESIGN AND/OR SPECIFICATIONS OF ITS
PRODUCTS AT ANY TIME WITHOUT OBLIGATION TO PREVIOUS PURCHASERS OF ITS PRODUCTS.
ENGLISH