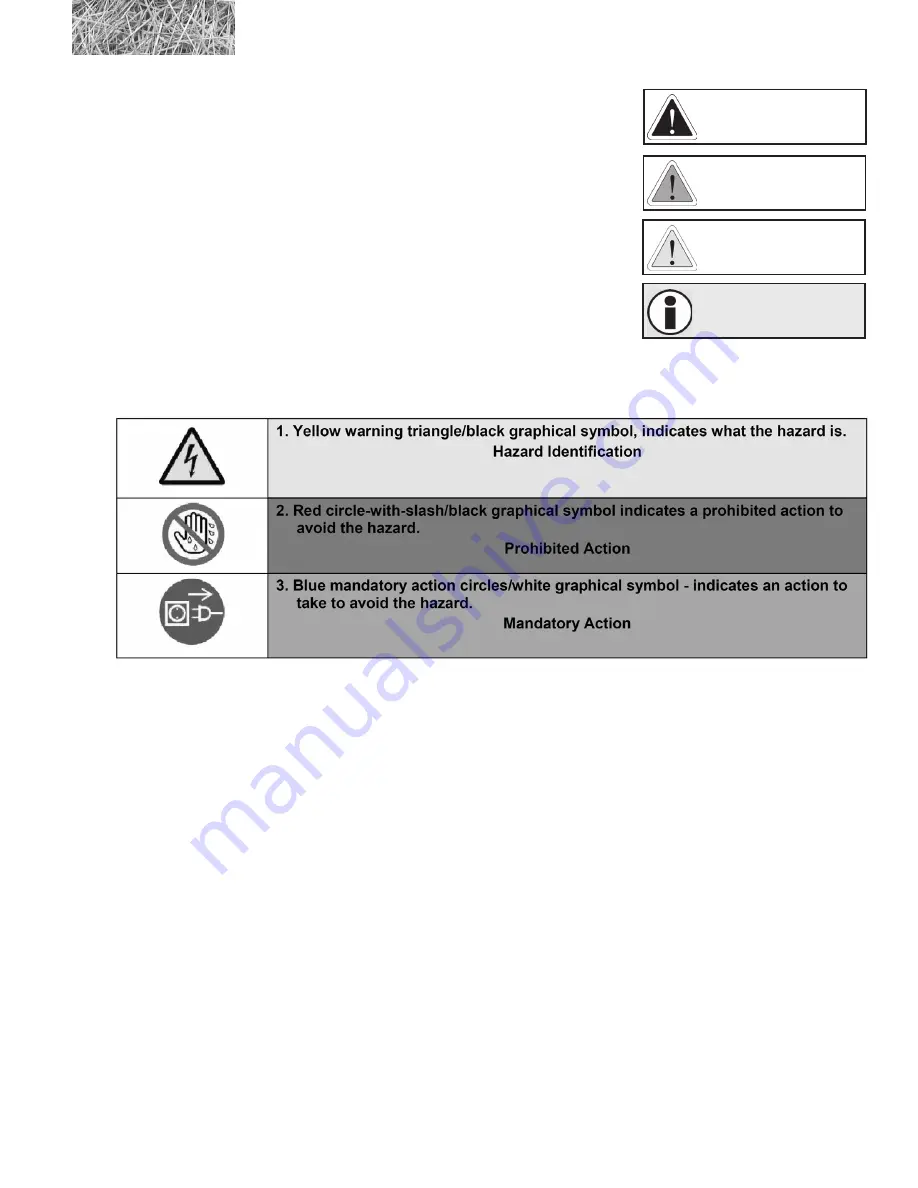
7
1 1 5 0 / 1 1 5 5 H A Y B U S T E R T U B G R I N D E R O P E R A T I N G I N S T R U C T I O N S
This manual uses the symbols to the right to denote
important safety instructions and information.
The
DANGER
,
WARNING
and
CAUTION
symbols
are used to denote conditions as stated in the text above.
Furthermore, the text dealing with these situations is
surrounded by a box with a white background, will begin
with
DANGER
,
WARNING
, or
CAUTION
.
The
INFORMATION
symbol is used to denote important
information or notes in regards to maintenance and use of
the machine. The text for this information is surrounded
by a box with a light grey background, and will begin with
either
Important
or
Note
.
DANGER
INFORMATION
CAUTION
WARNING
Содержание Haybuster 1150
Страница 2: ...A Tradition of Innovation Since 1966 ...
Страница 4: ...A Tradition of Innovation Since 1966 ...