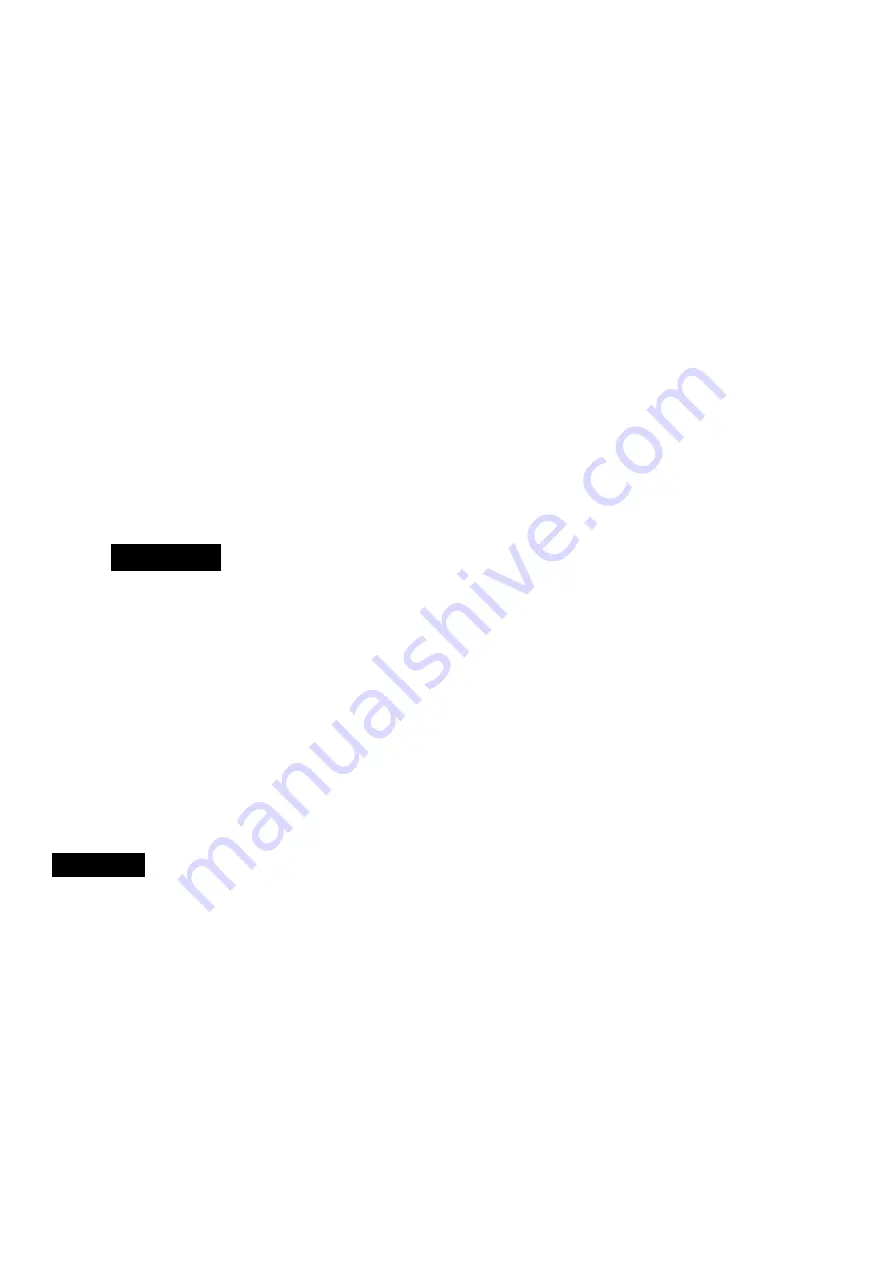
SECTION 1 - GENERAL
INTRODUCTION
This leaflet is intended to assist those involved with the
installation, operation and maintenance of EBSRAY
Model HD600 Internal Gear Positive Displacement
Pump. The design, materials and workmanship
incorporated in the manufacture of EBSRAY pumps
make them capable of reliable operation over a long
working life. Correct installation is essential. Service life is
enhanced by periodic inspection and careful
maintenance.
