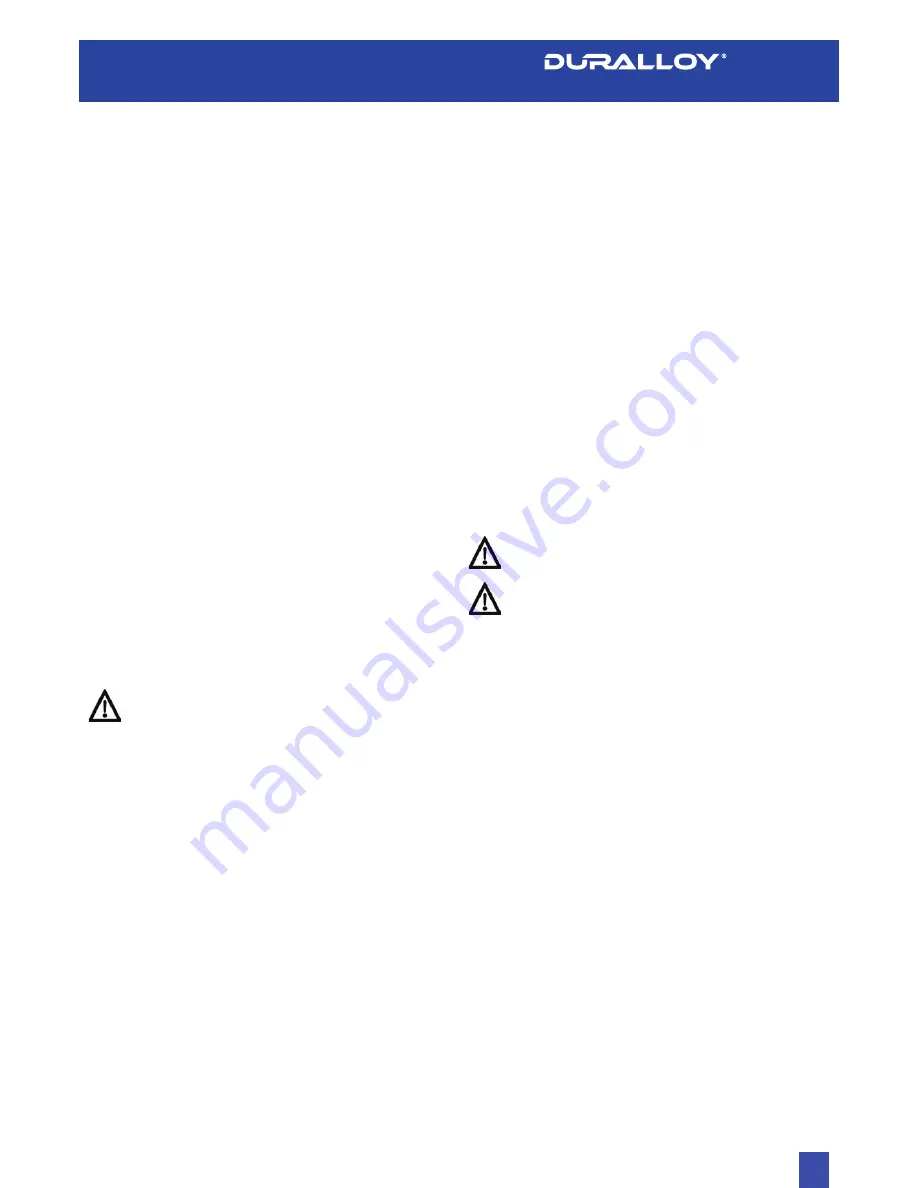
Electrical Connection
The DURALLOY MIG 200 is designed to operate on a 15A 240V
AC power supply. If an extension cord must be used, it should be
a heavy duty version with a minimum cable core size of 2.5mm
2
.
Operating Environment
Adequate ventilation is required to provide proper cooling.
Ensure that the machine is placed on a stable level surface where
clean cool air can easily flow through the unit. The DURALLOY
MIG 200 has electrical components and control circuit boards
which may be damaged by excessive dust and dirt, so a clean
operating environment is important for reliable product life.
