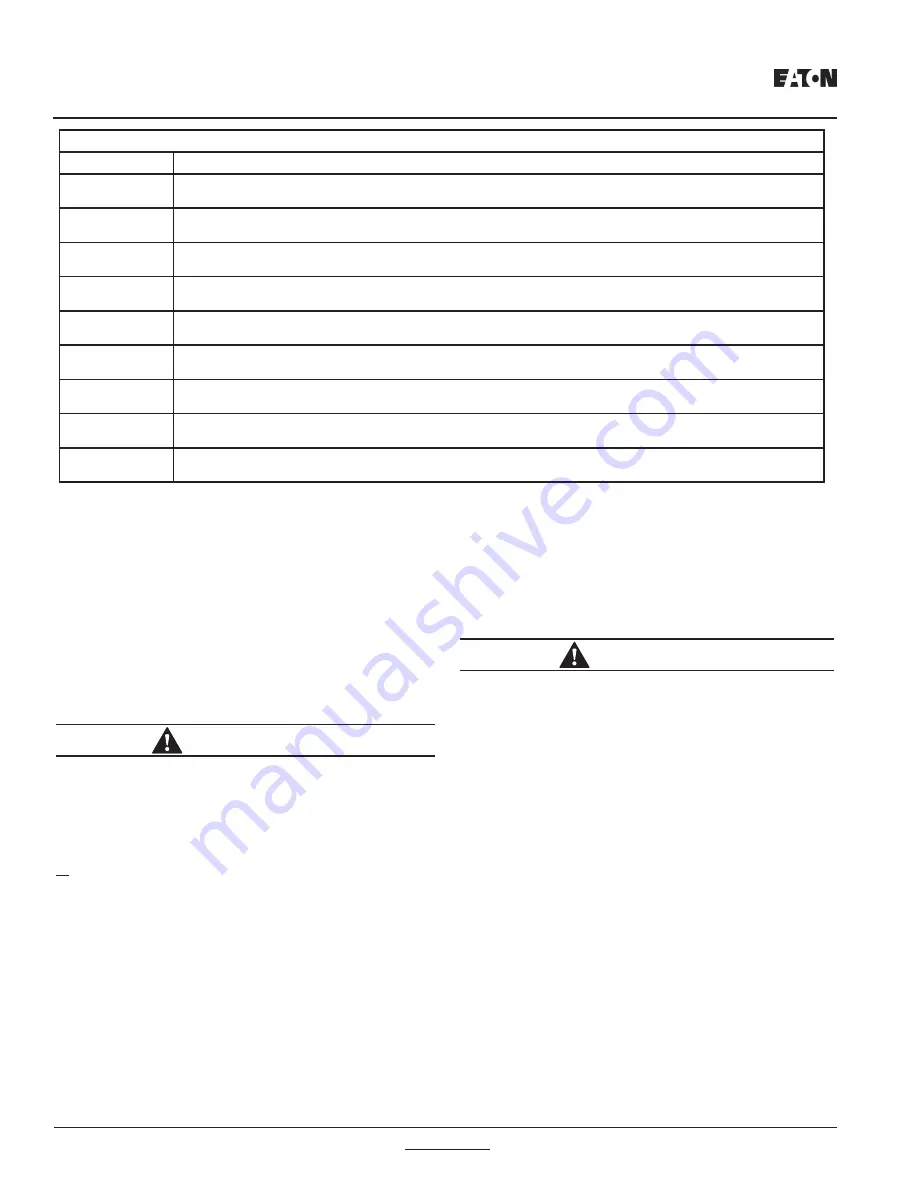
IM02602002E
Page
5-2
www.eaton.com
MP-3000
5.1.2 Setting P1L2, Locked-Rotor Current (LRC)
LRC is set to the locked-rotor current, which is the current the motor
draws when stalled, in percentage of
fLa
(see P1L1). Use the motor
nameplate or manufacturer’s data.
5.1.3 Setting P1L3, Maximum allowable Stall or Locked-Rotor
Time (LRT)
LRT specifies how long a locked-rotor or stall condition can be main
-
tained before the motor is damaged, in seconds, for a cold start. Use
motor nameplate or manufacturer’s data.
LRC
and
LRT
combine to specify a point on the motor damage curve
(Figure 9.4) which, when reached during a start, causes a locked-rotor
trip. Refer to Subsection 9.1.3 for a detailed explanation.
CaUTION
INCORRECT SETTING VaLUES fOR ThESE fUNCTIONS CaN
RESULT IN EXCESSIVE ROTOR TEMPERaTURES aND MOTOR
DaMaGE.
5.1.4 Setting P1L4, Ultimate Trip Current (UTC)
UTC sets the current level above which a trip eventually occurs when
no
RTD stator temperature data is available, in percentage of FLA.
This value represents the limit line on the running (upper) portion of
the non-RTD motor damage curve shown in Figure 9.4.
NOTE:
This UTC setting is where the User considers the service factor
rating of the motor.
Never
adjust the
fLa
setting P1L1 accord-
ing to the service factor (see Subsection 9.1.3.3).
For normal use, set UTC to the
service factor
times 100%. The avail
-
able range is 85% to 150%. The service factor is found on the motor
nameplate or in manufacturer’s data.
Note that the relay does not trip at the moment the current goes above
UTC during motor running. Instead, it models the gradual stator
heating for currents above UTC, and trips only after some time has
passed. The trip time depends on a variety of setting and operating
factors, including motor nameplate data contained in other setting values.
Use a conservative, or lower, value of UTC than that dictated by the
service factor if motor ambient temperatures rise above 40ºC (104ºF)
and the optional URTD Module is not used (see Subsection 9.1.1).
Also, consider lowering the UTC value if the motor is suitably rated,
yet additional safety is critical for the application.
