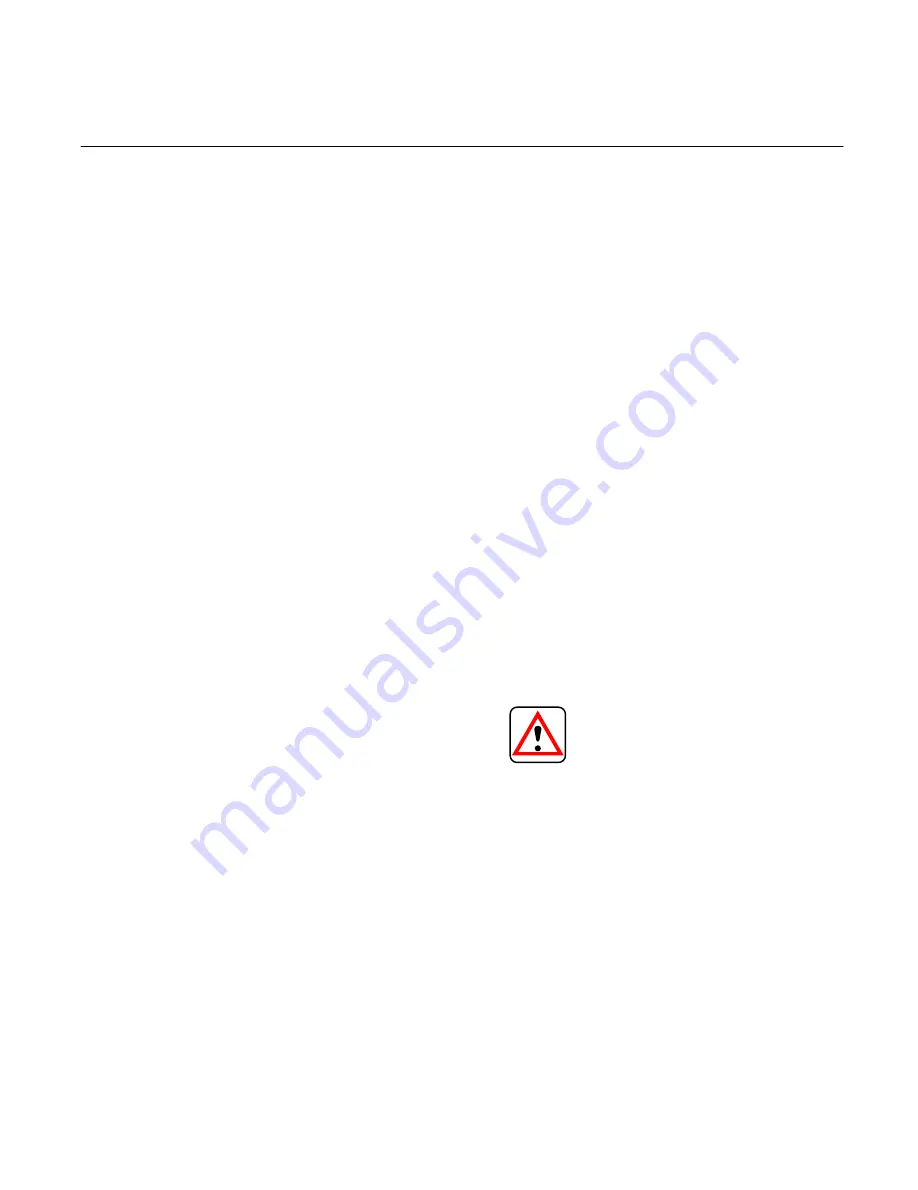
21
F. High/Standard Performance Pilot Valve
Disassembly
(Refer to Figure 18)
Note
The following steps describe the disassembly sequence
of a DG4V-3(S)-*A(L)/B(L)-FJ/FW-60 pilot valve.
1. Remove the four screws (1) from name plate (2) and
remove the nameplate, cover (3) and gasket (4) from the
terminal box (5). Discard gasket (4).