BASIC OPERATION
1. Fitting Wire Spool & Loading Wire Feeder
1.1 Open the wire compartment cover. Unthread the wire spool
retainer. Fit the wire spool to spool holder shaft, ensuring that
the wire exits the spool towards the bottom the spool.
1.2 Set the spool brake tension by adjusting the spool tension
adjustment screw before replacing the wire spool retainer.
The spool brake tension should be set so that the spool can
rotate freely, but does not continue to rotate once the wire
feed stops. This may need to be adjusted as the wire is used
up and the spool weight decreases.
WARNING!
Excessive spool brake tension will
cause wire feeding issues and affect welding performance
as well as premature failure/ wear of
wire feed components.
1.3 Feed the wire from the spool through the wire drive inlet
guide into the wire feeder.
1.4 Release the wire feed tension arms by pivoting the wire feed
tension adjustment lever from the vertical to the horizontal
position.
1.5 Check the wire drive roller grooves match the selected MIG
wire type and size. The drive roller will have two different
sized grooves; the size of the groove in use is stamped on
the side of the drive roller. For flux cored ‘soft’ wire, such as
that used in gasless MIG welding, the drive roller groove has
a serrated profile (known as knurled). For solid core ‘hard’ MIG
wire, the drive roller groove used has a ‘V’ shaped profile. For
Aluminium solid core ‘soft’ MIG wire, the drive roller required
has a ‘u’ shaped groove. If necessary, remove and change the
drive roller by unthreading the drive roller retainer.
1.6 Once the correct drive rollers are selected and fitted, manually
feed the wire through the wire drive inlet guide through the
www.duralloy.net.au
|
1300 369 456
drive roller grooves and into the brass outlet wire guide tube.
Ensuring that the wire is correctly seated in the drive roller
grooves, replace the wire feed tension arms and lock them
into place by rotating the wire feed tension adjustment lever
back to the vertical position.
Adjusting wire feed tension: this is accomplished by winding the
knob on the tension adjustment lever. Clockwise will increase
tension, anti-clockwise will decrease drive tension. Ideal tension
is as little as possible, while maintaining a consistent wire feed
with no drive roller slippage.
Check all other causes of excess wire feeding friction causing
slippage first, such as; incorrect/ worn drive roller, worn/ damaged
torch consumables, blocked/damaged torch wire guide liner,
before increasing wire feed tension. There is a number scale on
the tension adjustment lever to indicate the adjustment position.
The higher the number indicated, the higher the tension that is
set.
WARNING!
Before changing the feed roller or wire
spool, ensure that the mains power is switched off.
WARNING!
The use of excessive feed tension will cause
rapid and premature wear of the drive roller, the support
bearing and the drive motor/ gearbox.
1.7 Connect the MIG Torch Euro Connector to the MIG torch Euro
connection socket (12) on the front of the machine. Secure by
firmly hand tightening the threaded collar on the MIG Torch
connector clockwise.
1.8 Check that the correct matching MIG wire, drive rollers and
MIG torch tip are fitted.
1.9 Connect the machine to suitable mains power using the
mains input power lead. Switch the mains power switch to ‘on’
to power up the machine. Adjust the wire feed speed control
(1) to maximum.
1.10 You are now ready to feed the wire through the torch. With
the wire feeder cover open, pull the trigger of the MIG torch
to check that the wire is feeding smoothly through the feeder
and into the torch.
1.11 With the tip removed from the torch and the torch laid out as
straight as possible, activate the torch trigger until the wire
feeds out through the end of the MIG torch. Replace the tip on
the MIG torch and trim off any excess wire.
QUICK START GUIDE - WELDER INSTALLATION
7
MIG 200
OWNER’S MANUAL
Содержание MIG 200
Страница 1: ...MIG 200 OWNER S MANUAL www duralloy net au 1300 369 456 ...
Страница 9: ...www duralloy net au 1300 369 456 WIRING DIAGRAM 9 MIG 200 OWNER S MANUAL ...
Страница 22: ...www duralloy net au 1300 369 456 22 MIG 200 OWNER S MANUAL ...
Страница 23: ...www duralloy net au 1300 369 456 23 MIG 200 OWNER S MANUAL ...
Страница 24: ...www duralloy net au 1300 369 456 ...