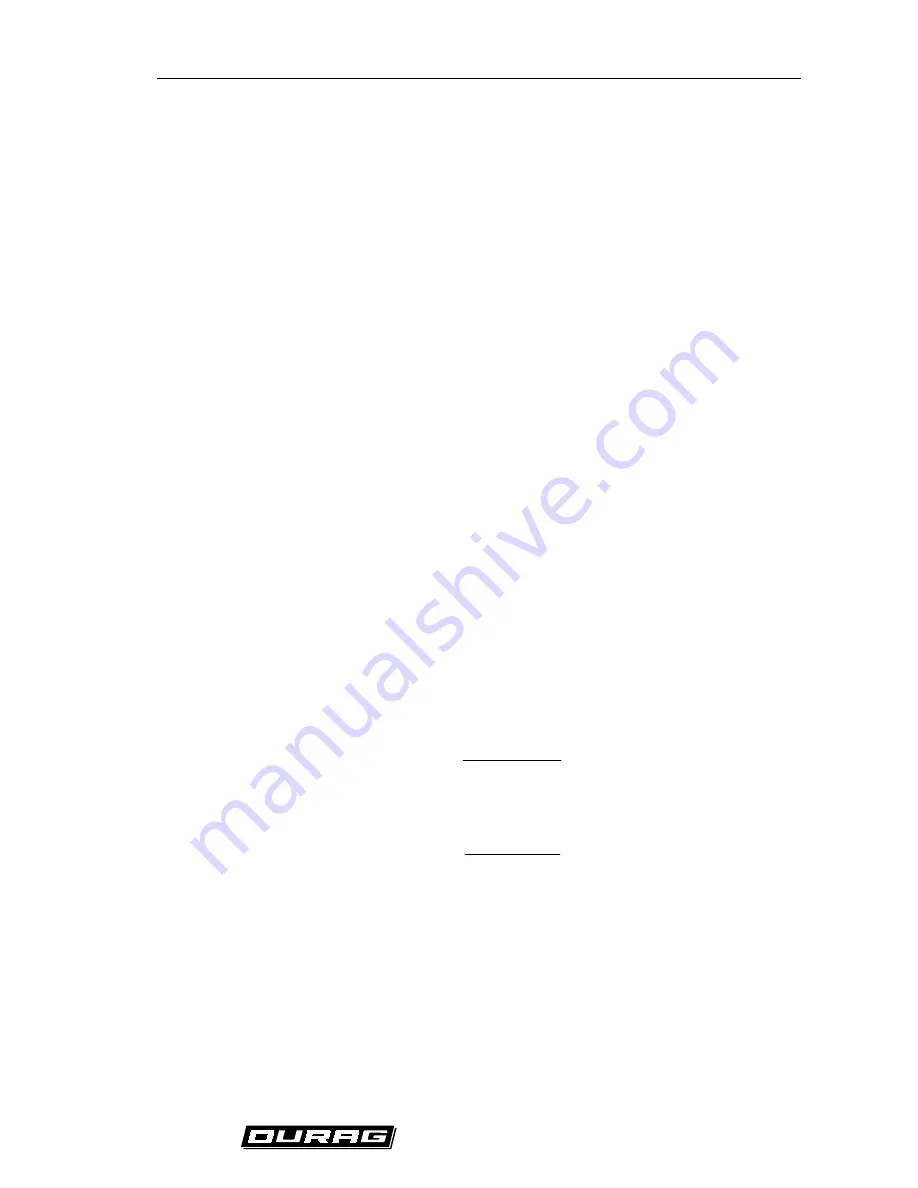
D-FL 200 / Rev. 6
1
______________________________________________________________________________________________________
Industrie Elektronik GmbH & Co KG
1. Application
Acoustic methods of flow measurement use sound waves to determine velocity and flow. The pulse
differential method is among the best known and reliable of such methods. High resolution is achieved
using frequencies in the ultrasonic range.
This monitoring system is applicable in acquiring flue gas volumetric flow in combustion or waste
incineration systems. The system also allows measurements to be made that are otherwise poorly
performed using traditional systems. Measurements in lower velocity ranges are also possible, in
contrast to differential pressure methods. This system is especially advantageous due to its ease of
installation, even on stacks that are wide in diameter.
Acquisition of volumetric flow occurs along the entire profile of the flow. The essential advantage of an
ultrasonic monitoring system is that neither temperature, pressure nor density changes will influence
the measured result. If you want receive the standard volumetric flow you have to consider these three
parameters.
The system is designed for velocities of 0-40 m/s (0-131 ft/sec.) and stack diameters till 5 m (197 in.)
with it measurements up to 0-5,000,000 m³/h (0-approx. 17,7*10
7
ft
3
/h) are possible.
2. Function
The measurement of volumetric flow using ultrasonic probes offers great advantages compared to
conventional methods using differential pressure, since this type of system operates with no moving
parts. Conventional screens heavily choke the overall flow and cause pressure losses. This causes
high energy costs. The employment of dynamic pressure probes requires the use of expensive special
materials if the stack gas is heavily corrosive. In contrast, purge air is used to separate ultrasonic
sensors from the stack gas.
The monitoring system operates using two ultrasonic transducers, which can both transmit and receive
acoustic signals. These transducers are installed in a stack such that the velocity of the acoustic signal
is influenced by the gas flow. That is to say, the gas flow must show properties of a vectorial portion in
the direction of the acoustic signal (see
(Fig. 1) Measuring principle). The ultrasonic sensors are
installed at an angle of about 45° (range 30° - 60°) to the axis of the stack. The transit times of the
acoustic impulses form the basis of the volumetric flow and velocity calculations.
(Fig. 1) Measuring
principle offers a schematic of the monitoring system. The transmitting oscillator receives a keyed
sinusoidal signal and transforms it into an acoustic wave pack whose transit time through the gas
medium is measured. The transit times result as follows:
+
=
+ ⋅
t
L
(c v cos )
α
Equation 1
−
=
⋅
t
L
(c- v cos )
α
Equation 2
with:
t
+
Impulse transit time with the flow
t
-
Impulse transit time against the flow
c
Sonic velocity