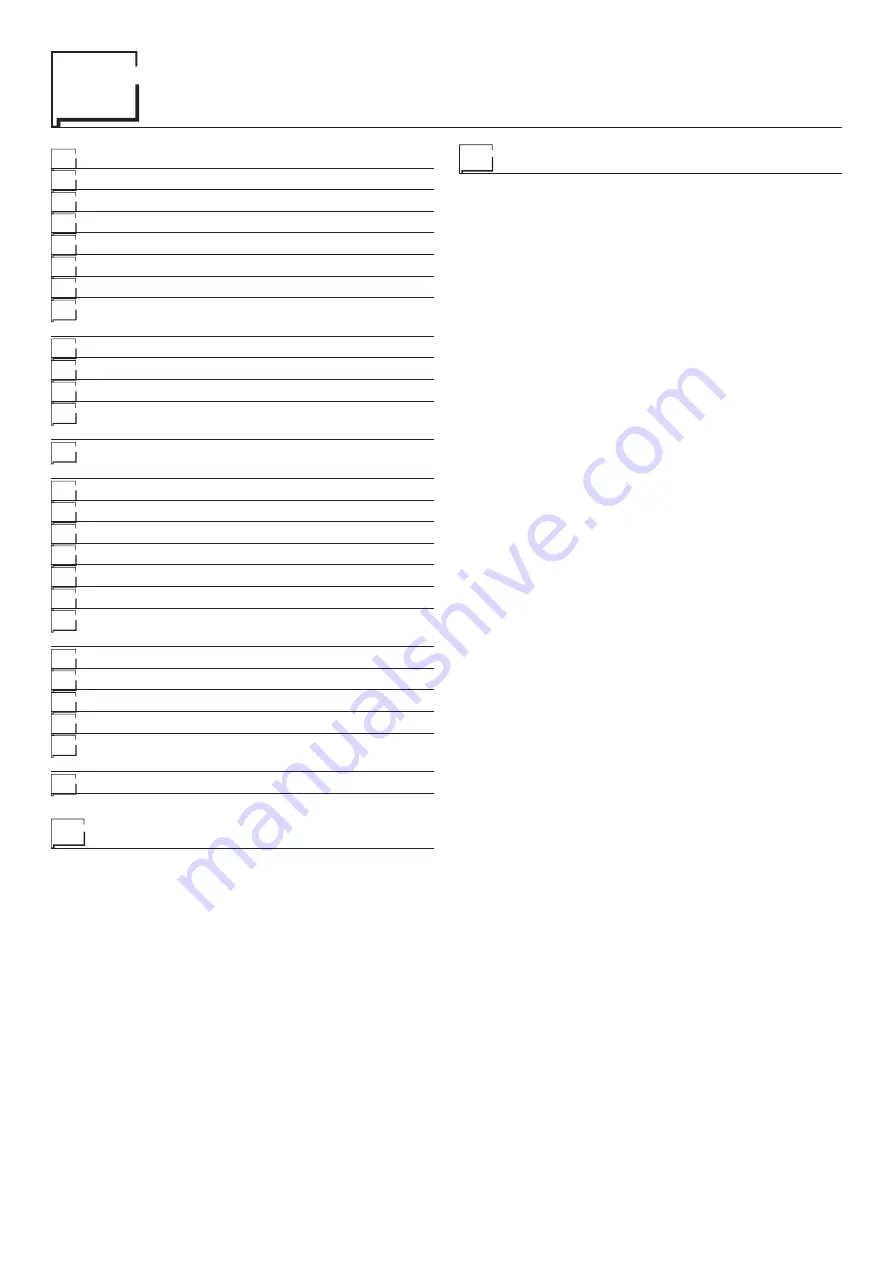
2
How to lift up the welding power source
4
Connecting the welding welding power source to
Command and control units (Fig. A)
MIG-MAG / Puls MIG / DOUBLE Puls MIG
MIG-MAG / Puls MIG / DOUBLE Puls MIG
The pointing out of any difficulties and their
Replacing the digital interface PCB
Electro topographical diagram
12
Electro topographical diagram key
Meaning of graphic symbols on welding power
source 13
Description
MULTI-FUNCTION INVERTER WELDING POWER SOURCE
SUITABLE FOR SINGLE-PHASE POWER SUPPLIES FOR
MIG Puls, MIG DOUBLE Puls, MIG-MAG, MMA, and TIG
WELDING (with “Lift” type ignition)
Multifunction synergic welding power source, based on the
leading-edge IGBT inverter technology and fully digitally con-
trolled, offer premium welding quality in both MIG/MAG and
Pulsd / Dual-Pulsd MIG on all materials, especially stainless
steel, aluminium and galvanized steel; the spatter-free welding
feature minimises reprocessing work. It also ensures excellent
performance in TIG and MMA welding prcesses.
