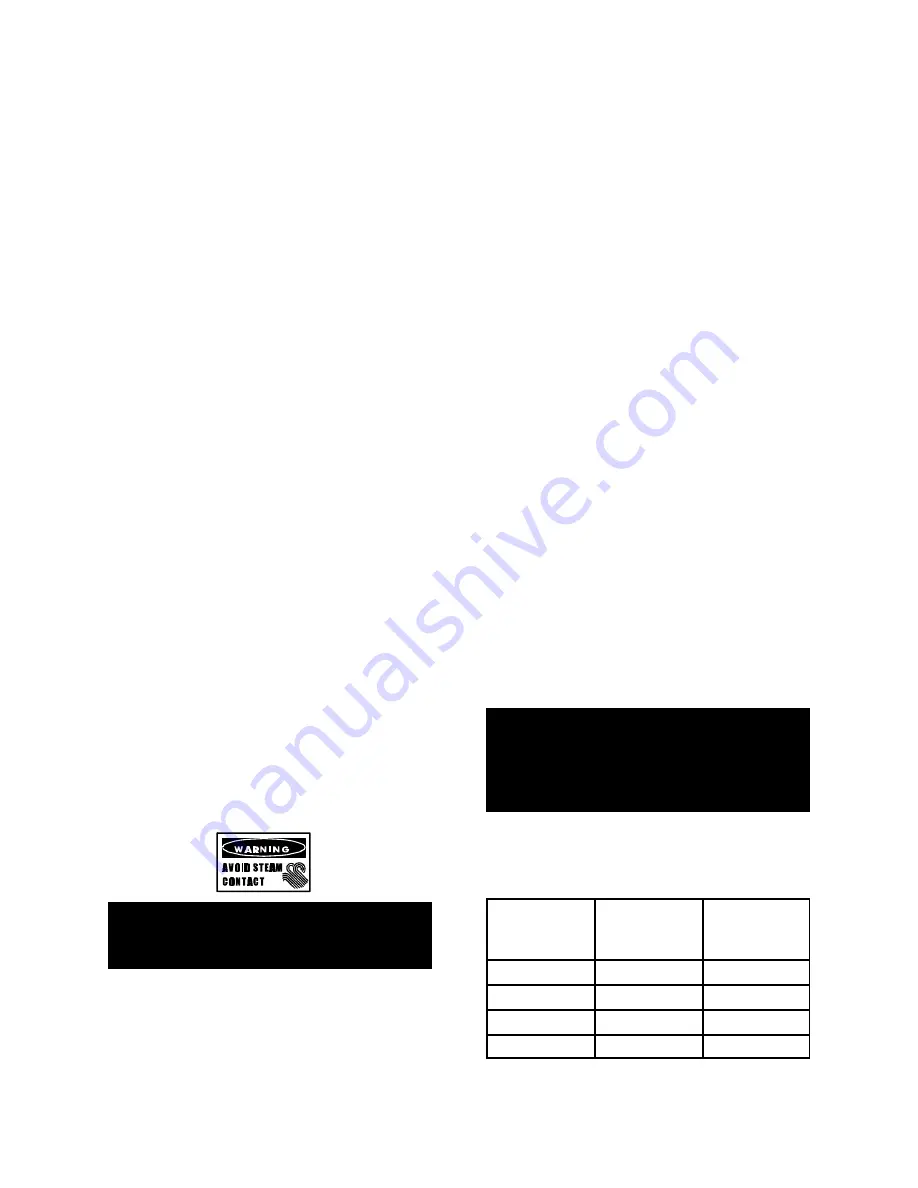
OM/SM-AH-CE
10
i.
See appropriate ASME Boiler and Pressure
Vessel Code for additional installation
instructions.
3.1
Conversion — NOTE:
See Para 1.9
and 1.10 (Page 6) for important gas
proper level, either because water was lost as
conversion information. VERIFY
steam during venting or because treated water
THE TYPE OF GAS TO BE USED. In
was lost by draining.
the countries listed in Paragraph 1.10
all conversions must be for approved
The procedure for adding water is as follows:
gas
.
To change the type of gas used (e.g. G20 to
G25 or G31 or the like), change the following:
Burner injector
Pilot orifice
Pressure setting
Data Plate
The governor spring does not need to be
changed- only the pressure setting.
3.2
Jacket Vacuum
When the kettle is cold, a reading that is
positive or near zero on the pressure/vacuum
gauge indicates excess air in the jacket. Air in
the jacket slows down the heating of the kettle.
To remove air:
a.
Light the unit (see Section 2.5.1).
b.
When the pressure/vacuum gauge reaches
a positive reading of five PSIG, release air
and steam by lifting the lever on the safety
valve for about 1 second. Repeat this
process a few times, then let the valve snap
back into the closed position.
See detailed Instructions on Page 8 pertaining
to Safety Valve installation and operation.
WARNING
AVOID ANY EXPOSURE TO THE STEAM
BLOWING OUT OF THE SAFETY VALVE.
3.3
Jacket Filling
The jacket has been charged at the factory with
the proper amount of treated distilled water. You
may need to restore the jacket water to its
a.
If you are replacing water lost as steam use
distilled water. If you are replacing treated
water that was removed from the jacket,
prepare more as directed below.
b.
Allow the kettle to cool completely. Using
the proper sized spanner, remove the pipe
plug from above the globe valve.
c.
Open the globe valve and pour distilled or
treated water in the pipe plug orifice. (See
“Water Treatment Procedure,” Paragraph
3.4). Hold the safety valve open while you
pour, to let air escape from the jacket.
d.
Air introduced to the jacket during the filling
operation must be removed to obtain
efficient heating. (See "Jacket Vacuum"
section 3.2).
See detailed Instructions on Page 8 pertaining
to Safety Valve installation and operation.
3.4 Water Treatment Procedure
WARNING
READ AND FOLLOW ALL PRECAUTIONS
STATED ON THE LABEL OF THE WATER
TREATMENT COMPOUND TO AVOID
INJURY.
a.
Fill the mixing container with the measured
amount of water required. (See Table). Use
distilled water only.
Model
Capacity
Kettle
Capacity
Jacket
(Approx)
AH-20
75.7 Liters
17 Liters
AH-40
151.4 Liters
26.5 Liters
AH-60
227.1 Liters
35.9 Liters
AH-80
302.8 Liters
43.5 Liters
Содержание GROEN AH-20
Страница 23: ...OM SM AH CE 23 ...
Страница 24: ...OM SM AH CE 24 Parts Lists ...