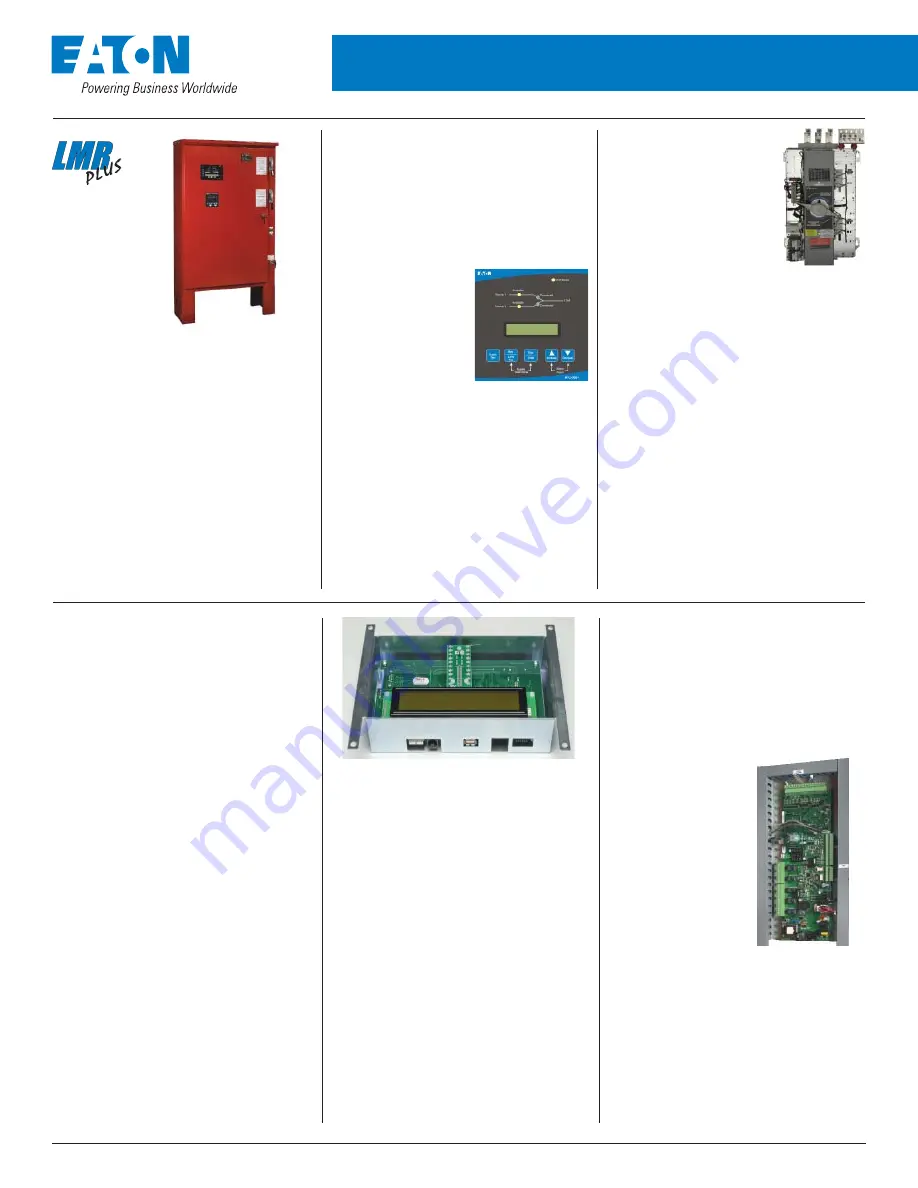
LMR PLUS Electric Fire Pump Controllers with Transfer Switch
Features
1 - 1
For more information visit: www.chfi re.com
BR05805063K/K
January 2012
FT80 Reduced Voltage - Wye Delta (Star-Delta) Closed
The Automatic Transfer Switch Option may be
added to any FD type Fire Pump Controller
whenever automatic transfer from normal to
alternate power is required.
The automatic Transfer Switch and Fire Pump
Controller are mounted in the same enclosure
or in separate enclosures to form one unit and
interwired - depending on the horsepower and
voltage required.
