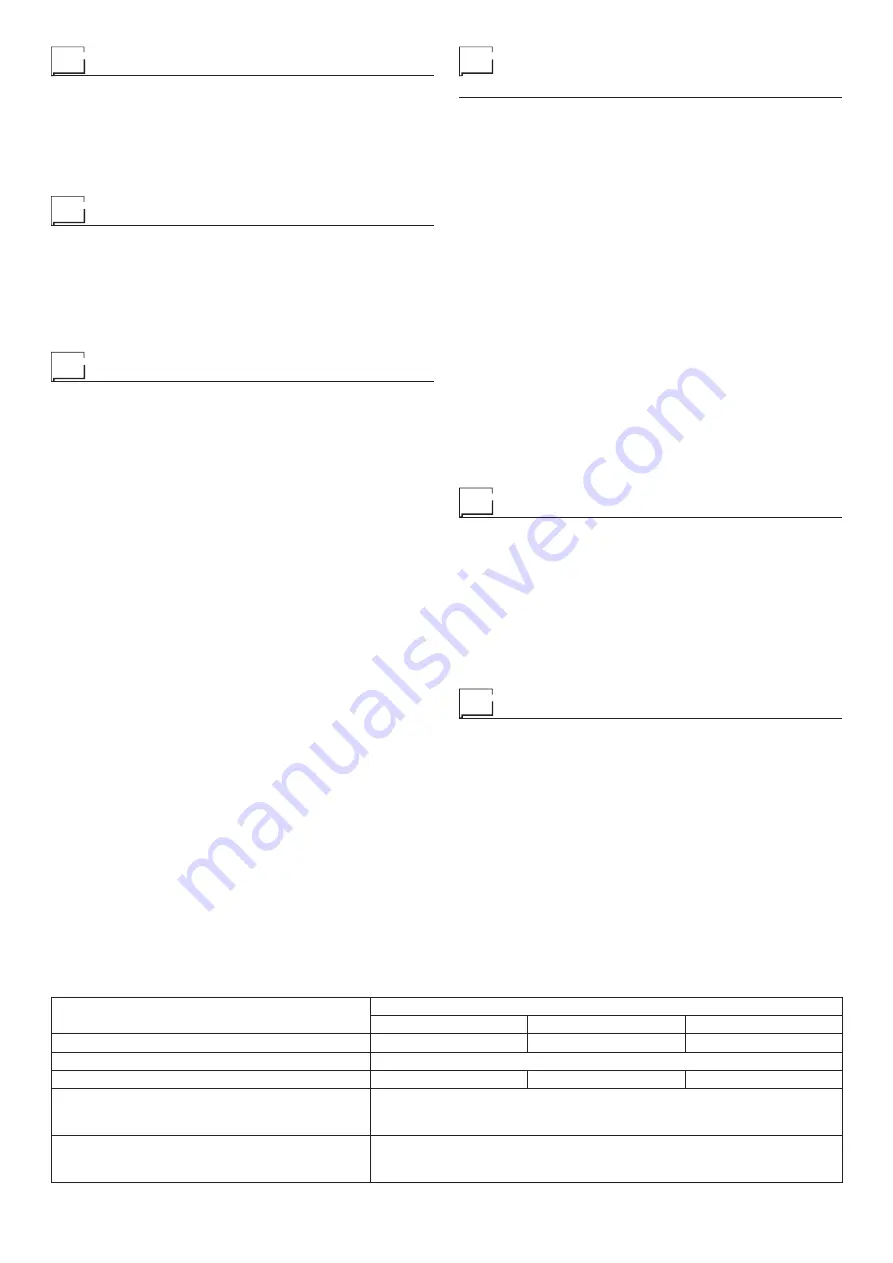
4
How to lift up the welding power source
The welding power source has a strong handle all in one with
the frame, used for transporting the welding power source man-
ually only.
NOTE: These hoisting and transportation devices conform to
European standards. Do not use other hoisting and transpor-
tation systems.
