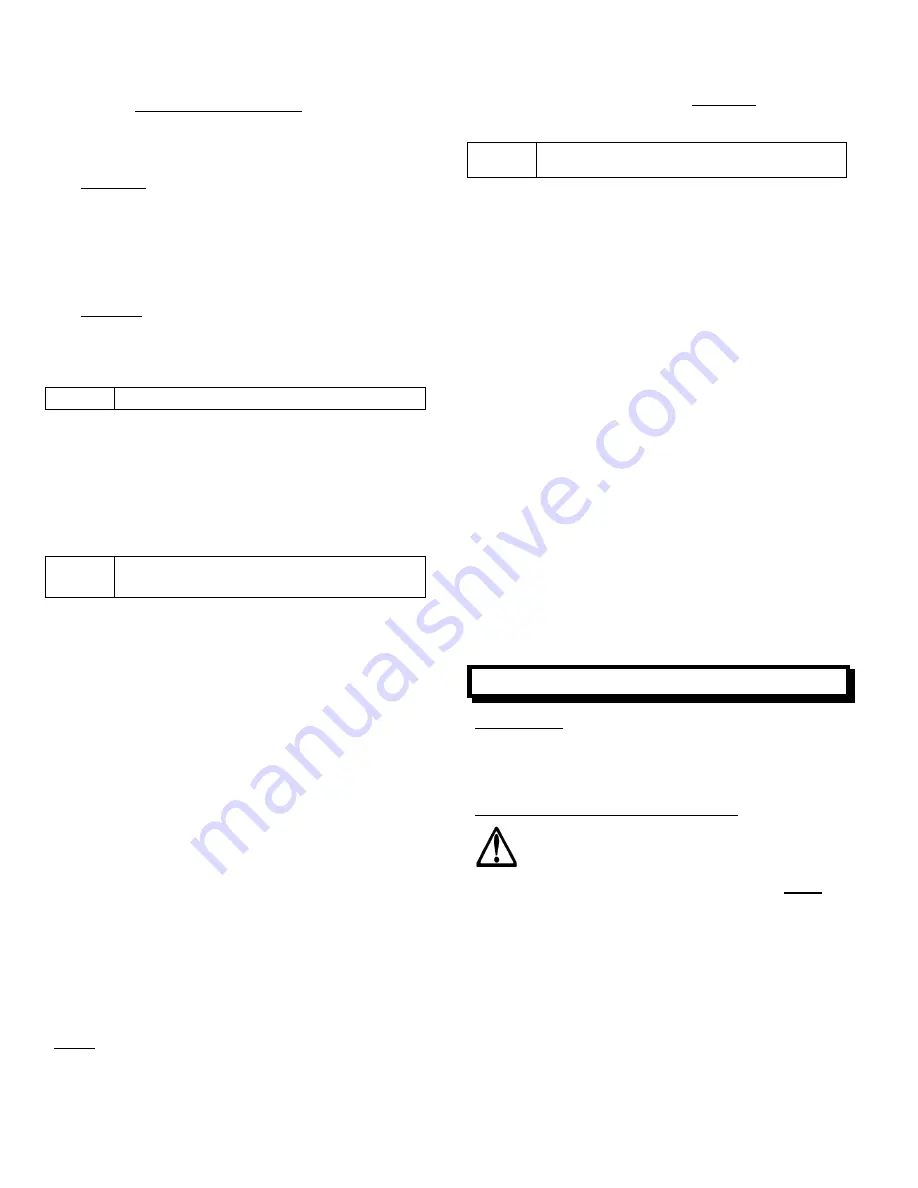
22
the life, near the same cost as a star
wheel.
c) Tungsten Carbide Wheel: Heavy Duty
asphalt or concrete scarifying, or de-
scaling of steel decks. 10 times the life of
a star wheel.
Assembly: When new cutters are installed, be
sure to “stagger” the washers in order in avoid any
“blind spots” in the cutter path (On any one cutter
block put the first washer on the opposite end of
each stack of cutters). Also make sure that the
wheels can rotate freely when the attaching
Capscrews are tightened.
Bushings: Be sure to inspect the cutter bushings
on a regular basis. Worn bushing can cause the
Scarifier Wheels to break and be thrown against
the inside of the machine frame.
4.5
Wire Brushes
[See FIG. 26]
For Light Scarifying and cleaning. Flat wires are
available in many sizes and configurations. They
should be rotated end-for-end in the
Accessory Disk
[P]
every hour to avoid the wire taking a “set” (wire will
bend in one direction). External weight added to
machine will NOT normally increase production rates,
but only accelerate the wire brush wear rates
.
