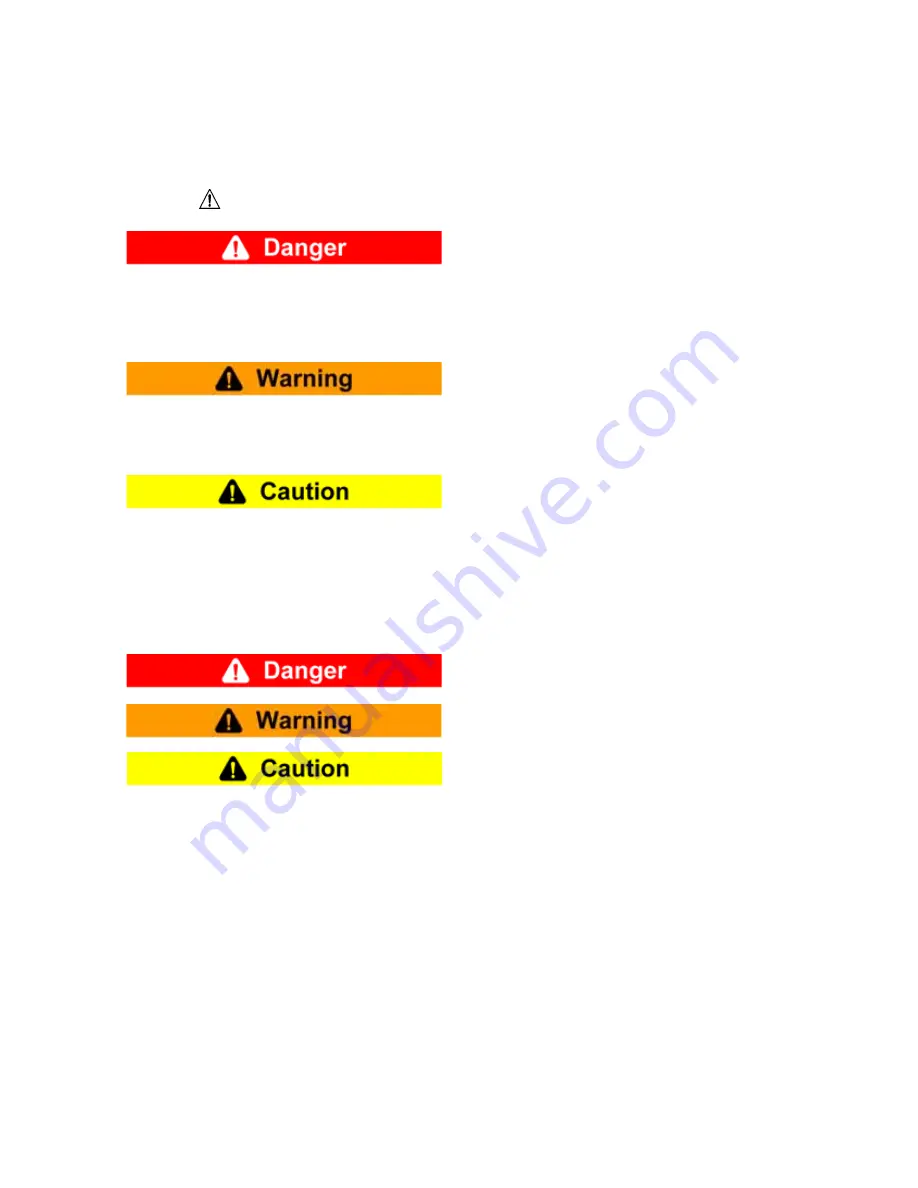
WCB11070 (PDF FORMAT)
3
©
Copyright Eaton Corp. 2007, All Rights reserved.
1.0 INTRODUCTION
Throughout this manual there are a number of HAZ-
ARD WARNINGS that must be read and adhered to in
order to prevent possible personal injury and/or dam-
age to equipment. Three signal words “
DANGER
”,
“
WARNING
” and “
CAUTION
” are used to indicate the
severity of a hazard, and are preceded by the safety
alert symbol
Denotes the most serious hazard, and is used
when serious injury or death WILL result from
misuse or failure to follow specific instruc-
tions.
Used when serious injury or death MAY result
from misuse or failure to follow specific
instructions.
Used when injury or product/equipment dam-
age may result from misuse or failure to fol-
low specific instructions.
It is the responsibility and duty of all personnel
involved in the installation, operation and maintenance
of the equipment on which this device is used to fully
understand the:
procedures by which hazards can be avoided.
1.1
Description
1.1.1
The Airflex
®
WCB2 water-cooled tensioner is
designed for constant tension applications. It is excep-
tionally well suited for high inertia stopping and rapid
heat dissipation. The design of the WCB2 tensioner
permits mid-shaft or end-shaft mounting. The rugged
construction ensures long, trouble free service.
1.1.2
WCB2 tensioners are available in various sizes and
quantities of friction discs. The model number identi-
fies the number of discs and the nominal disc diame-
ter. For example, 324WCB2 indicates three 24"
diameter discs.
1.1.3
When size, such as 36WCB2, is referred to in this
manual, it means that the information given applies to
all models using the 36" diameter watercooled disc
assembly; i.e., 236WCB2, 336WCB2, etc.
1.1.4
Tensioners can be used with either closed loop or
open loop water systems.
1.1.5
This manual includes metric equivalents usually
shown in brackets (#) following the U.S. measurement
system value. Be sure to use the correct value.
1.2
How It Works
1.2.1
Referring to
Figure 1
, the gear (28) is mounted on the
shaft which is to be stopped and the tensioner assem-
bly is attached to the machine frame or a reaction
bracket.
Air pressure is applied through the ports in the cylinder
(19) causing the piston (33) and pressure plate
assembly (13) to move towards the mounting flange,
compressing the release springs. As the applied pres-
sure increases, the friction disc(s) are clamped
between the pressure plate and mounting flange,
stopping or controlling the shaft the discs are mounted
on. Modulation of air pressure then controls applied
torque of the tensioner. Multiple disc brakes utilize
reaction plates (30) between discs. The release
springs (34) assist in disengagement and retraction of
the piston, pressure plate, and reaction plates, if appli-
cable. High heat dissipation is accomplished by pass-
ing water through a special cavity behind the copper
alloy wear plates.
Torque flows through the brake from the shaft to be
controlled, through the friction discs, through the pres-
sure plate and reaction plates, through the clamp
tubes and studs, to the mounting flange, which is
attached to a rigid surface.