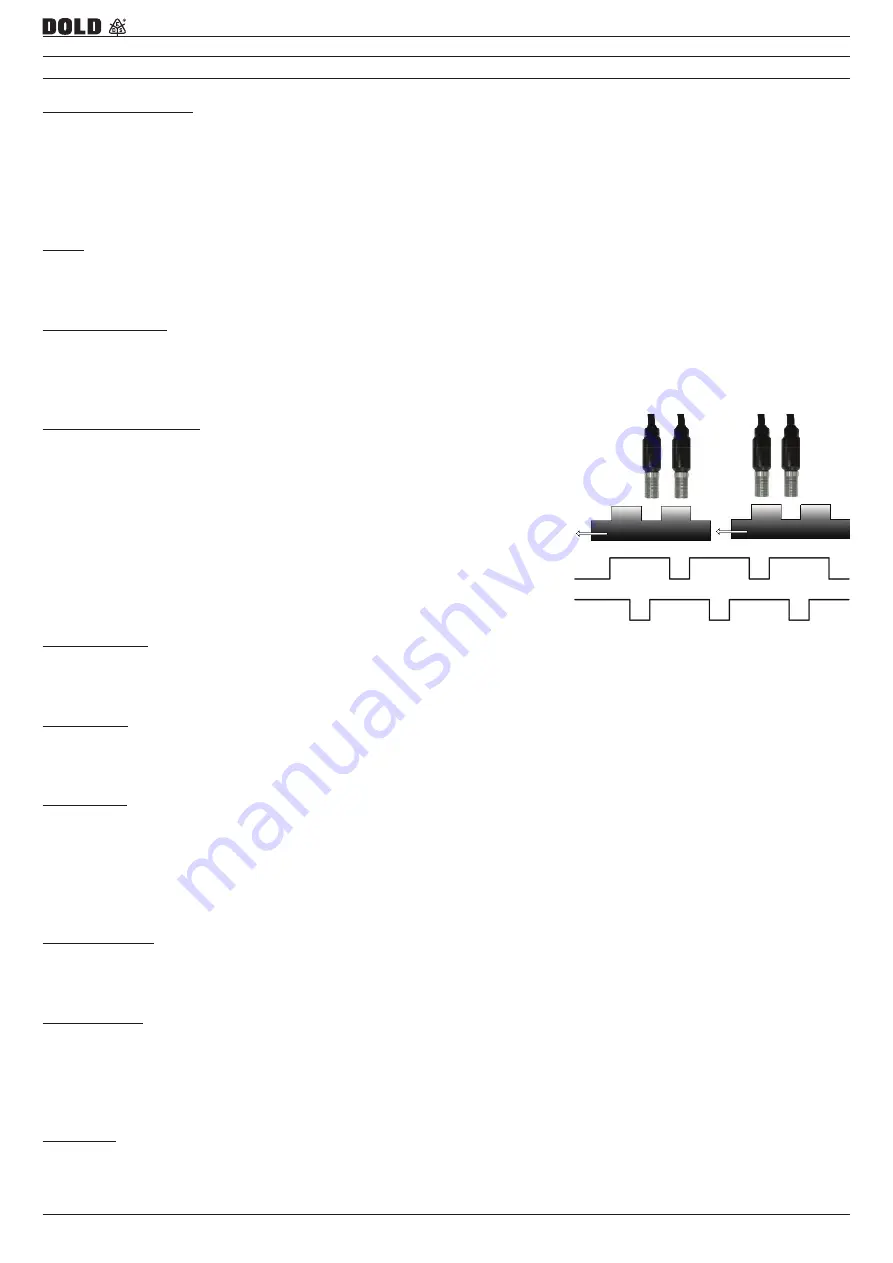
Configurable Safety System SAFEMASTER PRO
126
0265525 / 16.05.19 en / 101A
Threshold number:
It allows you to enter the number of thresholds for the maximum value of speed. Changing this value will
increase/ decrease the number of thresholds that can be entered from a minimum of 1 to a maximum of 8 with
UG 6911.10 (FW
≥
4.0 and UG 6917 FW
≥
2.0) and 4 with UG 6911.10 (FW < 4.0) or UG 6911.12/080 or UG 6917
(FW < 2.0). In the case of thresholds greater than 1, the input pins for the selection of the specific threshold will
appear in the lower part of the function block.
Pitch:
If the Axis Type chosen was linear, this field allows you to enter the sensor pitch to obtain a conversion between
sensor revolutions and distance travelled.
Proximity choice:
It allows you to choose the type of proximity sensor from PNP, NPN, Normally Open (NO) and Normally Closed
(NC), with 3 or 4 wires.
(In order to ensure a Performance Level = PLe use a proximity switch type PNP, NO)
Proximity Interleaved:
When an axis of the UG 6917 module is configured for a
measurement with two proximity switches, these can be
configured in interleaved mode. Under the conditions listed
below the system reaches a Performance Level = PLe
• Proximity switches must be fitted such that
the recorded signals overlap
• Proximity switches must be fitted such that at least one
is always activated
Measurement:
Enter in this field the number of pulses/revolution (in the case of rotary sensor) or µm / pulse (linear sensor)
relating to the sensor used.
Verification:
Enter in this field the number of pulses/revolution (in the case of rotary sensor) or µm/pulse (linear sensor)
relating to the second sensor used.
Gear Ratio:
This parameter is active if there are two sensors on the selected axis. This parameter allows you to enter the
ratio between the two sensors. If both sensors are on the same moving parts, the ratio will be 1 otherwise the
number corresponding to the report must be entered. E.g. there are an encoder and a proximity switch, and the
latter is on a moving part that (due to a gear reduction ratio) rotates at twice the speed of the encoder. Therefore,
this value must be set at 2.
Hysteresis (%):
It represents the percentage hysteresis value below which the speed change is filtered. Enter a value other than
1 to avoid continuous switching as the input changes.
Speed 1 … 8:
Enter in this field the maximum speed value above which the function block output (OVER) will be 0 (FALSE). If
the measured speed is less than the set value, the function block output (OVER) will be 1 (TRUE).
If UG 6911.10 (FW
≥
4.0 and UG 6917 FW
≥
2.0), it’s possible to enter the speed value with the decimal point
(not with UG 6911.12/080).
Frequenz:
It shows the maximum calculated frequency values fM and fm (decreased by the hysteresis set). If the displayed
value is GREEN, the calculation of frequency gave a positive result.
Parameters
Содержание Safemaster Pro
Страница 8: ...Configurable Safety System SAFEMASTER PRO 8 0265525 16 05 19 en 101A...
Страница 198: ...Configurable Safety System SAFEMASTER PRO 198 0265525 16 05 19 en 101A DECLARATION OF CONFORMITY...
Страница 199: ...Configurable Safety System SAFEMASTER PRO 199 0265525 16 05 19 en 101A DECLARATION OF CONFORMITY...