Open the packaging
Upon receiving the welding power source:
•
Remove the welding power source and all relevant accesso-
ries-components from their packaging.
•
Check that the welding power source is in good condition, if
not report any problems immediately to the seller-distributor.
•
Make sure all ventilation grilles are open and that no foreign
bodies are blocking the air circulation.
Installation and connections
The installation site for the system must be carefully chosen
in order to ensure its satisfactory and safe use. The user is re-
sponsible for the installation and use of the system in accord-
ance with the producer’s instructions contained in this manual.
Before installing the system the user must take into consider-
ation the potential electromagnetic problems in the work area.
In particular, we suggest that you should avoid installing the
system close to:
•
Signalling, control and telephone cables.
•
Radio and television transmitters and receivers.
•
Computers and control and measurement instruments.
•
Security and protection instruments.
Persons fitted with pace-makers, hearing aids and similar
equipment must consult their doctor before going near a weld-
ing power source in operation. The equipment’s installation
environment must comply to the protection level of the frame
i.e. IP 23 S (IEC 60529 publication). The system is capable of
working in environments where working conditions are partic-
ularly hard.
This system is cooled by means of the forced circulation of air,
and must therefore be placed in such a way that the air may
be easily sucked in and expelled through the apertures made
in the frame.
The equipment must be assembled as follows:
•
Mount on the trolley (optional extra).
•
Fix the welding unit to the trolley.
•
Connect the welding welding power source to the utility line.
•
Connect up the welding cables.
Connecting the welding welding
power source to the utility line
Connection of the welding power source to the user line
(electrical current) must be performed by qualified per-
sonnel.
Before connecting the welding welding power source to
the mains power supply, make sure that rated voltage and
frequency correspond to those provided by the mains pow-
er supply and that the welding welding power source’s
power switch is turned to “O”.
Connection to the power supply must be carried out using the
tripolar cable supplied with the system, of which:
•
2 conducting wires are needed for connecting the welding
power source to the supply.
•
The third, which is YELLOW GREEN in colour is used for
making the “GROUND” connection.
Connect a suitable load of normalised plug (2p + e) to the
power cable and provide for an electrical socket complete
with fuses or an automatic switch. The ground terminal
must be connected to the ground conducting wire (YEL-
LOW-GREEN) of the supply.
Table 2 shows the capacity values that are recommended for
fuses in the line with delays.
NOTE: Any extensions to the power cable must be of a suita-
ble diameter, and absolutely not of a smaller diameter than the
special cable supplied with the welding power source.
Command and control units (Fig. A)
Pos. 1
Control panel.
Pos. 2
Fast coupling straight polarity.
Pos. 3
Fast coupling reverse polarity.
Pos. 4
Centralised MIG-MAG torch connection.
Pos. 5
Power supply switch. In the “O” position the welder
is off.
Pos. 6
Mains cable.
Pos. 7
Weld gas inlet coupling.
Pos. 8
Cable clamp for the welding cable to pass (with the
“Retrofit kit adaptor” fitted).
Loading wire
•
Open the side panel on the left using the relevant Allen key
and insert the coil (use coils with a MAX diameter of 200 mm
and MAX weight of 5 kg) that suits the material to be welded
on the relevant support so that the wire unwinds anticlock-
wise and aligning the protruding marker on the support with
the relevant hole in the coil.
Table 2
Model
DIX PI GO 1156.M Puls
MIG/MAG
TIG
MMA
Power input (I
2
Max)
kVA
9,7
6,4
7,8
Delayed fuse (I
eff)
A
16
Duty cycle @ X% (40°C)
A
200 (15%)
175 (20%)
150 (25%)
Mains cable
Length
Section
m
mm
2
3
2,5
Ground cable
Length
Section
m
mm
2
3
16
Содержание DIX GO 1156.M Puls
Страница 12: ...12 2101AC55 A Electro topographical diagram...