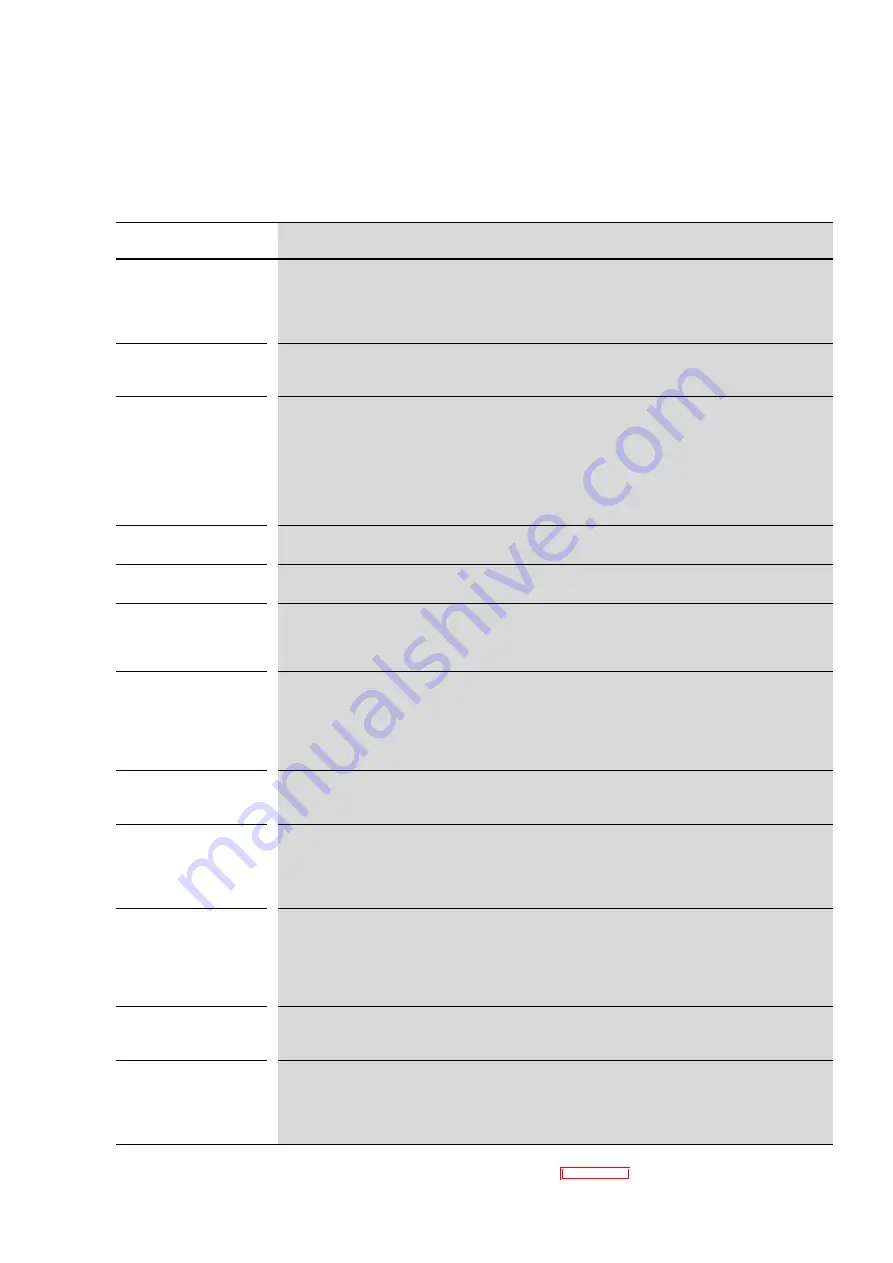
3 Control signal terminals
3.1 Correspondence between inputs/outputs and terminals
DC1…E1 Variable Frequency Drives
11/16 MN040022EN
www.eaton.com
13
The following abbreviations are used throughout this document:
Table 8: Abbreviations
Abbreviation
Significance
AI1 REF
Analog input AI1 (terminal 6)
Used as a speed setpoint input.
• P-16: configuration (voltage input, current input etc.)
• P-35: scaling
• P-39: offset
AI2 REF
Analog input AI2 (terminal 4)
Used as a speed setpoint input.
• P-47: configuration (voltage input, current input etc.)
DIR
Used to select an operating direction
Used together with the START command.
• Low = Forward (FWD )
• High = Anticlockwise operation (REV)
Hint:
If there is a wire breakage and the REV operating direction is selected, this will cause the drive to reverse!
Alternative: Use configuration with FWD/REV.
DOWN
Used to reduce the speed if a digital setpoint value is selected (P-12 = 1 or = 2). Used together with the UP
command.
ENA
Variable frequency drive enable signal
A start signal (START, FWD, REV) is additionally required for starting. If ENA is removed, the drive will coast.
EXTFLT
Ext Fault/Warning
Can be used to integrate an external signal into the variable frequency drive’s fault messages. During operation,
there must be a high-level signal at the terminal. If the unit detects a low-level signal instead, the drive will be
switched off and display
E-trip
as a fault message.
FWD
Used to start the drive in the forward direction (FWD = Forward)
If a high-level signal is applied at the corresponding terminal, the drive will accelerate with the selected ramp.
Removing the signal will cause the drive to stop. In this case, the specific way in which it stops will depend on
the value set for P1-05 (stop mode). Once the variable frequency drive stops, it will be locked.
In applications with two operating directions, the reverse direction can be selected with REV. FWD and REV are
XOR’d. If both signals are applied simultaneously, the drive will ramp down to zero with the quick stop ramp (P-24).
INV
Used to reverse the operating direction
The operating direction will be reversed as per the configured ramps:
Low = do not reverse, High = invert
Pulse FWD (NO)
Pulse REV (NO)
Pulse STOP (NC)
Pulse control
Used to control the drive like a latching reversing contactor circuit. The Pulse STOP signal must always be present
when operating the drive. If the signal is not present, it will not be possible to start the drive / the drive will ramp
down to zero. To start, all that is required is a pulse via the FWD (forward) or REV (reverse) signal.
The FWD and REV signals do not need to be continuously applied during operation.
REV
Used to start the drive in the reverse direction (REV = Reverse)
If a high-level signal is applied at the corresponding terminal, the drive will accelerate with the selected ramp.
Removing the signal will cause the drive to stop. In this case, the specific way in which it stops will depend on
the value set for P-05 (stop mode). Once the variable frequency drive stops, it will be locked.
In applications with two operating directions, the forward direction is selected with FWD. FWD and REV are
XOR’d. If both signals are applied simultaneously, the drive will ramp down to zero with the quick stop ramp (P-24).
Select AI1 REF/AI2 REF
Used to select between the analog setpoint values on AI1 (terminal 6) and AI2 (terminal 4)
• AI1 = Low
• AI2 = High
Select AI1 REF/f-Fix
Used to select between the analog speed reference value at analog input 1 (AI1 = terminal 6) and a fixed
frequency. The fixed frequency itself is selected with the Select f-Fix Bit0, Select f-Fix Bit1, Select f-Fix Bit2
commands.
• Low = analog setpoint value
• High = fixed frequency
Содержание Cutler Hammer PowerXL DC1 E1 Series
Страница 4: ...II...