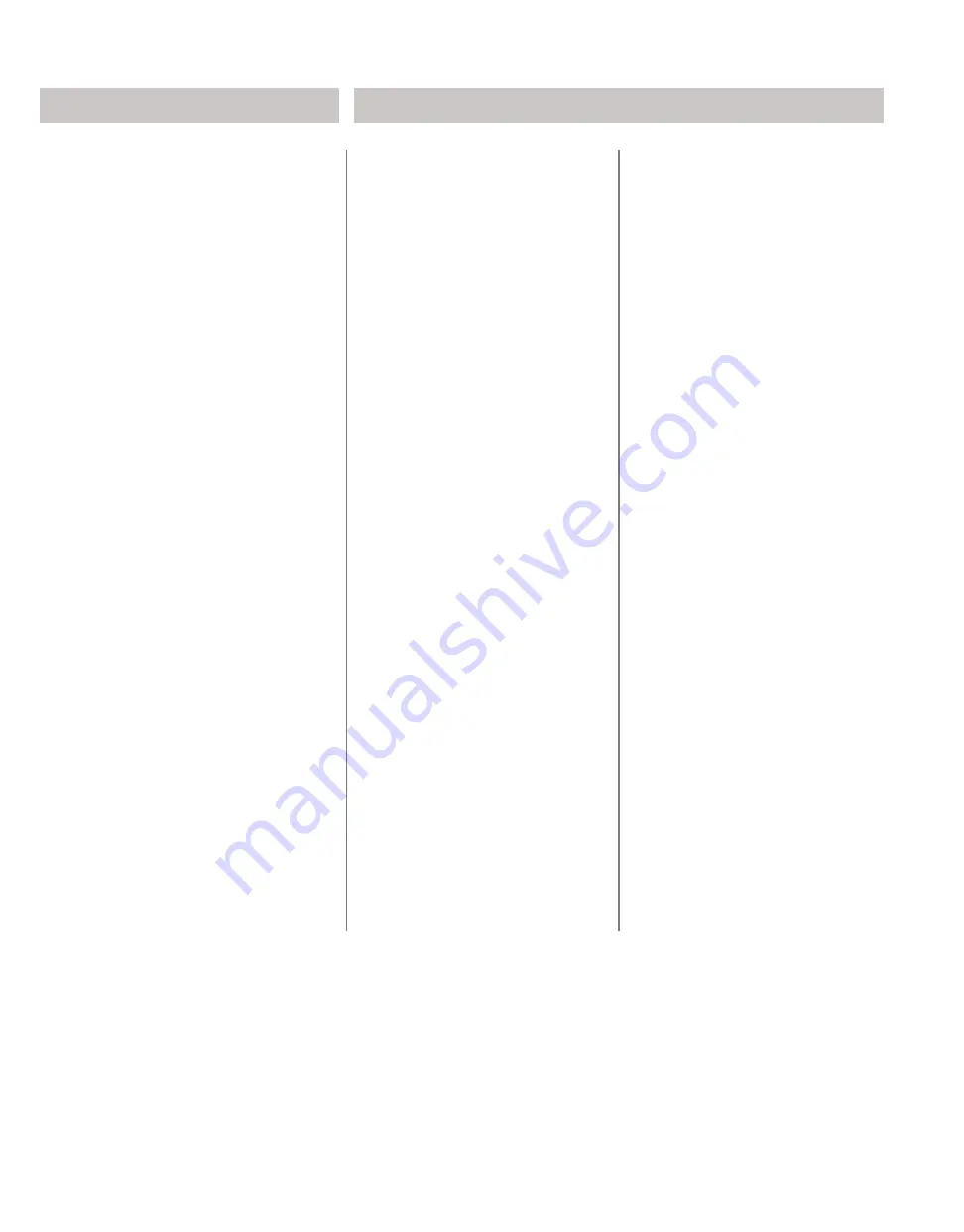
a. Remove static mixing tip.
b. Grease the fi ttings on the manifold and-
secure for next use.
c. Fill Iso side tank (Part B for Metzger/
McGuire joint fi llers, amber colored side)
with Iso product to within a couple inches
of the top of the tank.
d. Press a new clean plastic bag, or similar
plastic sheeting, over tank and into top
of product lapping excess plastic over
the top sides of the tank. By doing this,
excess air potentially containing moisture
or humidity is forced away from the top of
the polyurea Iso component.
e. Place tank lid over plastic sheeting and
secure.
f. At next use, a thorough evaluation must
be done as indicated in the “Prior to Use”
section to ensure no cross contamination
exists in the manifold.
Next Day Use:
1. It is always advisable to re-check the
manifold fi rst by removing the check ball
assembly and inspecting for clogs and
also re-checking ratio by dispensing a
small amount of material into graduated
plastic containers.
2. Before use, cure test should be per-
formed by dispensing through the static
mixer onto a cardboard or plastic sheet
and monitored for 10-15 minutes to con-
fi rm cure prior to commencement of fi ller
placement.
3. Follow instructions outlined above under
“Prior to Use” and “Dispensing Filler”.
End of Project:
1. Dispense all remaining polyurea into
waste container.
2. Once polyurea has been dispensed,
partially fi ll each tank with hydraulic fl uid
and run through the machine to ensure
pumps and lines have been purged.
3. Grease fi ttings on the manifold.
4. Wrap mixing manifold with plastic or
shrink wrap tightly sealing end and pre-
venting moisture exposure and absorp-
tion into manifold.
5. Package up for storage.
Problems During Dispensing
Polyurea Joint Filler:
1. Material fl owing slowly:
A. May occur when material temperature
is cool and in the case of cooler/freezer
environments. Preheat material and/
or store outside of cooler/freezer area.
For freezer installations, tank heaters
should be used to maintain a “pump-
able” viscosity.
B. May occur if static mixing manifold has
buildup or restriction in the outlet orifi ce.
Remove pump lines from the manifold,
remove fi ttings,
plastic washer, check ball, and spring
and ensure no buildup or restriction is
present. Inspect outlet orifi ce for restric-
tion and drill out if buildup is present.
C. May occur if mixed material begins to
“gel” inside of the static mixing element
(tip). This typically will occur when
jumping from joint to joint allowing
mixed product to set inside the plastic
mixer without purging. Purging the
static mixing element should be done
approximately every 45 seconds with
most M/M products.
2. Material STOPS fl owing:
A. Check main power supply to ensure
voltage is entering the speed con-
trol unit. Inside the control box cover
located on the face of the circuit board
a GREEN LED light should be illumi-
nated when proper voltage is present. If
indicator light is off (switch is on), check
main power supply cord to ensure
power is being supplied to the control
box. Correct if necessary. If control box
is receiving power and the light on the
front is OFF, check 12A ceramic fuse
behind the control box cover (left side of
electrical panel). Replace if necessary.
B. If control box is receiving power and the
LED light on the circuit board is ON,
check 8A MDL (slow burn) fuse behind
the control box cover (right side of
electrical panel). DISCONNECT POW-
ER before removing or testing fuses!
Replace if necessary. Burnt 8A MDL
fuses will be the primary cause for NO
FLOW situations and will typically occur
when the motor is being placed under
excess strain. Most common to occur
when dispensing in cold environments
or freezer/cooler installations.
C. If control box fuses are not “blown”,
check trigger switch mechanism on dis-
pensing wand. A trigger switch malfunc-
tion is not common, but does occur from
time to time. In this instance, the green
LED light will be illuminated indicating
the circuit board is receiving power.
3. Material does not cure or cures “soft”:
A. Always test cure of previously placed
materials as you move from section to
section. Most M/M polyurea products,
even in freezer environments, should
reach signifi cant cure within 1 hour.
B. ALWAYS confi rm that the proper pump
pulleys or sprockets are being used.
Equal sized pulleys/sprockets for 1:1
ratio.
C. If uncured or soft cure is found, an off
ratio mixture is most always caused
by a restriction or buildup inside of
the mixing manifold. Disconnect lines,
inspect and clean mixing manifold. Prior
to reassembly, test material fl ow and
ratio check directly from the pump lines.
After confi rming proper ratio from the
lines, connect mixing manifold, attach
static mixing element and dispense test
material to monitor for full cure.
D. If OFF ratio dispensing is found when
testing directly from the pump lines
(without the manifold attached), check
each hose line for contamination or
restriction. Ultimately, it will be VERY
diffi cult to visually fi nd a restriction
inside the hose line. Generally, hose
lines should be replaced before starting
a project.
E. If hose lines are clear, buildup or re-
striction will likely be within one or both
pump units. Disassemble, clean thor-
oughly, and reassemble. Attach hose
lines and test fl ow ratio.
TROUBLESHOOTING
SET-UP (cont.)
Содержание DP-PUMP10GAL
Страница 4: ...www diamaprosystems com 404 834 1162 ...