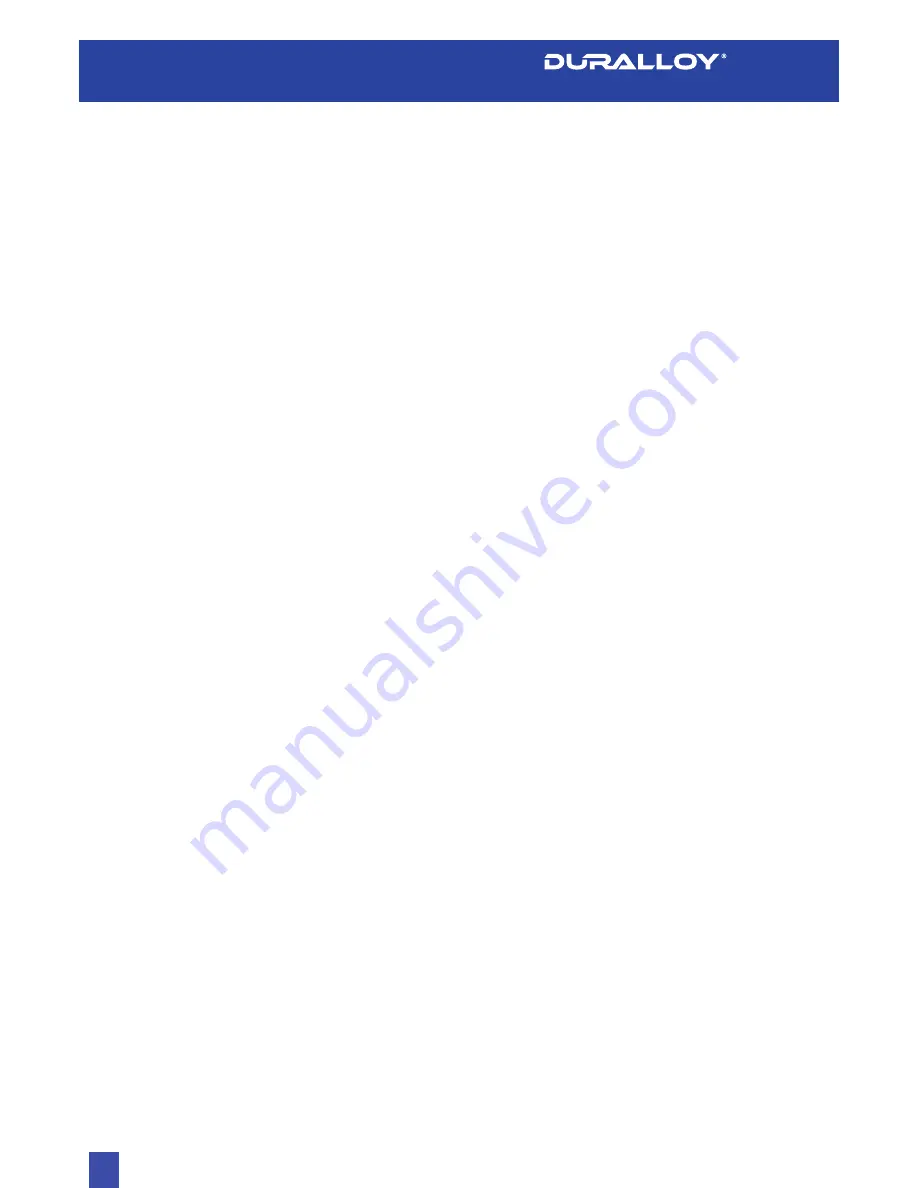
2. Gasless Welding Operation
2.1 Connect the earth cable quick connector to the negative
welding power output socket (11). Connect the earth clamp
to the work piece. Contact with the work piece must be firm
contact with clean, bare metal, with no corrosion, paint or
scale at the contact point.
2.2 Change Polarity link which is situated above Wire feed
system.
2.3 Set the welding voltage adjustment knob (2), wire speed
control knob (1) and wave control knob (9) to the desired
positions. You are now ready to weld!
3. Gas Shielded Welding Operation
3.1 Connect the earth cable quick connector to the negative
welding power output socket (11) Connect the earth clamp
to the work piece. Contact with the work piece must be firm
contact with clean, bare metal, with no corrosion, paint or
scale at the contact point.
3.2 Change polarity Link which is situated above the wire feed
system.
3.3 Assemble the female gas quick connector to the gas line
and to the regulator outlet fitting. Connect the gas regulator
to a gas cylinder (not included with machine) and connect
the female quick connector to the male gas inlet on the rear
of the machine. Ensure all connections are tight. Open gas
cylinder valve and adjust regulator, flow should be between
10-25 l/min depending on application.
3.4 Set the welding voltage adjustment knob (2), wire speed
control knob (1) and wave control knob (9) to the desired
positions. You are now ready to weld!
www.duralloy.net.au
|
1300 369 456
8
Note: MIG welding with aluminium provides a unique challenge, due to
the low column strength of the wire. This causes the wire to deform more
as it is pushed through the feed mechanism and the torch wire delivery
liner, greatly increasing friction. Because good MIG welding results are
dependent on a smooth wire feed, certain changes must be made to the
wire feed system to minimise friction caused issues.
For a standard ‘push’ fed torch, a length of no longer than
3m cable may be used, as well as the torch feed liner must
be changed to a special Teflon/ PVC liner, rather than the
conventional steel liner. Also the correct style drive roller must
be used and specific Aluminium rated torch contact tip (or a
standard tip in one size oversize, e.g. 0.8mm aluminium wire, use
standard 1.0mm contact tip). For this reason, it is quite common
for operators to have an extra MIG torch specifically set up for
aluminium use, if the machine is used for welding steel as well.
MIG 200
OWNER’S MANUAL
Содержание MIG 200
Страница 1: ...MIG 200 OWNER S MANUAL www duralloy net au 1300 369 456 ...
Страница 9: ...www duralloy net au 1300 369 456 WIRING DIAGRAM 9 MIG 200 OWNER S MANUAL ...
Страница 22: ...www duralloy net au 1300 369 456 22 MIG 200 OWNER S MANUAL ...
Страница 23: ...www duralloy net au 1300 369 456 23 MIG 200 OWNER S MANUAL ...
Страница 24: ...www duralloy net au 1300 369 456 ...