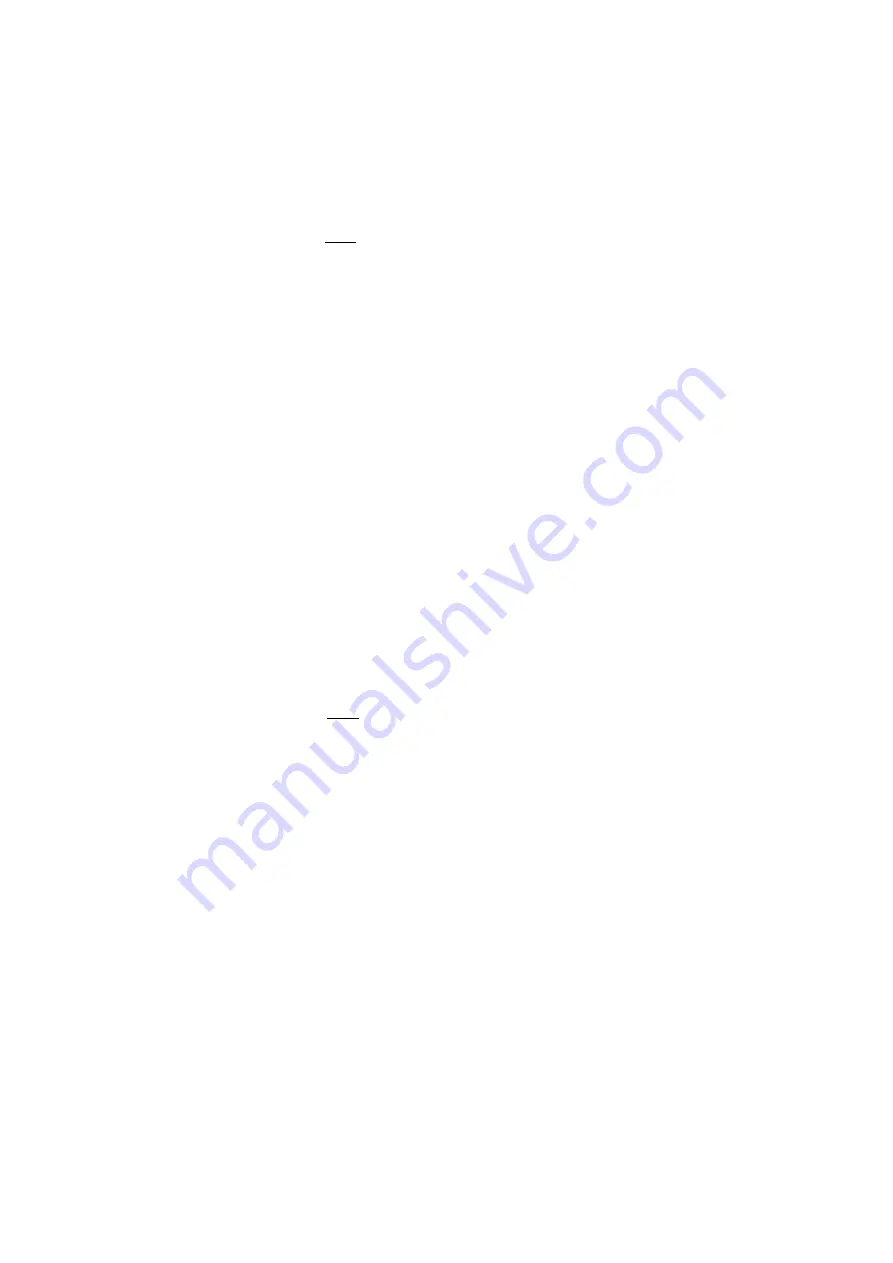
7
3.
Apply a suitable sealant (e.g. Loctite) to the Inner
Rotor Pin bore in the cover.
Ensure sealant does
not enter the Inner Rotor.
Press Inner Rotor Pin
into Cover ensuring lubrication groove points
centrally towards crescent and adequate support is
given around the Inner Rotor Pin bore boss when
pressure is applied.
4.
Place Inner Rotor Pin Spacer (if fitted) and Inner
Rotor Pin Washer over Inner Rotor Pin and lock
Inner Rotor Pin Nut securely whilst maintaining
lubrication groove location. Note: Use of a split
clamp will aid this operation.
5.
Fit Body to Bracket with Gasket between faces.
