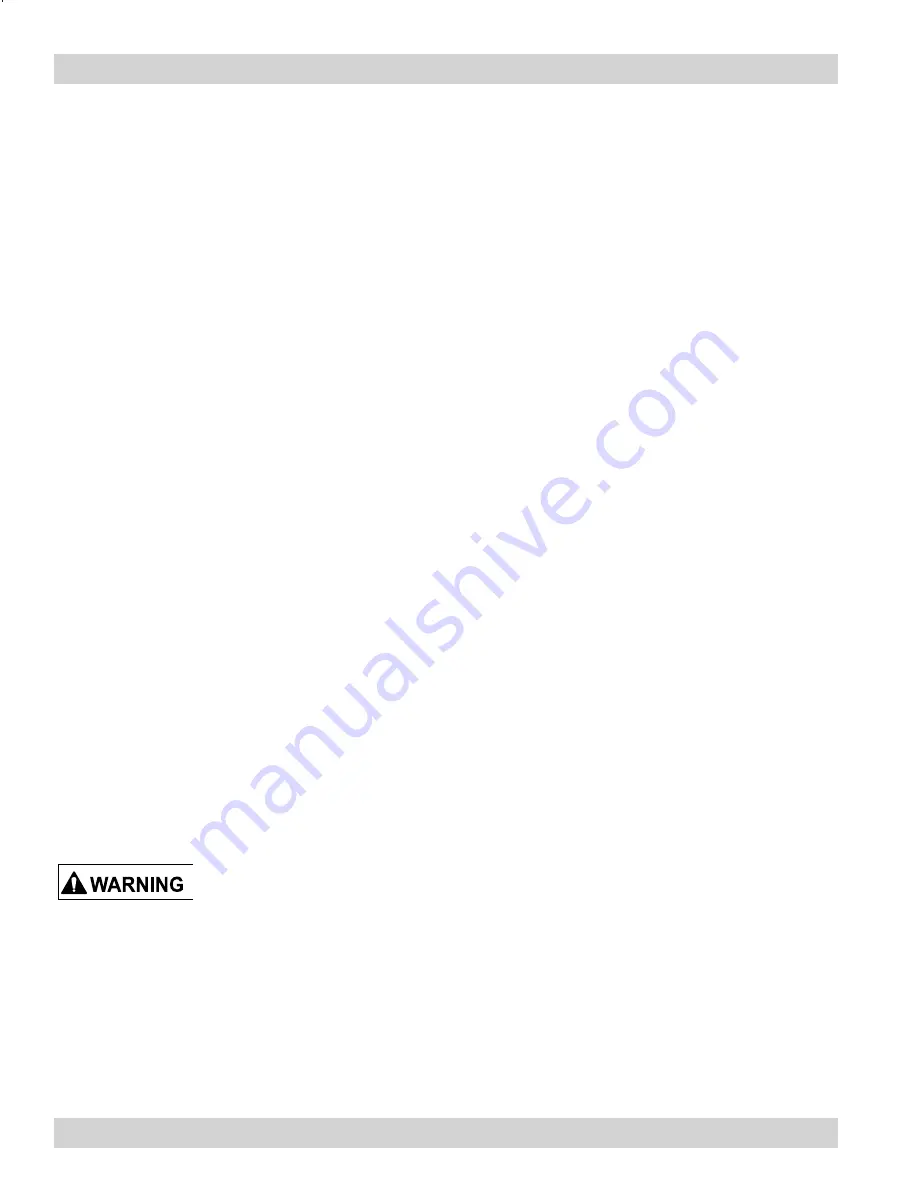
Combustible materials such as buffing lint, paper, wood, metal dusts, weld fume, or flammable
coolants or solvents represent potential fire and/or explosion hazards. Use special care when
selecting, installing, and operating all dust, fume, or mist collection equipment when such combustible
materials may be present in order to protect workers and property from serious injury or damage due to a
fire and/or explosion.
Consult and comply with all National and Local Codes related to fire and/or explosion properties of
combustible materials when determining the location and operation of all dust, fume, or mist collection
equipment.
Standard Donaldson Torit equipment is not equipped with fire extinguishing or explosion protection systems.
1
Donaldson Company, Inc.
Description
The Downflo WorkStation, DWS, is a continuous duty,
self contained, modular workstation with oval cartridge
style filters. Continuous duty means the filters can be
pulse cleaned - one at a time, without turning the unit
off. The modular design creates a custom unit for each
application. The DWS power module includes a blower,
DWS 4 or DWS 6 filter modules, two (2) dust drawers
(available in either metal or plastic), a louver air inlet that
can be located in a high or low position, and a ledge less
design to reduce dust build up in the collector. Models
DWS 4-1, 4-2, 4-3, 4-4, and DWS 6-1, 6-2, 6-3, 6-4 power
modules can have joining strips to tie modules together.
Optional booths can be applied for all models. Designed
to increase versatility of the unit, standard options
include heavy duty wall and ceiling acoustic panels. They
also include a ceiling light for each power module on
hard sided and roof booths in dust tight or flush mounting
lighting. Soft side weld and acoustical curtain booths are
also available with a clear plastic ceiling to allow plant
light to illuminate the booth. Also, a moveable side shield
with canopy booth is available for one module and two
module configurations.
Purpose and Intended Use
The DWS is commonly installed in applications where
dust containment and noise control from a specific
operation are required. Typical applications include;
abrasive blasting, batch mixing, composite grinding, and
metal grinding.
While the DWS effectively contains dust and controls
much of the noise generated within the work area,
it does not provide source capture of dust and some
noise will be emitted from the booth. The 160 fpm indraft
velocity is sufficient to prevent nuisance dust from
escaping the DWS.
Abrasive Blasting
Abrasion-resistant options include an open louver inlet
and smooth wall booth. Recommended options include,
a control panel for reduced installation expense, flush
lights for increased headroom, and ASHRAE or HEPA
afterfilters for added safety on hazardous dust.
Batch Mixing
Dumping and mixing operations often produce significant
amounts of nuisance or hazardous dust. The DWS
provides effective dust control and allows complete
freedom of movement.
Composite Grinding
The DWS gives the worker complete freedom of
movement while grinding or moving around large or odd-
shaped parts. Open-pleat Fibra-Web or Ultra-Tek
®
filters
are required for the fibrous nature of composite dust.
An open louver inlet is also required for improved dust
capture. Recommended options include acoustic panels
for a quiet work environment, control panel for reduced
installation expense, flush lights for increased headroom,
and HEPA afterfilters for added confidence on composite
dust.
Содержание DWS 4-1
Страница 11: ...Downflo Workstation DWS 4 1 to 6 4 8 This Page Intentionally Left Blank ...
Страница 20: ...17 Donaldson Company Inc Solenoid Enclosure ...
Страница 42: ...39 Donaldson Company Inc Service Notes Date Service Performed Notes ...
Страница 43: ......