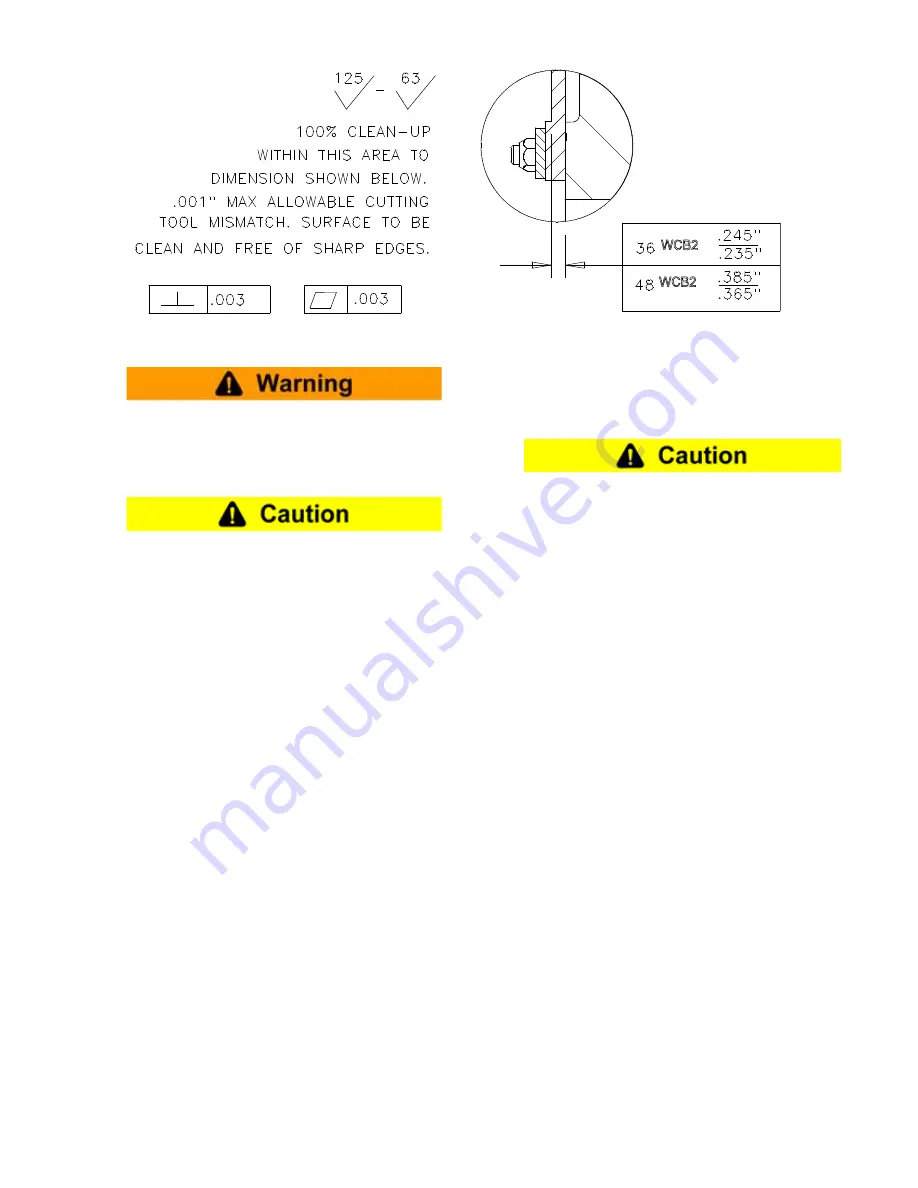
WCB11070 (PDF FORMAT)
21
©
Copyright Eaton Corp. 2007, All Rights reserved.
Figure 18
Failure to machine wear plates flat could
result in poor contact between the friction
couple and subsequent reduction or erratic
torque of the tensioner.
After replacement or machining of wear
plates, a minimum wear-in period of four
hours at 50% of the rated horsepower is rec-
ommended for the friction couple to achieve
rated torque.
4.7
Cylinder Seal Replacement
Note :
Note: Item numbers (#) are shown on
Figures
1 and 2
.
4.7.1
Disconnect the air connections.
4.7.2
While supporting the cylinder, loosen the locknuts (18)
ONE TURN AT TIME and in an alternating (crosswise)
pattern until the spring force is completely relieved.
Remove the locknuts and washers (17). Deep well
sockets are required for removal of the locknuts.
4.7.3
Using lifting equipment, carefully remove the cylinder
(19) and piston (33) as an assembly. Set aside in a
clean area.
4.7.4
Place the cylinder and piston assembly with the piston
facing down on blocks approximately 6" (150 mm)
high. The blocks must only contact the cylinder (19) so
that the piston (33) will be free to move out of the cyl-
inder bore.
4.7.5
If a regulated air line is available, the piston can be
partially ejected from the cylinder by applying no more
than 15 PSIG (1.0 bar) to the cylinder.
Application of a higher pressure may cause
damage to the components.
4.7.6
To complete the removal of the piston from the cylin-
der, open all air inlets. Alternately insert a 0.50" (12
mm) diameter by 6" (150 mm) long wood dowel into
each air inlet and gently tap the piston with a mallet so
that it moves evenly out of the cylinder. Be careful not
to damage the sealing surfaces of the piston or cylin-
der by cocking the piston in the cylinder.
4.7.7
Remove the old seals and discard.
4.7.8
Inspect the cylinder sealing surface condition for nicks
or scratches or any other defect which may prevent
the seals from being effective. See Table 13 for wear
limits of the sealing surface. Replace the cylinder, if
necessary.
4.7.9
Thoroughly clean the seal grooves in the piston (#)
and apply a thin, even coat of Dow Corning
®
55 O-
ring lubricant to the piston seal grooves and chamfer
on the piston, the sealing surfaces in the cylinder (19),
and the seals (21)(23).
4.7.10 Install the new seals in the grooves in the piston,
noting the orientation of the seal lips. See
Figure 19
.
Note :
Some assemblies might have used a one piece
bi-directional lip seal. That type of seal has been
superseded by the use of TWO seals that fit
back-to-back as shown in
Figure 19
.
4.7.11 Position the cylinder on a flat, level surface so that the
pressure cavity faces upward.