2. Remove two screws (7) and strap (8) from the terminal
box (5).
3
Remove two screws (9), ground screw (11), terminal box
(5) and gasket (6) from body (10). Discard gasket (6).
Note
If the pilot valve is equipped with two solenoids, perform
steps 4 through 6 for opposite end of body (10).
4. Remove knob (12) ) from core tube S/A (21). Remove
coil (14) from body (10) and discard ‘‘O’’ Rings (13) and
(15).
5. Remove push pin (18), spring 917), washer (19) or (20)
and ‘‘O’’ Ring (15) from body (10). Remove ‘‘O’’ Ring (16)
from core tube S/A (21).
6. Remove pilot spool (22) from body (10).
7. Secure the body and remove plug (24) and ‘‘O’’ Ring (25)
from body (10). Discard ‘‘O’’ Ring (25).
8
If necessary, remove rest pins (26) with vise grip pliers.
G. Wet Armature Pilot Valve Disassembly
(Refer to Figure 19)
Note
The following steps describe the disassembly sequence
of a DG4S4-01*B/C-(U)-*-60 pilot valve.
1. Remove the four screws (1) from name plate (2) and
remove the nameplate from the body (5). Remove screw
(4) and gasket & wire S/A (3) from body (5).
Note
If the pilot valve is equipped with two solenoids, perform
steps 3 through 6 for opposite end of body (5).
2. Remove knob (8) and ‘‘O’’ Ring (9) from core tube S/A
(20). Remove coil (10) from body (5) and discard gasket
(14) and ‘‘O’’ Ring (9).
Note
Perform step 4 for models equipped with DIN coils.
3. Remove DIN connector (13) and plug (12) from coil (11).
4. Remove knob (8) and ‘‘O’’ Ring (9) from core tube S/A
(20). Remove coil (11) from body (5) and discard gasket
(14) and ‘‘O’’ Ring (9). Remove plug (12) from coil.
5. Remove washer (15), stop (16), spring (17), push pin
(18) and ‘‘O’’ ring (19) from core tube S/A (20). Discard
‘‘O’’ Ring (19).
6. Remove pilot spool (21) from body (5).
7. Remove plugs (24) and (22) and ‘‘O’’ Ring (23) from
body (5). Discard ‘‘O’’ Ring (23).
8. Secure the body and remove plugs (25 and 27) from body
(5). Remove ‘‘O’’ Rings (26 and 28) from plugs and discard.
Remove and discard ‘‘O’’ Ring (29).
H. Cleaning
All parts must be thoroughly cleaned and kept clean during
inspection and assembly. Close tolerance of valve bodies
and spools make this requirement critical. Clean all parts
with a commercial solvent that is compatible with system
fluid. Compressed air may be used to clean valve, but it
must be filtered to remove water and contamination. Clean
compressed air is particularly useful for cleaning spool
orifices, body passages and drying parts.
I. Inspection, Repair and Replacement
1. Check that all internal passages are clean and free from
obstruction. Examine all mating surfaces for nicks and
burrs. Minor nicks and burrs can be removed with crocus
cloth or an India stone.
CAUTION
DO NOT stone the edges of spool sealing
lands. Remove minor burrs with #500 grit
paper. Use the paper very lightly on the
outer diameter of each spool.
2. Inspect all screws for evidence of damaged threads. If
threads are damaged, replace the screws.
3. Inspect all springs for distortion or wear. The ends of the
springs shall be square and parallel to each other.
Replace springs that are damaged or distorted.
4. Check push pins, pole faces, washers, and manual
plungers for burrs, cracks or mushrooming. Replace all
parts that show evidence of wear.
5. Visually inspect the internal coring (bore) of each body for
large scratches or erosion across the spool land sealing
areas. If such evidence is found, replace valve. If the body
bore passes inspection, check bore to spool clearance
as follows:
A. Lubricate spools and body bores with clean system
fluid. make sure the parts are clean.
B. Insert the spool into its body bore. Rotate the spool
360
while moving it back and forth. Observe the following: