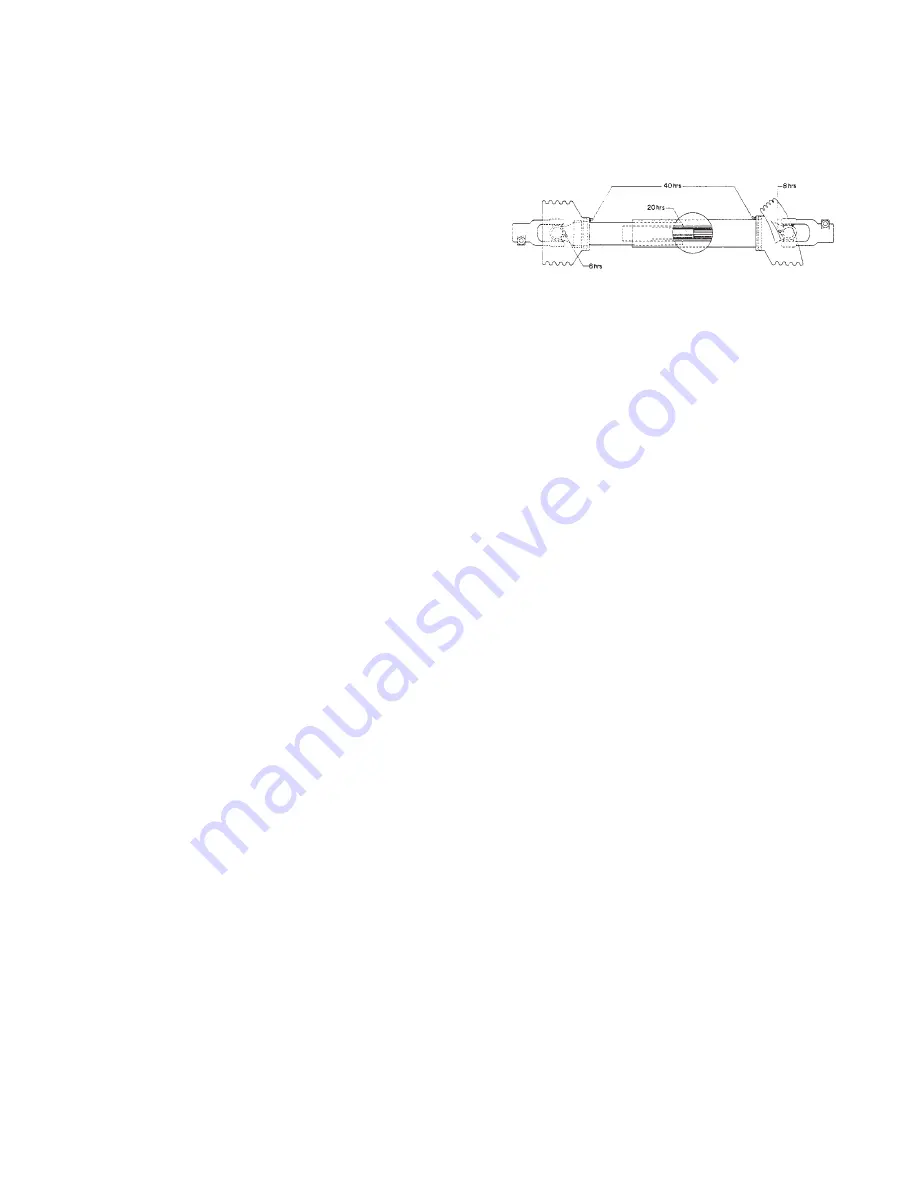
Page 7
60706-133
8290-01
MAINTENANCE
General Information
The main components of the generator are: armature, field
coils, cooling fan, brushes, brush holder assembly, end
brackets, rectifier and voltage regulator. Before performing
any maintenance on the generator, isolate and/or disable the
drive system so the unit can not be accidentally started while
being repaired.
The troubleshooting chart lists various symptoms of poor
generator operation with possible causes and the appro-
priate corrective action. You will need a volt-ohm meter or
test light to check some of the causes. For some of the
other causes you will need to check generator speed. To
check generator speed you can use a frequency meter, a
tachometer, or a 120V-60Hz electric clock and a correctly
operating wrist watch. (Run the electric clock on generator
power and compare the clock’s second hand movement
with that of the wrist watch. They should run at the same
speed. If clock runs faster, generator speed is too high,
and vice versa.)
CAUTION: Equipment Damage
Most electrical equipment in North America operates
satisfactorily at frequencies between 58.5 and 62 Hz
(cycles per second.) Operating the generator at frequen-
cies outside that range may cause damage to the genera-
tor and/or to electrical equipment driven by the generator.
Periodical Maintenance
Service/maintenance items include periodic external physi-
cal inspection for missing hardware or damage to mounting
or drive system and checking the oil level in the gear case.
It is recommended that the generator be operated at least
monthly under normal loads to familiarize operators with the
procedures and controls as well as to dry out any accumu-
lated condensation or other moisture in the generator elec-
trical windings. The maintenance and service attention
invested will insure getting the peak performance that was
designed into the unit.
Routine preventive maintenance minimizes costly repairs
and generator down-time. Before each use, inspect the
generator: gear case oil level should be correct, cooling
vents and screens should be clear, and generator mount-
ing hardware should be tight. Clean and inspect the
generator after storing it for long periods, and after using
it in extremely dusty conditions or in severe weather, such
as rain or blowing snow.
Lubrication
The generator bearings are factory lubricated and sealed,
and require no further lubrication.
The generator input shaft should be cleaned and lubricated
with a thin film of grease before installing the drive shaft and
each time it is removed.
The drive shaft (tumbling bar) requires greasing. Keep the
universal joints in the coupling shaft free from grease and dirt
buildup.
NOTE:
Do not over lubricate the universal joints.
Check the generator gear case oil level before each use of
the generator. Maintain the oil level at oil level plug height.
(See page 6 for oil level plug location.) The generator is
shipped with lubricant in the gear case. Specifications for
gear case lubricant are:
API Service: GL-5
Grade: SAE 85W-9O-140
Amount: 2 pints
The following kinds of oil are recommended for use in the
generator gear case: Mobil SAE 85W90-140 API Service GL-
5, Sunoco/DX XL80W90-140 Kendal Three Star 85W-140,
Amoco 85W140 or equivalent.
CAUTION: Equipment Damage
Do not overfill generator gear case. Overfilling causes
overheating and oil seal failure.
Change the oil at least once every six months. Change it
more often if you use the generator in bad weather. Use the
following procedure to change generator gear case oil:
1.
Remove gear case breather. Soak breather in cleaning
solvent, then allow it to dry.
2.
Remove oil level check plug.
3.
Remove the oil drain plug, drain the oil into a clean oil
resistant container, 1 quart or larger. Check the oil for
metal. Fine metal dust in the oil does not indicate
trouble, but metal chips do. Dismantle the gear case and
look for damaged gears if you find metal chips in the oil.
4.
Replace the oil drain plug. Refill the gear case through
the breather port with new oil of the recommended type.
Fill the case up to oil level check plug height. (It will take
about 1 pint.)
5.
Replace the oil level check plug.
6.
Replace the breather
Cleaning and Inspection
Use a vacuum cleaner or dry low pressure compressed air
(regulated at 25-35 PSI) to clean the generator periodically.
WARNING
DO NOT CLEAN THE GENERATOR WHILE IT IS RUNNING.