Innovative, versatile, light-weight, easily portable, simple to use,
DIX PI GO 1156.M Puls
is a very high level product that is ab-
solutely irreplaceable technologically for all internal and exter-
nal maintenance works, vehicle bodyworks, agricultural and
small light metalwork jobs.
The principal characteristics of welding units are:
•
Multifunction power source with premium welding quality in
MIG Puls / double Puls, MMA and TIG with “Lift” type igni-
tion welding processes.
•
Standard polarity inversion for welding with the most com-
mon core wires and without gas.
•
Central Euro connection on torch.
•
Innovative practical design.
•
Supporting structure in metal with front panel in special
shockproof material.
•
Protective visor on the control panel.
•
Robust handle integrated into the chassis.
•
Professional 2-roller wire feeder that guarantees precise
feeding of the wire.
•
The double slot rollers can be replaced without using any
tools.
•
A graduated knob for precise adjustment of the wire pressure
that stays unvaried when the arms open and close.
•
Housing for coils of wire with max Ø 200 mm – 5 kg.
•
Possibility of fitting coils of wire up to max Ø 300 mm - 15 kg
thanks to the exclusive “retrofit kit adaptor” optional extra.
•
Synergic digital control of all welding parameters, shown on
the display, also featuring the following functions:
- Allows less expert operators to regulate all welding param-
eters, choosing the type of program on the basis of the ma-
terial, wire diameter, and gas used.
- Innovative software “DIX ARC” for controlling all welding
parameters.
- Digital Voltmeter / Ammeter with HOLD function (saving of
latest data on both displays).
- “Energy Saving” function to operate the power source cool-
ing fan only when necessary.
- Auto-diagnostic feature for trouble shooting.
- Ability to store personalized welding programmes (JOB).
- MIG-MAG welding:
- BURN BACK control. At the end of each weld, in any
condition and with any material, the digital control en-
sures a perfect wire cut, prevents the typical “wire glob-
ule” from forming and ensures correct arc restriking.
- WSC Wire start control. This arc striking control device
prevents wire from sticking to the workpiece or torch
nozzle and ensures precise and smooth arc striking,
particularly when welding aluminium.
- Welding parameters that are controlled digitally by a
microprocessor, are monitored and modified in just a
few seconds, maintaining a consistently precise and
stable arc as the welding conditions continue to vary
due to the movement of the torch and the irregularities
of the parts to be welded.
Introduction
Thank you for buying our product.
In order to get the best performance out of the equipment and
ensure the maximum lifespan of its parts, the use and mainte-
nance instructions contained in this manual must be read and
strictly complied with, as well as
the safety instructions con-
tained in the relevant folder
. If repairs to the equipment are
required, we recommend that our clients contact our service
centre workshops, as they have the necessary equipment and
personnel that are specifically trained and constantly updated.
All our welding power sources and equipment are constantly
developed and so changes may be made in terms of their con-
struction and features.
Copyright © 2018 DINSE G.m.b.H., Hamburg.
These instructions or excerpts there of shall not be duplicated, translated or reproduced, nor shall
they be stored, processed, transmitted or distributed by any electronic means without the prior
written permission of
DINSE G.m.b.H.
D I N S E G . m . b . H .
Tarpen 36 • D-22419 Hamburg
Tel. +49 (0)40 658 75-0
Fax +49 (0)40 658 75-200
[email protected] – www.dinse.eu
Содержание DIX GO 1156.M Puls
Страница 12: ...12 2101AC55 A Electro topographical diagram...