Product Description
Product Features
Engine Test Button
Logic Controller Board
Power I/O Board
Electrically and Mechani-
cally Interlocked
ATC-300 Plus
Automatic Transfer
Voltage and Frequency Sensing
Alarm Relay
Keypad Programming
LED Status Indication
An engine test button is provided on the ATC-
300 controller that can be used to test the
Source 2 (generator) engine. The operator can
select the engine run test time (0-600 minutes).
As well, a silence pushbutton is provided which
de-energizes the alarm bell.
The FT Series transfer switch operating mecha-
nisms are mechanically interlocked to prevent
the normal and alternate source from connect-
ing at the same time.
The switch operates upon signals received from
the ATC-300 Plus controller.
The panel mounted,
multi-function, micropro-
cessor based ATC-300
Plus controller accurately
monitors two power
sources and provides the
necessary intelligence
to reliably operate the
transfer switch through
a series of programmed
sensing and timing func-
tions.
The ATC-300 Plus controller membrane is
equipped with seven keypad input buttons
which are used to program the controller as well
as set operating parameters.
Five LED’s indicate the status of the power
sources.
Source 1 Available Source 1 Connected
Source 2 Available Source 2 Connected
Unit Status
The FT Series Transfer Switches
will perform an automatic
transfer from Normal to Alter-
nate source when the Voltage
drops to 85% of normal, or
there is a loss of any phase
and/or Phase Reversal.
The ATC-300 Plus continuously monitors the
normal source for out of range setpoint values.
When the source is outside the dropout set-
points, the source will become unavailable.
This prompts a transfer to the alternate source.
Retransfer occurs when the normal source’s
frequency and/or voltage return within pickup
setpoints.
The alarm relay is de-energized to indicate an
absence of an alarm state and energized to
indicate the presence of an alarm condition.
Alarm conditions include:
Improper Circuit Breaker Operation
Motor Operator Failure
Lockout
Failsafe Condition
Aborted Engine Test
Aborted Plant Exerciser
Unsuccessful in-phase Transition
The FT80 Transfer Switch Controllers use a
method of connecting the pump motor windings
into wye confi guration to start, then switching to
a delta confi guration to run.
This reduces the starting current of the motor
signifi cantly.
Wye-Delta starting is the only method that has
a starting torque effi ciency of 100%. The FT80
can be programmed for either fully automatic or
semi-automatic operations.
Communication
The controller can be ordered with the option to
display and output current values and status,
on command, from various software protocols
through the appropriate port(s).
Embedded Web Page
The web page is a multifunction tool that allows
the user to view the controller’s current status,
data values, programmed set points and history.
It is accessed using the optional ethernet port.
USB Port / USB Drive
The logic controller board is equipped with a
USB port that can be used to transfer data to
and from a portable USB Drive device (memory
stick).
Ethernet Port
An optional ethernet port is used for direct con-
nection to a computer for data transfer.
RS485 Serial Port
An optional RS485 serial port can be provided
for communication to various external software
programs.
Buzzer
A buzzer is mounted on the logic board which
will operate if Fail to Start, Hardware Malfunc-
tion or any Common Alarm condition exists.
Transformers
Incoming line voltage is run directly to the I/O
board from the incoming lines. The three trans-
formers mounted on the I/O board will accept
voltage inputs between 100 and 600V.
Customer Connection Terminals
Connection terminals for external customer
connections, are located on the top of the
Power I/O board.
Output Relays
Seven socket mount,
8 Amp, 2 Form - C
(DPDT) output relays
are provided standard
on each power I/O board.
They are designated for:
Common Alarm,
Phase Failure,
Phase Reversal,
Pump Run,
Startup,
Acceleration
and Future # 1.
Each socket has an LED mounted on the I/O
board which indicates each relay’s coil status.
Optional Output Relay Boards
T
here is provision to add up to eight additional
relay outputs, via optional relay output boards.
Each board contains a maximum of 2 addi-
tional relays. The Power I/O Board will accept a
maximum of 4 optional boards which mount in a
snap-on confi guration.
Each board provides an area for the user to
label the terminal number and relay name.