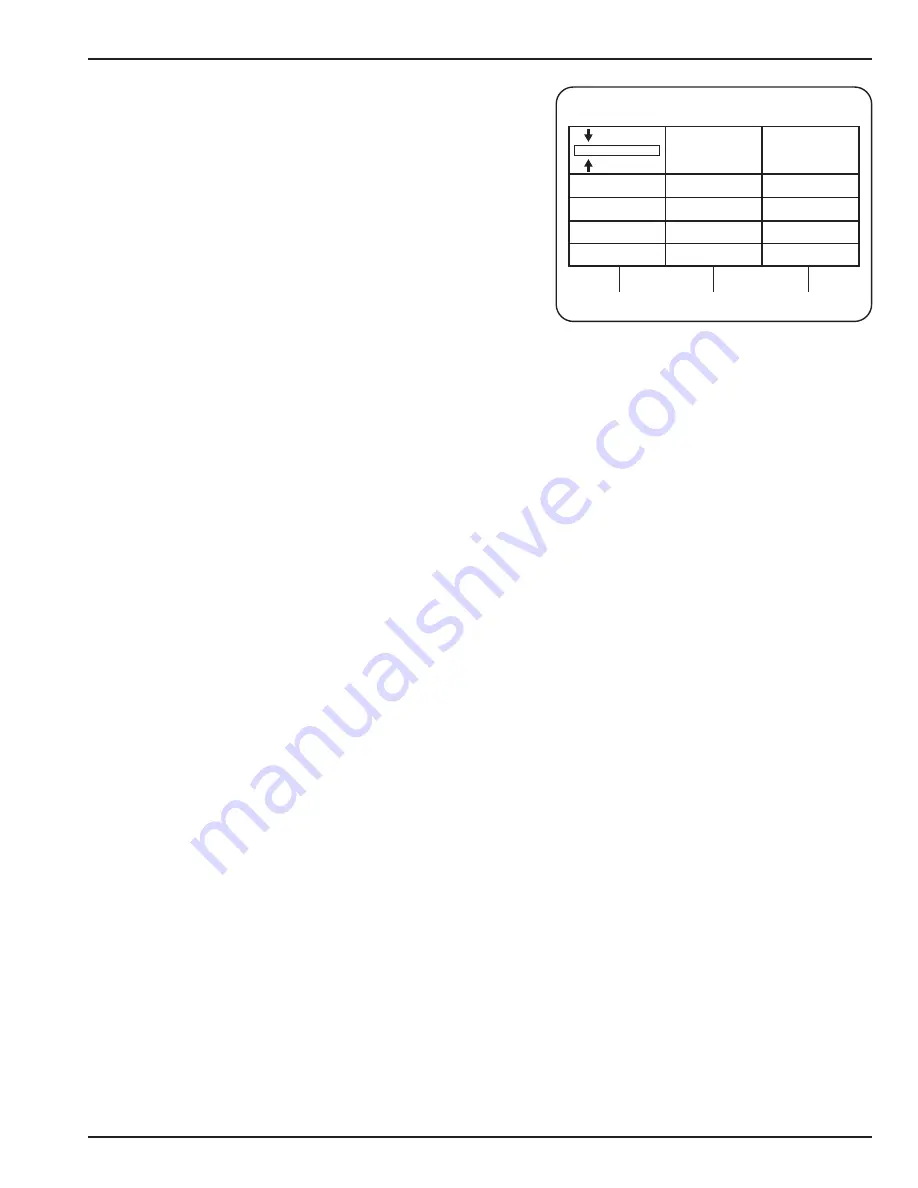
16
9. SETTING THE ARC WELDER
NOTE:
Remove the plug from the socket before
carrying out adjustment, servicing or maintenance.
Check that the electrical supply delivers the voltage
and frequency corresponding to the welding
machine and that it is fitted with a delayed fuse
suited to the maximum delivered rated current.
NOTE:
The welding machines are set to the highest
voltage at the factory.
9.2 PREPARING THE WELDING CIRCUIT
Connect the ground “lead” to the piece to be
welded. Connect the welding electrode to the
electrode holder.
When the machine is turned on and the electrode
touches, the workpiece, the electrical circuit is
complete, this will result in the welding arc being
produced.
NOTE:
Once you have put the welding machine into
operation, switch it on and carry out the required
adjustments.
9.3 ADJUSTING THE WELDING CURRENT
Select the welding current depending on the
electrode, the joint and the welding position.
Indicatively, the currents to be used with the
different electrode diameters are listed in Fig.1.
NOTE:
Do not force the adjustment flywheel as this
could damage the welding machine. Check the
adjustment on the current adjustment indicator.
NOTE:
To strike the welding arc with the coated
electrode, brush it onto the piece to be welded and
as soon as the arc is struck, hold it constantly at a
distance equal to the electrode diameter and at an
angle of approximately 20-30 degrees in the
direction in which you are welding.
9.4 THERMAL CUTOUT SIGNAL
The warning light switched on means that the
thermal protection is running.
If the welding time “tw” indicated in the data plate
is exceeded, a thermal cutout stops operation
before the welder is damaged. Wait for operation
to be resumed and, if possible, wait a few minutes
more.
If the thermal cutout continues to cut in, the
welding machine is being pushed beyond its normal
performance levels.
FIG. 1
1
2
3
1
Plate thickness
2
RCD Diameter
3
Welding amperage
1,0
1,6
30 – 50
mm
Ø
mm
AMP
2,0 – 3,5
2,0
50 – 75
2,5 – 3,0
2,5
75 – 105
3,0 – 4,0
3,2
105 – 140