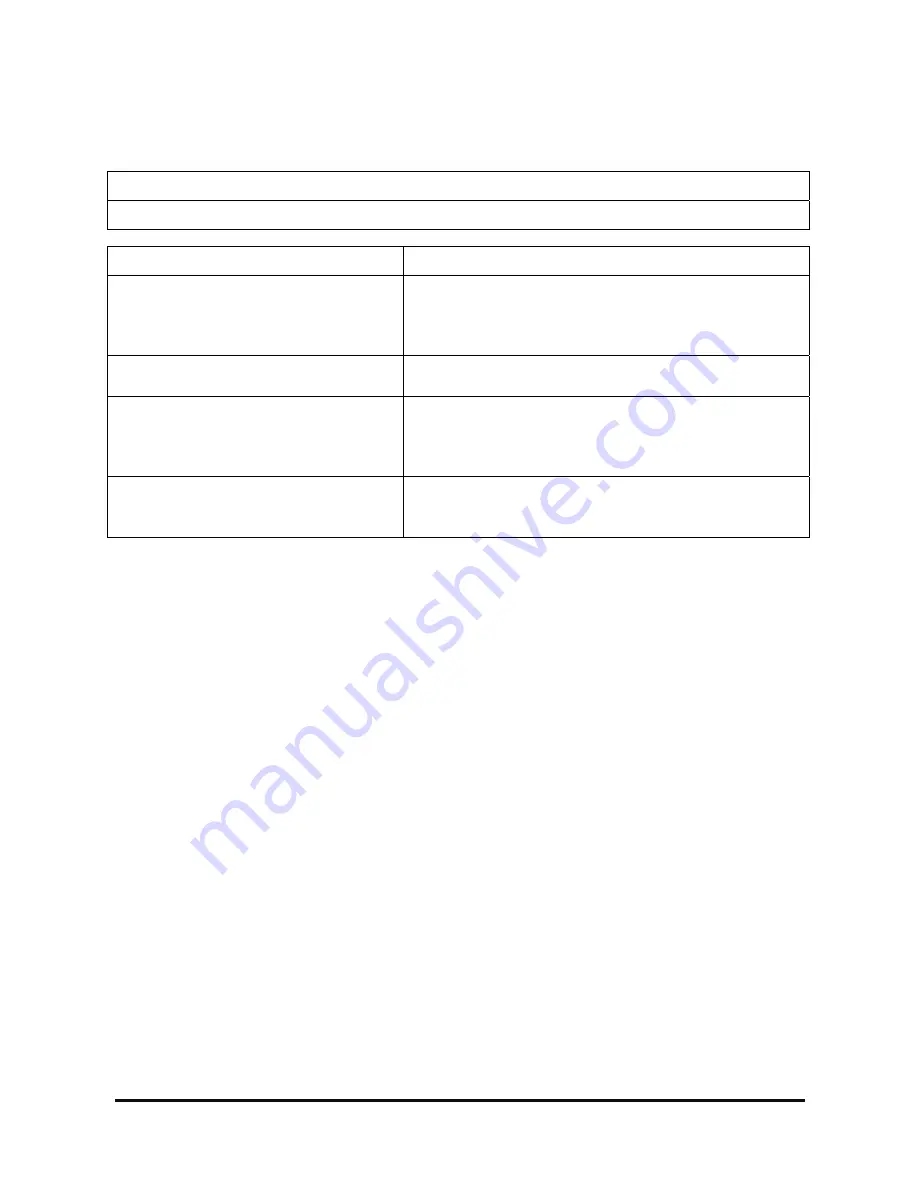
G424F(FE) Service Manual
245
Chapter 8. Basic Troubleshooting
High Idle Speed
Engine idles above the range of 750-1100 rpm.
PRELIMINARY CHECKS
Perform the visual checks as described at start of “ Basic Troubleshooting” chapter.
PROBABLE CAUSE
CORRECTIVE ACTION
Incorrect idle speed control
Check all hoses and gaskets for cracking, kinks, or leaks.
Verify that there are no vacuum leaks.
See Chapter 8 Advanced Diagnostics & Chapter 6 Tests and
Adjustments
Throttle sticking
Replace throttle.
See Fault Code 461: ETC_Sticking
Foot pedal sticking or incorrect pedal signal
Check pedal return spring travel for binding.
Check APP function with Service Tool.
Verify smooth change of APP reading with pedal movement.
See Chapter 8 Advanced Diagnostics.
Engine mechanical
Check for vacuum hose leak.
Check for PCV malfunction.
Check for defective intake gasket.
Related MIL Faults:
ETC Sticking fault
Idle adapt out of range
MAP Sticking fault
MAP high value
Содержание G20P-5
Страница 2: ......
Страница 4: ......
Страница 31: ...G424F FE Service Manual Chapter 2 Recommended Maintenance 29 ...
Страница 36: ...G424F FE Service Manual Chapter 3 Engine Mechanical System 34 MAIN BEARINGS 0 50 UNDERSIZE ...
Страница 86: ...G424F FE Service Manual Chapter 3 Engine Mechanical System 84 ...
Страница 113: ...G424F FE Service Manual Chapter 4 Engine Electrical System 111 2 Alternator and outer terminal connection inspection ...
Страница 153: ...G424F FE Service Manual Chapter 5 Engine Management System EMS 151 Figure 22 SECM Wiring Diagram for G424FE LP System ...
Страница 162: ...G424F FE Service Manual Chapter 5 Engine Management System EMS 160 SECM Wiring Diagrams for G424F LP Engine ...
Страница 230: ...G424F FE Service Manual 228 Chapter 8 Basic Troubleshooting Irregular Idling Or Engine Is Suddenly Stopped ...
Страница 231: ...G424F FE Service Manual 229 Chapter 8 Basic Troubleshooting Engine Hesitation Or Insuffient Accelelation ...
Страница 232: ...G424F FE Service Manual 230 Chapter 8 Basic Troubleshooting ...
Страница 234: ...G424F FE Service Manual 232 Chapter 8 Basic Troubleshooting ...