Maintain correct inlet and discharge port
orientation, securely tighten in a uniform manner.
6.
Insert Rotor/Shaft assembly ensuring Rotor Bearing
is lubricated.
7. Fit Inner Rotor over Inner Rotor Pin in Cover
assembly with flush side towards Cover, ensure
Inner Rotor Pin Bearing is lubricated.
8.
Fit Cover assembly to Body with Gasket between
faces, make sure the seal land of the Cover
matches with the seal land in the pump Body. (This
seal land is diametrally opposite the centre of the
Cover crescent). Lubricate pump elements through
pump port and check that Rotor/Shaft assembly
turns freely.
......For pumps fitted with EBSRAY mechanical seals:
9.
Slide Circlip along Shaft ensuring gap in Circlip
lines up with access hole. Take care to avoid
scratching Shaft.
10. Slide Circlip Retainer along Shaft until located
against Circlip (a suitable tube may help, keep drive
screw inline with access hole), tighten Drivescrew.
11. Insert Spring, Drivewasher, Rotating 'O'ring,
Rotating Face, Stationary Face, Stationary 'O' ring
and Mechanical Seal Plate. Note: Particular care
must be taken to avoid contamination of lapped
seal surfaces by any foreign matter. All parts should
be lubricated before assembly and Drivepins must
be located during assembly. Mechanical Seal Plate
must be fastened evenly.
......For pumps fitted with packed glands:
9.
Place Packing rings in position in accordance with
normal packing procedures. For standard square
Packing with one Lantern Ring, use eight (8) rings
of 12.7mm square Packing. For other types of
packing refer to suppliers instructions.
10. Position Gland Plate and tighten by hand only.
11. Final adjustment is carried out during operation of
pump. Packed glands, when adjusted correctly are
designed to have a very small amount of seepage.
If packing is too tight it will generate excessive heat,
if too loose it will leak excessively.
12. Lubricate Lipseal on Inner Lockring and slide
Lockring along Shaft, screw Lockring in until it
protrudes approximately 4mm from thread on pump
side.
13. Lubricate Bracket Ball Bearing. Fit Bearing to Shaft
and drive Bearing into position against Shaft
shoulder using a suitable drift. Bearing should only
be tapped on by using a drift on its inner ring.
Tapping on the outer ring could damage the
bearing.
14. Lubricate outer lockring Lipseal and screw Outer
Llockring into Bracket.
15. Slide Ball Bearing locknut along Shaft through
Lipseal and tighten firmly using a suitable tool.
Tighten Locknut Locking Screws.
16. Replace lubrication/cooling circulation harness
assemblies if fitted.
17. If fitted, reinstall Bypass Valve – Refer Section 5.
4.7
ROTOR AXIAL CLEARANCE ADJUSTMENT
The Inner and Outer Lockrings when finally positioned
determine the Bracket Ball Bearing location within the
Bracket. As the Ball Bearing is positively locked to the
Shaft shoulder by the Bearing Locknut, the positioning of
the Ball Bearing will control the Rotor axial clearance.
To adjust axial clearance:
a) A crank handle or other suitable arrangement
should be affixed on the coupling end of the
Rotor/Shaft assembly to facilitate rotating of the
assembly by hand.
b) Screw Outer Lockring in a clockwise direction
whilst simultaneously rotating assembly. This
enables sensing the rotor-cover point of contact
ie. a slight drag is felt by hand.
c) Mark Outer Lockring position relative to Bracket
i.e. establish a datum point for setting axial
clearance.
d) Back off Outer Lockring 180 degrees to
eliminate any backlash.
e) Reposition Outer Lockring to a point measured
radially from the previously marked datum equal
to the amount of desired axial clearance.
Note:
For model HD600 5.14 mm radial movement on
the O.D. of the Outer Lockring equals 0.025 mm axial
movement of the Rotor/Shaft assembly. Refer Table of
Clearances for actual clearances.
Example: Standard 'A' clearance 0.13 - 0.18 mm
(0.13
÷
0.025) x 5.14 = 26.7
(0.18
÷
0.025) x 5.14 = 37.0
is equivalent to 26.7 - 37.2 mm radial movement on the
outside diameter of the Outer Lockring.
f) Screw in Inner Lockring to lock hard against ball
bearing. At this point, check for freedom of
rotation of assembly. Axial clearance should
now be established.
g) Tighten Inner and Outer Lockring Lockscrews.
Содержание HD600
Страница 11: ...11 11 ...