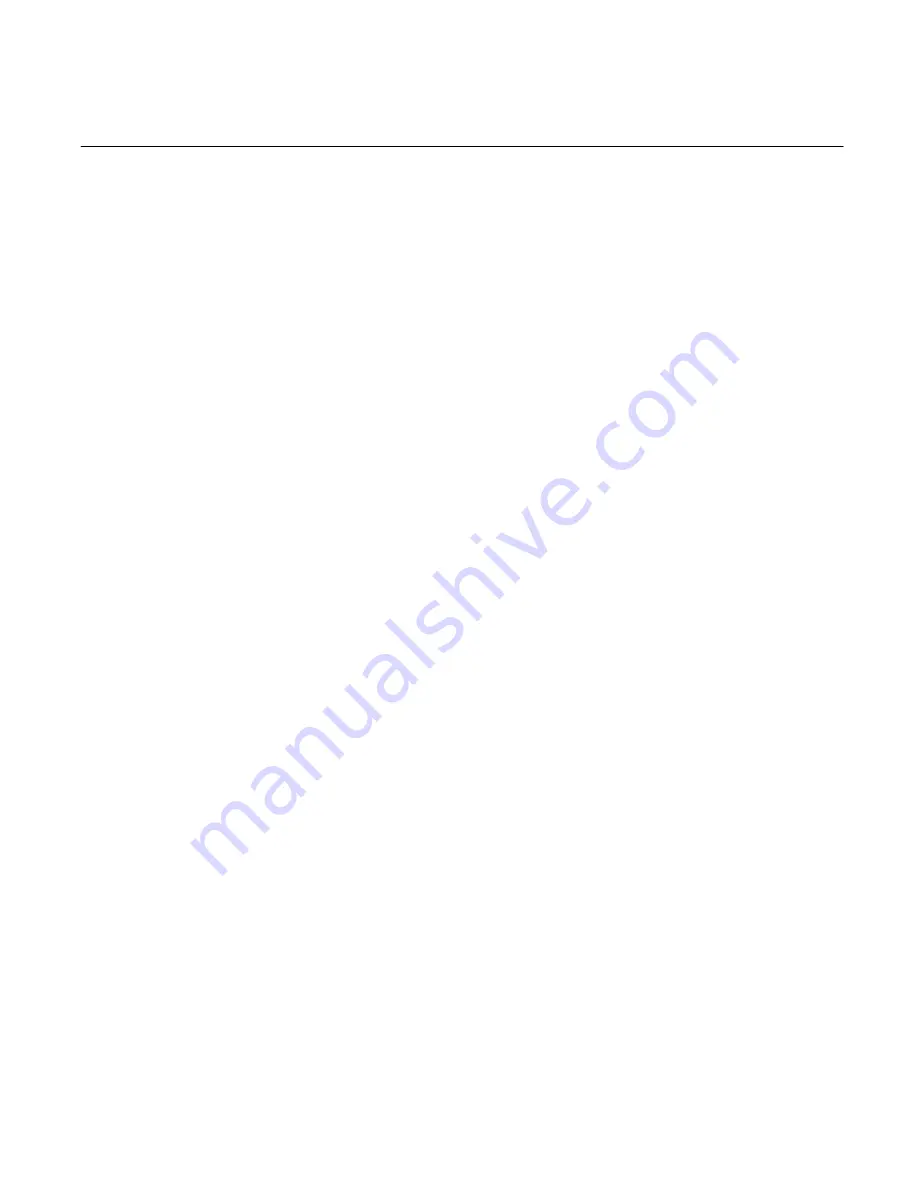
23
6. Lubricate spool lands with clean system fluid and then
carefully install spool (15) into main body bore. Make
sure the spool moves freely inside the body bore and is
oriented properly. (See parts drawing).
Note
Spring and washer do not exist on floating type models
or on opposite side of spring offset ‘‘A’’ models.
7. Install washer (14) and spring (13) on end of spool.
8. Install ‘‘O’’ ring (12) into cover (11).
9. Install cover on body with four screws (10). Torque the
screws to value noted in parts drawing. Refer to Table 1.
Make sure cover is oriented properly (in line with body
contours).
Note
Repeat steps 7 through 9 for opposite side cover
assembly.
L. Pilot Valve and Module Assembly
(Refer to Figure 15)
1. Install plug (9) into adapter plate (8).
2. Install adapter plate on body (5) with four screws (7).
Torque the screws to the value noted in parts drawing.
Refer to Table 1.
3. Install ‘‘O’’ rings (6) in pilot choke (3) and pilot valve (2).
4. Install pilot choke and pilot valve on body with four
screws (1).Torque the screws to the value noted in parts
drawing. Refer to Table 1.
M. Pressure Centered Main Stage Assembly
(Refer to Figure 17)
1. Install ‘‘O’’ rings (24) on plugs (25). Lubricate plug
threads and install plugs and set screws into body (6).
Torque plugs to value noted in parts drawing. Refer to
Table 1.
2. Tap new rest pin(s) (27) into place if removed during
disassembly.
3. Install ‘‘O’’ rings (21) into ‘X’ and ‘Y’ port mounting grooves.
4. Install ‘‘O’’ rings (22) into port mounting grooves ‘A’, ‘B’
and ‘T’.
5. Install ‘‘O’’ rings (23) in body.
6. Lubricate spool lands with clean system fluid and then
carefully install spool (13) into main body bore. Make
sure the spool moves freely inside the body bore and is
oriented properly. (See parts drawing).
7. Install piston (12), sleeve (11) and spring (10) into cover (8).
8. Install ‘‘O’’ ring (9) in cover and install cover on body with
four screws (7). Torque the screws to the value noted in
parts drawing. Refer to Table 1.
9. Install centering washer (20) and spring (19) in body.
10. Install ‘‘O’’ ring (18) in cover (17) and install cover on
body with four screws (16). Torque the screws to the
value noted in parts drawing. Refer to Table 1.
11. Install ‘‘O’’ ring (15) and plugs (14) into cover (7).
12. Install crossover plate (4) on body with four screws (3).
Torque screws to value noted in parts drawing. Refer to
Table 1.
13. Install name plate (2) on crossover plate with four screws
(1).Torque screws to value noted in parts drawing. Refer
to Table 1.
M. High/Standard Performance Pilot Valve
Assembly
(Refer to Figure 18)
1.. Install ‘‘O’’ rings (25) on plugs (24). Lubricate plug
threads and install into body (10). Install remaining ‘‘O’’
rings (25) into body (10). Torque plugs to the value
shown in parts drawing. Refer to Table 1.
2. Lubricate pilot spool (22), then carefully install spool into
the body (10).
Note
If pilot valve is equipped with two solenoids, repeat steps
3 through 7.
3. Assemble washer (19) or (20) on end of spool (22) with
sharp break edge toward outside of body.
4. Install spring (18), push pin (17) and ‘‘O’’ ring (15) into
body (10).
5. Install ‘‘O’’ ring (16) on core tube S/A (21) and install core
tube S/A into body (10).
6. Install ‘‘O’’ ring (13) on core tube S/A (20).
7. Install coil (14) on body (10) and secure to core tube S/A
(20) with knob (12).
8. Install gasket (6) and terminal box (5) on body (10) and
secure with ground screw (11) and two screws (9).
9. Install strap (8) on terminal box (5) with two screws (7).
10.Install gasket (4), cover (3) and nameplate (2) on terminal
box (5) with four screws (1).