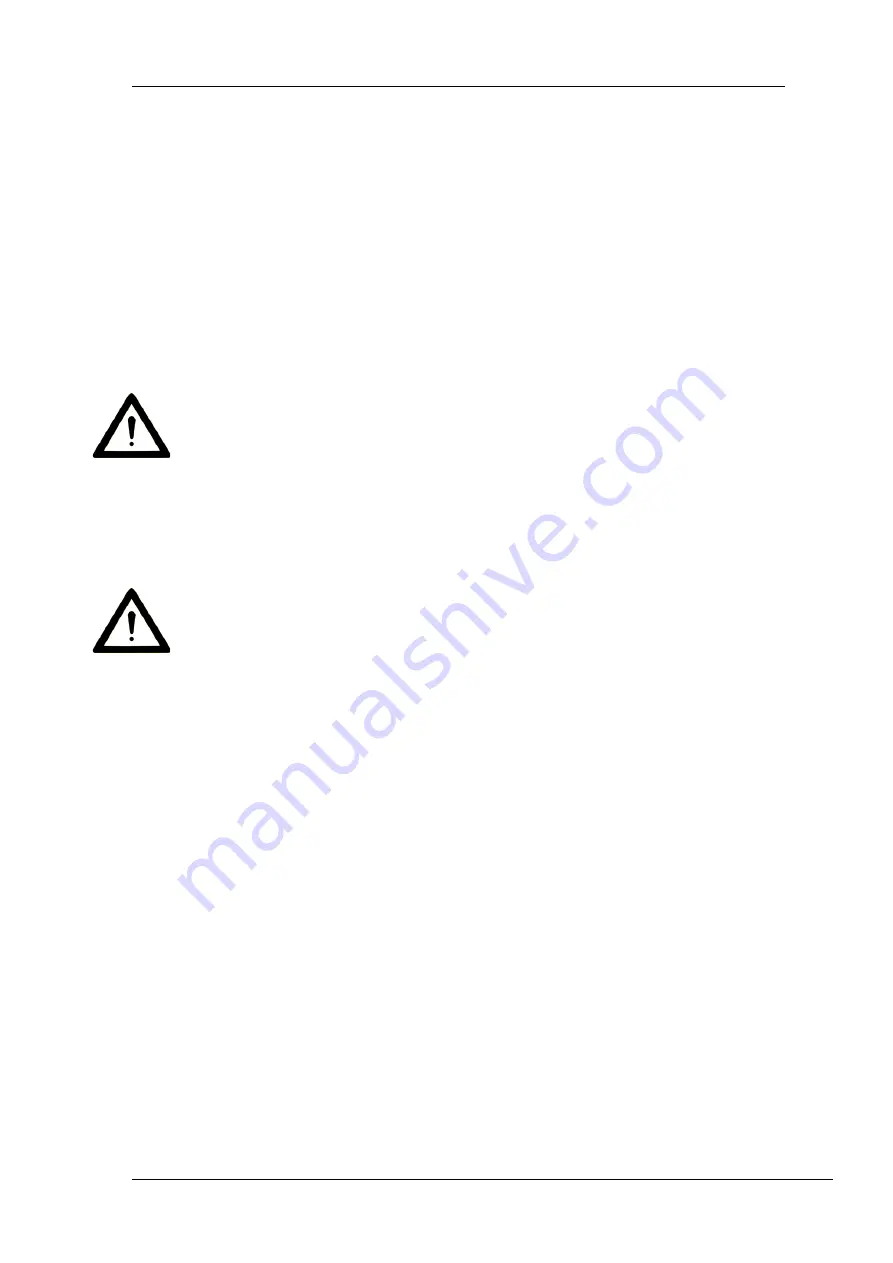
EATON
Installation & Maintenance Instructions
IMI+70-XP-XT Iss_A
© 2020, Eaton
Page 7 of 24
3.0
Installation
In order to ensure proper wiring and system operation of all components, it is recommended
that all units and all associated control equipment be tested at your Factory before field
installation is attempted.
3.1
Unpacking and Handling
3.1.1
Unpacking
On receipt of the units ensure that the cartons are undamaged and that the contents are all
correct and complete. After unpacking it is recommended that the packing materials are
kept safe, should you need to return the unit for repair, or maintenance.
The protective plastic film should be removed from sunshields before they are fitted.
3.1.2
Handling
Due to the reinforced steel construction of the camera units, correct handling is of great importance.
Lifting and positioning XP and XT units should always be completed using suitable lifting
equipment that is capable of supporting loads in excess of 65Kg. XP and XT units should only
be lifted using the L-body/ T-Body, with equal support on both sides. The camera housings
must not be used for lifting. To avoid damage to the unit DO NOT rotate the camera housings
by hand. The units should not be handled using direct contact with ferrous metal equipment.
(see section 4.1 for details)
3.2
Mounting
Ensure the desired mounting surface can support four times the combined weight of the
complete unit.
Do not stand or place objects “directly under” the installed camera system.
Due care and attention must be taken to ensure enough clearance can allow full rotation of
the unit with its associated equipment, and that the moving unit cannot strike, or make
contact with personnel.
It is strongly suggested that the EATON range of mounting brackets are used.
3.2.1
Mounting the XP & XT Series
The XP and XT pan/tilt/housing assembly may be mounted onto various structures such as
bulkheads, walls or towers. it can also be mounted upside down, in the inverted position,
but this must be specified in the customer order.
The complete assembly is mounted to the support structure via its base part, which has
11mm clearance holes for four (4) M10 fixings. (Fig 1)
The type and size of any fixing brackets to be supplied by the user/installer must be
suitable for the installation requirements outlined in this manual.
An alternative is to use the BPW6500 Wall mount bracket (Fig 2)