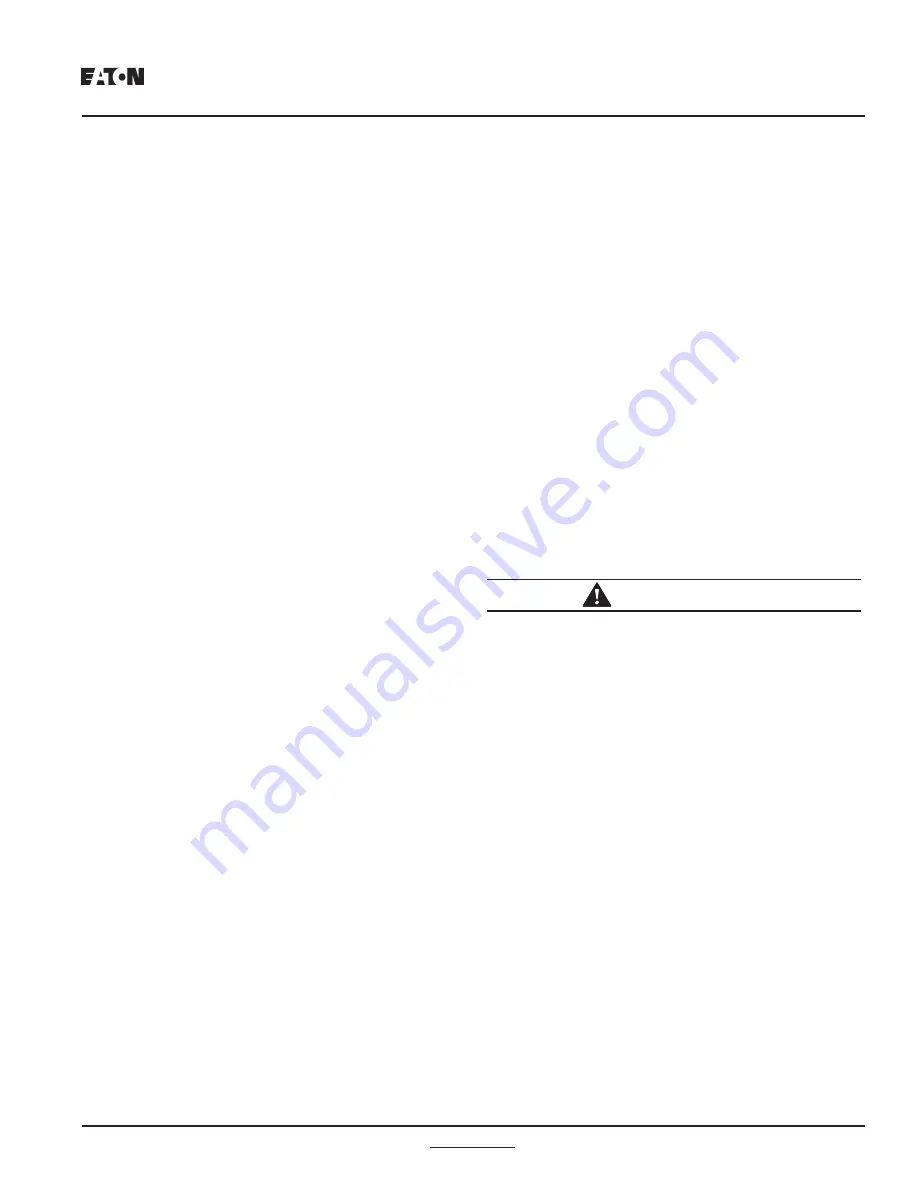
IM02602002E
www.eaton.com
Page
6-1
MP-3000
SECTION 6 - INSTaLLaTION aND WIRING
6.0 Mounting the MP-3000 Motor Protection Relay
The following subsections describe the mounting of the MP-3000 mo
-
tor protection relay, and its optional URTD and PONI communications
modules.
6.0.2 Mounting Locations
Mount the unit vertically on a flat panel. The location should be as free
as possible of water, chemicals, dust, and excessive heat and vibra
-
tion. The panel should protect the User from accidental contact with
live terminals on the back of the MP-3000. A 0.125-in. (3.18-mm) steel
panel or door, solidly grounded, is recommended.