CaUTION
If UTC IS SET aBOVE 100 % TIMES ThE SERVICE faCTOR, MO
-
TOR DaMaGE COULD RESULT.
5.1.5 Setting P1L5, Phase Current Transformer Ratio (PCT)
PCT specifies the numerator of the turns ratio of the main phase current
transformers. Obtain the value from the current transformer (CT) name
-
plate or from the installation drawings
. PCT is not the CT rating, but
the actual turns ratio, which may depend on a CT ratio tap.
Explanation of CT Ratio Presentation
The MP-3000 motor relay is available in multiple styles designed
for use with current transformers (CTs) having a nominal or rated
secondary current of either 5 amperes or 1 ampere. Check the relay
labeling or the catalog number and the CT secondary rating to confirm
a match.
All displayed information is the same for either of the two types of MP-
3000 relays. When CT ratios are to be set, the value entered is the
numerator
of the main CT ratio. The denominator is assumed to be
either 5 or 1 depending on the style of MP-3000 used.
For example, a set of three 400:5 phase CTs might be used with an
MP-3000 specified for 5 A CTs. The phase CT ratio is then set to 400.
Alternatively, a set of three 400:1 CTs could be used with an MP-3000
rated for 1 A CTs. Use a setting of 400 in this case as well.
Table 5.1 Inconsistent Settings Messages.
Display
Complete Help Messages
FLA CT L
THE RATIO OF FLA TO CT RATIO IS BELOW 0.25 - INCREASE FLA OR DECREASE CT RATIO - PRESS PROGRAM
TO CONTINUE
FLA CT H
THE RATIO OF FLA TO CT RATIO IS ABOVE 1.5 - DECREASE FLA OR INCREASE CT RATIO - PRESS PROGRAM
TO CONTINUE
IOC OUT
IOC SETTING IS OUT OF RANGE - DECREASE IOC OR DECREASE FLA OR INCREASE CT RATIO - PRESS PRO-
GRAM TO CONTINUE
JAMT OUT
AM TRIP SETTING IS OUT OF RANGE - DECREASE JAM TRIP OR DECREASE FLA OR INCREASE CT RATIO
- PRESS PROGRAM TO CONTINUE
MA OUT
JAM ALARM SETTING IS OUT OF RANGE - DECREASE JAM ALARM OR DECREASE FLA OR INCREASE CT
RATIO - PRESS PROGRAM TO CONTINUE
ULT LOW
UNDERLOAD TRIP SETTING IS LESS THAN STOP CURRENT LEVEL - DECREASE STOP CURRENT LEVEL OR
INCREASE UNDERLOAD TRIP LEVEL - PRESS PROGRAM TO CONTINUE
ULA LOW
UNDERLOAD ALARM SETTING IS LESS THAN STOP CURRENT LEVEL - DECREASE STOP CURRENT LEVEL OR
INCREASE UNDERLOAD ALARM LEVEL - PRESS PROGRAM TO CONTINUE
STP HIGH
STOP CURRENT LEVEL IS ABOVE THE START LEVEL - DECREASE STOP CURRENT LEVEL - PRESS PROGRAM
TO CONTINUE
TRNS LOW
STOP CURRENT LEVEL IS ABOVE THE TRANSITION LEVEL - DECREASE STOP CURRENT LEVEL OR
INCREASE TRANSITION LEVEL - PRESS PROGRAM TO CONTINUE
Содержание MP-3000
Страница 1: ...IM02602002E www eaton com IM02602002E Rev E MP 3000 Motor Protection Relay ...
Страница 18: ...IM02602002E Page 4 www eaton com MP 3000 This Page Intentionally Left Blank ...
Страница 32: ...IM02602002E Page 4 20 www eaton com MP 3000 This Page Intentionally Left Blank ...
Страница 50: ...IM02602002E Page 6 www eaton com MP 3000 DIMENSIONS IN INCHES CM Figure 6 3 MP 3000 Case Depth Dimensions ...
Страница 53: ...IM02602002E www eaton com Page 6 MP 3000 Figure 6 6 MP 3000 Typical CT Circuit and Motor Control Wiring ...
Страница 54: ...IM02602002E Page 6 10 www eaton com MP 3000 Figure 6 7 Typical AC Supply and URTD Wiring ...
Страница 55: ...IM02602002E www eaton com Page 6 11 MP 3000 Figure 6 8 Alternatives for Discrete Input Wiring ...
Страница 60: ...IM02602002E Page 7 www eaton com MP 3000 This Page Intentionally Left Blank ...
Страница 71: ...IM02602002E www eaton com Page 9 MP 3000 Figure 9 1 Rotor Temperature Tracking ...
Страница 72: ...IM02602002E Page 9 www eaton com MP 3000 Figure 9 2 Motor Protection Curve ...
Страница 73: ...IM02602002E www eaton com Page 9 MP 3000 Figure 9 3 Underload Jam Protection Curve ...
Страница 74: ...IM02602002E Page 9 10 www eaton com MP 3000 Figure 9 4 Motor Protection Curve Example without RTDs ...
Страница 75: ...IM02602002E www eaton com Page 9 11 MP 3000 Figure 9 5 Motor Protection Curve Example with RTDs ...
Страница 76: ...IM02602002E Page 9 12 www eaton com MP 3000 Figure 9 6 Motor Start and Run Cycles ...
Страница 79: ...IM02602002E www eaton com Page 10 MP 3000 Figure 10 1 PONI Communications Module ...
Страница 90: ...IM02602002E Page 12 www eaton com MP 3000 This Page Intentionally Left Blank ...
Страница 99: ...www eaton com MP 3000 IIM02602002E This Page Intentionally Left Blank Page 13 9 ...