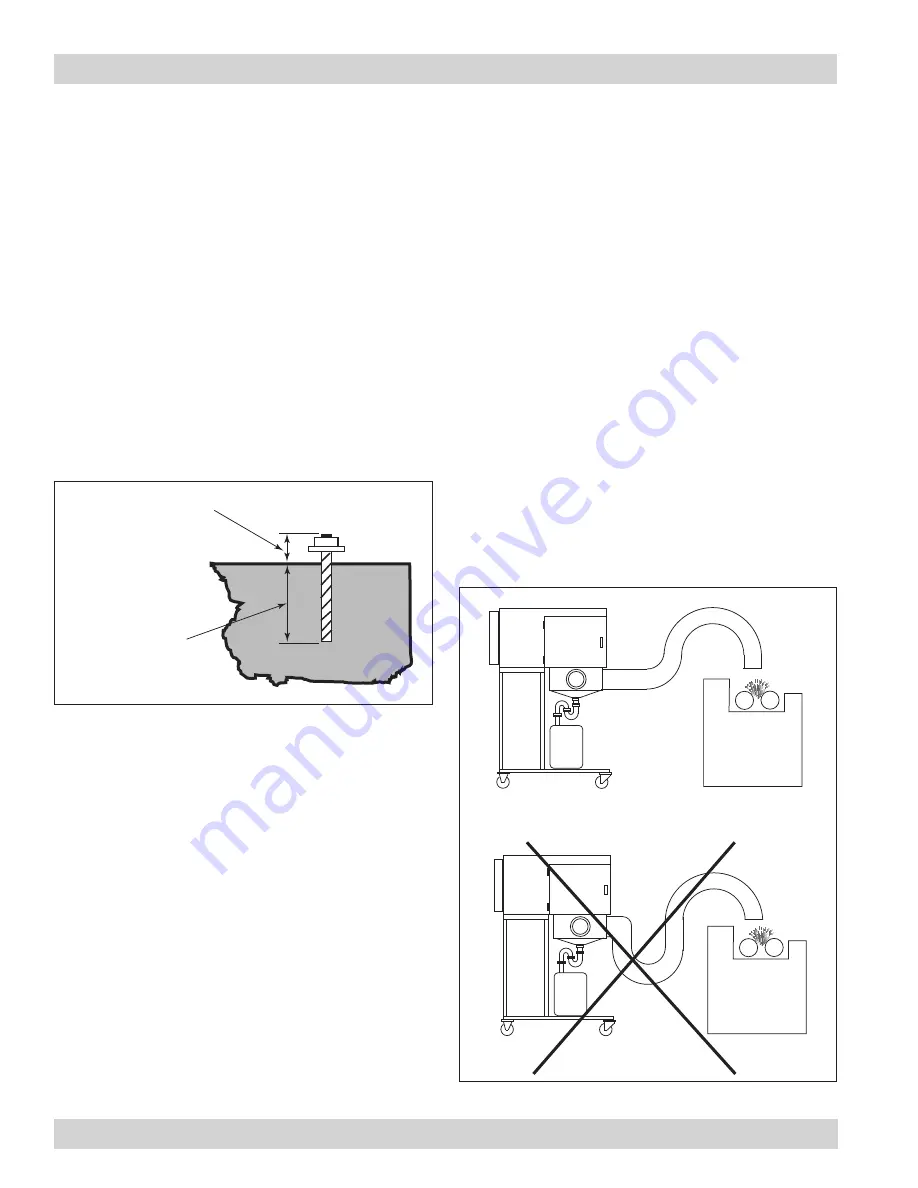
7
Donaldson Company, Inc.
Standard Equipment
Anchor should project
a minimum of 1 3/4-in
and account for nut,
washer, base plate
and shims/grout.
Embedment depth
Typical Foundation Anchor
Provisional Anchor Bolt Recommendations
1. Consider Hilti HIT-HY 200 Anchor System or
equivalent. Quantity of anchor bolts should match the
number of holes provided in the base plates.
2. Anchor diameter is typically 1/8-in less than
baseplate hole diameter.
3. Corrosive environment or outdoor installation may
require stainless steel anchors.
General Installation
1. Apply a generous amount of sealant when installing
attachments.
2. Position the collector above the mist-capture zone.
See Collector Positioning.
3. Do not allow a P-Trap to form when using flexible
duct. See Flex-Duct Positioning.
4. On enclosed-machine installations, mount the unit
as far from the chip conveyor opening as possible.
Installing too close allows the negative pressure
created by the unit to draw clean shop air, not
mist, into the collector. See Enclosed-Machine
Installation.
5. On open-machine installations, position the unit’s
pick-up hood a minimum of 305 mm (12-inches) from
the mist source. Avoid mounting the pick-up hood too
close to the mist source of an open machine such
as a wet surface grinder. Installing too close can
shorten filter life as the unit will collect large droplets
and particulate instead of mist. See Open Machine
Installation.
A variety of configuration and mounting options are
available with the WSO M. The WSO M can be mounted
directly on the roof of a machining center, suspended
overhead, or stand-mounted.
machine
center
Correct
machine
center
Incorrect
P-trap
Flex Duct Positioning
Содержание WSO M
Страница 25: ...WSO Mist Collector WSO M 22 Service Notes Date Service Performed Notes ...
Страница 26: ...23 Donaldson Company Inc Service Notes Date Service Performed Notes ...
Страница 27: ......