Before actually cutting the panel, check the required three-dimen
-
sional clearances for the MP-3000 case, particularly behind the panel.
Figures 6.2 and 6.3 show these clearances. If mounting the unit on a
swinging door, check the swinging clearance of rear projections and
wired connections.
Figure 6.1 shows dimensions for the panel cutout and mounting holes.
Cutout tolerances and mounting screw hole placement are critical. In
particular, the tolerance of the horizontal dimension between the center
of the mounting holes and the vertical edge of the cutout must be
between 0 and +0.050 in. (+1.273 mm).
NOTE:
The cutout is the same as for the previous-generation IQ 1000
II and MP-3000 motor relays, and other Eaton IQ products of
this case size. The six mounting holes that secure these older
products are still correctly located for the MP-3000, but the four
additional new holes should be added.
Secure the MP-3000 to the panel with the special self-tapping plastic
screws using moderate torque - 8 in.-lbs (0.9 N-m). Use the 0.375-in.
(9.5-mm) long screws supplied with the MP-3000 to mount the unit on
a 0.125-in. (3.18-mm) panel. Do not attempt to tap the screw holes,
and do not use machine screws.
6.0.1 Mounting the URTD Module
The optional URTD module provides temperature data to the MP-3000
from up to 11 RTDs embedded in the motor and driven equipment.
Refer to URTD I.L. 17367 for further information.
The URTD module may be mounted either on the back of the MP-3000
by using the URTD mounting bracket and machine screws (supplied
with the URTD module), or mounted remotely from the MP-3000. If
mounting the URTD module on the back of the MP-3000, see Figure
6.3 for overall depth dimensions. Figure 6.4 shows the URTD stand-
alone mounting dimensions.
Consider the benefit of mounting the URTD module away from the
MP-3000, as close as possible to the motor. The RTD wiring, consist-
ing of a large bundle of wires, is thus much shorter. The URTD conveys
multiplexed temperature data back to the MP-3000 via a single optical
fiber (recommended), or by a 3-wire communications conductor. The
URTD may be placed up to 400 ft (121.9 m) from the MP-3000 with the
optical fiber connection (recommended), or up to 499 ft (152 m) away
with a wired communications connection. Note that the URTD requires
120 Vac power (6 VA) at its remote location. It may be mounted in any
orientation.
6.0.3 Mounting the PONI Communications Module
Refer to Section 10 for a description of the various types of optional
PONI communications modules that can be used with the MP-3000.
Check the I.L. for the selected PONI to confirm dimensions and com
-
munications network connection requirements.
Figure 6.3 shows clearance dimensions to the rear of an I-PONI, M-
PONI, or D-PONI. An E-PONI is 0.5 in. (12.7 mm) deeper.
The PONI, if used, is always mounted on the back of the MP-3000. If
no URTD is mounted there, use the mounting bracket supplied with
the MP-3000, as shown in Figure 6.3. The bracket gives a conve
-
nient space to run CT wires underneath the PONI to the adjacent CT
terminal block.
If a URTD is mounted on the back of the MP-3000, the PONI pig
-
gybacks directly to the URTD module as shown. Use the machine
screws supplied with the PONI in the molded plastic mounting holes of
the URTD.
6.1 Wiring—General Information
When routing wires between the starter and the associated machine
or process equipment, follow these guidelines:
Do not route the control or RTD wiring through the high-volt
-
age compartment of the motor starter. However, the starter
manufacturer may be able to recommend or provide specific
measures for doing this if it is really necessary.
Separate the lower voltage (120 Vac) from the higher volt-
age (440 Vac or higher) conductors as much as possible.
In general, maintain a minimum distance of 1.5 ft (45 cm)
between the two types.
Any low-voltage control wiring routed out of the motor
starter cabinet should be at least #14 AWG (2.6 mm
2
)
stranded copper wire.
Communications circuits may use thinner conductors, as
recommended in installation literature for those circuits.