4.6
Multi-Segmented Diamond Disks [Q]
[See FIG. 24 & FIG. 25]
a) Temporary removal of the
Front Shield (A)
may be
required to complete this installation.
b) Attach the
Multi-Segmented Diamond Disks (Q)
to
the
Adapter Plate (R)
using the four (4)
Flat Head
Screws (S1)
and
Thin Locknuts (S2)
provided in
the
Adapter Plate Kit (Kit Part Number 177861)
.
Tighten the
Screws (S1)
securely. Repeat this
procedure for the other
Adapter Plate (R)
.
c) Attach the
Diamond Disk / Adapter Plate Assembly
to the machine using the three (3)
Capscrews
(T1)
,
Lockwashers (T2)
, and
Washers (T3)
provided in the Adapter Plate Kit. Tighten the
Capscrews (T1)
securely. Repeat this procedure
for the other assembly.
d) Gently lower the front of the machine until the
tools touch the ground.
e) Pivot the axle so that it is in the
Operation Position
[F] [See FIG. 11].
f) Lower the
Front Shield [A]
from its upper position.
Loosen the three (3) capscrews and lower the
shield so that it is only 3/8-1/2” (10-12 mm) from
the ground.
Notes
: If machine starts to vibrate and shake try
removing external weight from the machine. If the
vibration continues, move the axle into the “E2”
position [See FIG. 11]. This position is normally a
“transport” position, but for the diamond disks it
removes most of the weight from the front of the
machine and allows the disks to glide over the surface
rather than dig into the surface.
4.7
Tool Holding Pad (HH) Installation
[See FIG. 19, FIG. 20, FIG. 21, FIG. 22, FIG. 23]
This machine will allow the use of Scrubbing Pads [JJ]
that are available from another manufacture.
a) Position the triangular area of the
Tool Holding
Pad [HH]
[See FIG. 21] so that it mates with
the triangular area on the
Accessory Disk [P]
.
b) Use the 1/2-20UNF x 1-1/4” Long Capscrew
[SS1] and Lockwasher [SS2] to attach the Tool
Holding Pad to the Accessory Disk. Tighten
the capscrew securely, using the ¾” (19 mm)
End of the Wrench [V] [Shown in FIG.8].
c) Repeat this procedure on the other
Accessory
Disk [P]
.
d) Install the Scrubbing Pads [JJ], two (2) per
machine. Gently press the tool onto the hook
and loop fastening system until it is secure.
e) Gently lower the front of the machine until the
tools touch the ground.
f) Pivot the axle so that it is in the
Operation
Position
[F] [See FIG. 11].
g) Lower the
Front Shield [A]
from its upper
position. Loosen the three (3) capscrews [See
FIG. 2 & FIG. 3] and lower the shield so that it
is only 3/8-1/2” (10-12 mm) from the ground,
then re-tighten the three (3) capscrews.
5. Operating Instructions
All Models:
q
Configure the unit with the proper tool for the job.
See Section 4 of this document for tool
installation.
Start / Stop of Electric Models:
WARNING:
Make sure the
Voltage Change
Switch (J)
[See FIG. 5], is set to either 115, or
230 Volt, to match the voltage supply. The
Voltage Change Switch (J)
position is never to
be changed while the motor is running.
Make sure that the
Voltage Change Lock Bolt
(TT)
is in position. It will prevent the Voltage
Change Switch from being accidentally moved
into the wrong position.
Local electrical codes may require changing
the Plug (LL) [See FIG. 1] on the motor to the
proper NEMA connector to match the voltage
supply.
Содержание F60000
Страница 7: ...7...
Страница 8: ...8...
Страница 9: ...9...
Страница 10: ...10...
Страница 28: ...28 Diagram 1 Final Assembly Group 1 5 hp Electric...
Страница 30: ...30 Diagram 2 Final Assembly Group 11 hp Honda Gas...
Страница 32: ...32 Diagram 3 Handle Group 1 5 hp Electric...
Страница 36: ...36 Diagram 5 Motor Group 1 5 hp Electric...
Страница 38: ...38 Diagram 6 Engine Group 11 hp Honda...
Страница 40: ...40 Diagram 7 Gearbox Assembly All Models...
Страница 42: ...42 Diagram 8 Water Tank Kit Optional P N 177855 Complete Kit...
Страница 50: ...50 Diagram 15 Wiring Diagram 1 5hp Electric Model...