1.1
CAUTION
INSTALLATION AND SERVICING OF THIS
EQUIPMENT SHOULD BE PERFORMED BY
QUALIFIED COMPETENT PERSONNEL IN
ACCORDANCE WITH RELEVANT STATUTORY
REGULATIONS OR CODES, IN CONJUNCTION WITH
THESE INSTRUCTIONS.
When the equipment supplied utilises components other
than those manufactured by EBSRAY e.g. couplings,
speed reducers, electric motors etc, reference should be
made to the original manufacturer's data before
installation or servicing is commenced. Failure to observe
these details may void the warranty.
1.2
The pump must be operated within the original
selected design parameters of speed, temperature,
pressure and viscosity. Should any change be
contemplated, please confer with EBSRAY in order
to verify the suitability of such a change.
1.3
TRANSPORTATION AND PACKING
Standard domestic packing is suitable for shipment in
covered transports. Ports must be sealed to exclude
ingress of solids. When received on site the pump should
be stored in a dry covered area.
If storage is required for other than a short period prior to
installation, special preservatives and protective
wrappings will be required. Refer to EBSRAY for details.
1.4
INSPECTION ON RECEIPT - SHORTAGES
On receipt of equipment, check all items against the
dispatch documents and inspect for damage. Any
damage or shortage incurred during transit should be
noted on the packing note and on both your own and the
carrier's copy of the consignment note and a claim
should be made immediately on the transport company.
Should a shortage be evident on receipt, notify EBSRAY
immediately giving full details and packing note number.
1.5
HANDLING
Do not drop pump/pumpset
Care should be taken in
moving/handling pumps/pumpsets. A sling should be
placed under or around a pump/pumpset in order to
minimise stress on the internal components.
The pump/pumpset should be lifted in such a manner as
to ensure compliance with the relevant lifting codes.
Severe internal damage may result if correct
handling and due care is not taken.
SECTION 2 - INSTALLATION
CAUTION
INSTALLATION AND REMOVAL OF THIS EQUIPMENT
SHOULD BE PERFORMED BY QUALIFIED COMPETENT
PERSONNEL IN ACCORDANCE WITH RELEVANT
STANDARDS, CODES, REGULATIONS AND SITE
RESTRICTIONS - IN CONJUNCTION WITH THESE
INSTRUCTIONS.
NEVER LOOSEN OR REMOVE FITTINGS, FLANGES, ETC.
WHILE UNDER PRESSURE, ALWAYS ISOLATE
COMPONENTS OR PIPEWORK AND DEPRESSURISE
PRIOR TO WORK.
2.1
LOCATION
The pumpset should be placed as close as practicable to
the source of supply, keep within the NPSH requirement
of the pump. Ensure floor area and headroom allotted is
sufficient for inspection and maintenance. Allow sufficient
space and ventilation for motor cooling requirements.
Allow for crane or hoist access if required.
2.2
FOUNDATIONS
Baseplate mounted Pumpsets should be accurately
installed. When on a concrete foundation ensure that it
has been poured on a solid footing. NOTE: Position
foundation bolts to match baseplate foundation plan.
Pumpsets must be securely bolted down.
2.3
PUMP PIPING CONNECTIONS
All piping should be supported independently of and line
up accurately with the pump ports.
SEVERE DAMAGE COULD RESULT IF PIPING IS
DRAWN INTO PLACE BY USE OF FORCE AT THE
PORT CONNECTIONS OF THE PUMP.
2.4
STRAINER PROTECTION
The pump inlet should always be protected by an
efficient strainer of adequate size to accommodate the
liquid viscosity conditions and within NPSH
R
by the pump
DANGER
WARNING
2
Содержание HD600
Страница 11: ...11 11 ...