WaRNING
BEfORE WORKING WITh ThE WIRING, MaKE SURE POWER IS
DISCONNECTED fROM ThE MOTOR STaRTER, MP-3000, aND
aLL REMOTE CONNECTIONS, INCLUDING CONTaCT OUTPUT
CONTROL CIRCUITS aND REMOTE INPUT CONTaCTS. OTh
-
ERWISE, haZaRDOUS VOLTaGES COULD CaUSE INjURy
OR DEaTh. aLSO, UNEXPECTED MOTOR CONTROL aCTION
COULD INjURE PERSONNEL OR DESTROy EQUIPMENT.
Figure 6.5 shows rear terminal connections of the MP-3000.
Connect terminal 5 to the closest solid electrical-safety grounding
point with a heavy wire or braid (#14 AWG [2.6mm
2
] or larger). Do not
use a current-carrying or neutral conductor for this grounding. Also,
do not tie terminal 5 to neutral terminal 7 at the relay. Note that termi
-
nal 5 is internally connected to the outer case and to the conductive
faceplate of the relay.
6.1.1 CT Wiring
Carefully read the advice in Section 5.1.5 on the choice of CT ratios
for a particular motor application. An inappropriate CT ratio results in
poor measurement accuracy and limited protection. More serious er
-
rors in ratio choice make it impossible to set the relay properly.
Connect the phase and optional ground CTs as shown in Figure 6.6.
Pay attention to the phase identification and sequence, and check
for consistent polarity among the three phases. The MP-3000 may
not allow the motor to run, and cannot protect the motor properly, if
two phases are swapped or if the polarity of any CT is reversed with
respect to the other two.
Pass the motor phase conductors through the window of the flux-can
-
celing ground CT. The ground CT need not have any particular polarity
relationship to the phase CTs.
•
•
•
•
Содержание MP-3000
Страница 1: ...IM02602002E www eaton com IM02602002E Rev E MP 3000 Motor Protection Relay ...
Страница 18: ...IM02602002E Page 4 www eaton com MP 3000 This Page Intentionally Left Blank ...
Страница 32: ...IM02602002E Page 4 20 www eaton com MP 3000 This Page Intentionally Left Blank ...
Страница 50: ...IM02602002E Page 6 www eaton com MP 3000 DIMENSIONS IN INCHES CM Figure 6 3 MP 3000 Case Depth Dimensions ...
Страница 53: ...IM02602002E www eaton com Page 6 MP 3000 Figure 6 6 MP 3000 Typical CT Circuit and Motor Control Wiring ...
Страница 54: ...IM02602002E Page 6 10 www eaton com MP 3000 Figure 6 7 Typical AC Supply and URTD Wiring ...
Страница 55: ...IM02602002E www eaton com Page 6 11 MP 3000 Figure 6 8 Alternatives for Discrete Input Wiring ...
Страница 60: ...IM02602002E Page 7 www eaton com MP 3000 This Page Intentionally Left Blank ...
Страница 71: ...IM02602002E www eaton com Page 9 MP 3000 Figure 9 1 Rotor Temperature Tracking ...
Страница 72: ...IM02602002E Page 9 www eaton com MP 3000 Figure 9 2 Motor Protection Curve ...
Страница 73: ...IM02602002E www eaton com Page 9 MP 3000 Figure 9 3 Underload Jam Protection Curve ...
Страница 74: ...IM02602002E Page 9 10 www eaton com MP 3000 Figure 9 4 Motor Protection Curve Example without RTDs ...
Страница 75: ...IM02602002E www eaton com Page 9 11 MP 3000 Figure 9 5 Motor Protection Curve Example with RTDs ...
Страница 76: ...IM02602002E Page 9 12 www eaton com MP 3000 Figure 9 6 Motor Start and Run Cycles ...
Страница 79: ...IM02602002E www eaton com Page 10 MP 3000 Figure 10 1 PONI Communications Module ...
Страница 90: ...IM02602002E Page 12 www eaton com MP 3000 This Page Intentionally Left Blank ...
Страница 99: ...www eaton com MP 3000 IIM02602002E This Page Intentionally Left Blank Page 13 9 ...