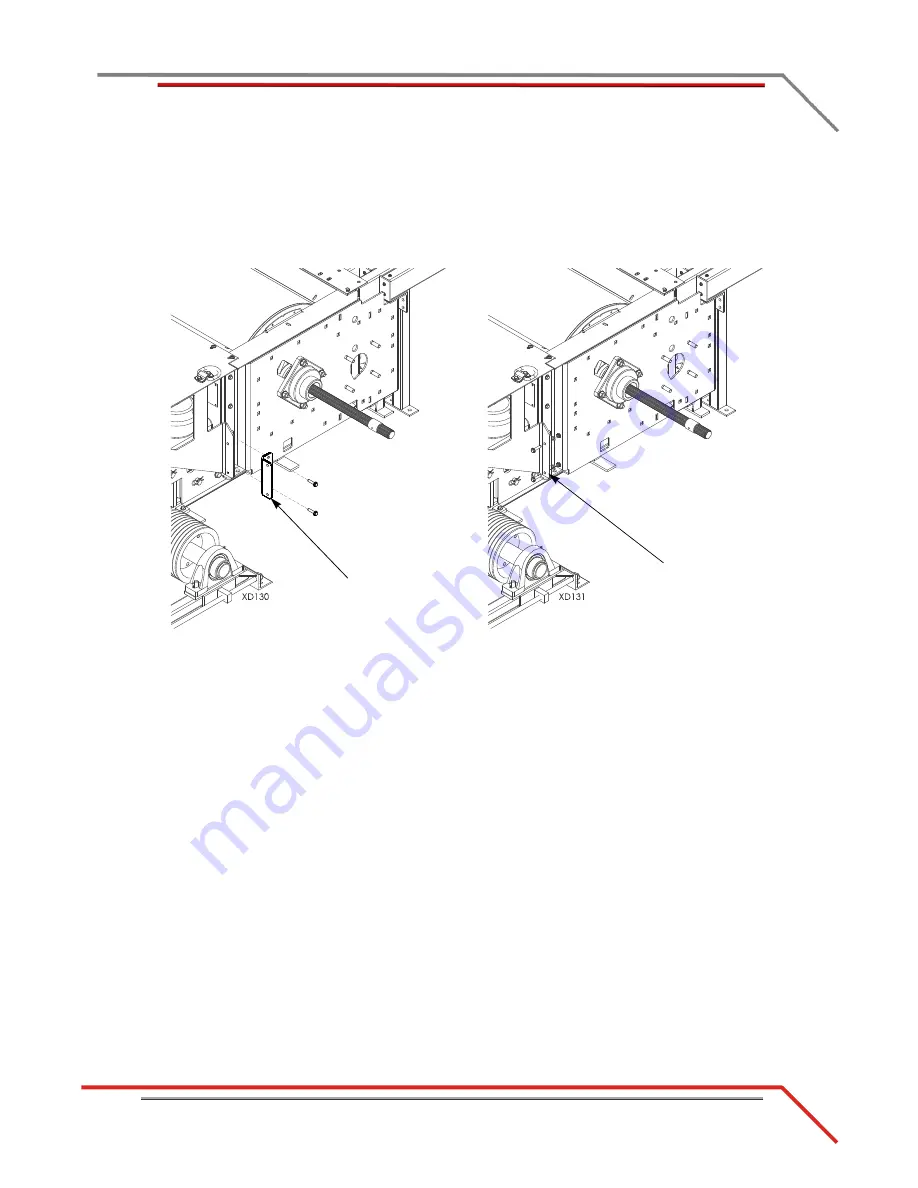
17
L I N X W I T H A T R A F L E X I N S T A L L A T I O N
Inner Mounting Plate and Flange Bearing Installation
Version 3
Linx with Atra Flex Installation for Model 424 Automotive Dynamometers
The following steps are for the above ground dyno only.
6
Secure the rear deck brace mounting bracket to the inner mounting plate and
dyno using the two 3/8-16 x 1.5-inch flange-hex bolts removed earlier.
7
Secure the rear deck brace to the mounting bracket using the two
3/8-16 x 1.5-inch flange-hex bolts, washers, and nuts removed earlier.
Figure 9: Secure the Rear Deck Brace and Mounting Bracket
rear deck brace mounting
bracket
rear deck brace