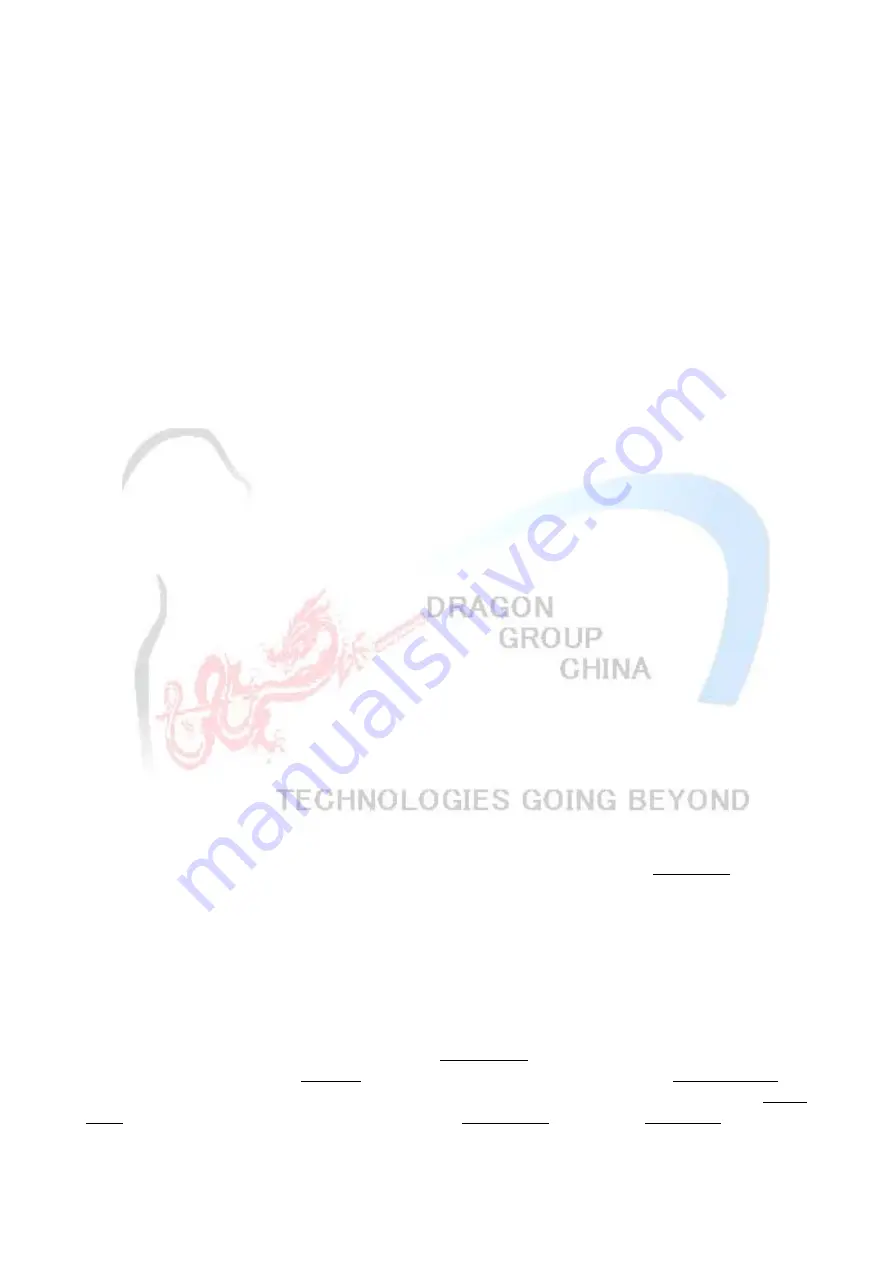
point is that the welding spots can still be welded on the pad. The ideal situation is
no poor welding. Poor welding may be caused by pollution or the uneven
distribution of flux paste. What's more, warped PCB may also lead to poor welding.
Open-circuit welding spot may exist, too.
The quantity and size of poor welding are the key factors to decide whether it
will be accepted. Generally the size of single poor welding should be less than 50%
of the solder ball's diameter. If the ball is surrounded by reflow solder, BGA is able
to work. It is a very critical standard. The electrical properties may meet the
requirements but the mechanical strength will be affected.
PCB with BGA must use X-ray evaluation systems that can decern holes of less
than 100 µm diameter. The X-ray must be able to observe from top-down and tilt.
X-rays is a reliable guarantee of successful BGA welding,
b. Proposed inspection criteria
The inspection criteria will help X-ray inspection system confirm some typical
welding problems, which is related with the use of BGA device. It includes the
following factors:
(1)Poor welding
Poor welding results from the expansion of compounds in solder during the
heating of BGA. BGA with poor welding may cause some problems such as
ineffectiveness. The inspection criterias are as follows: the size of single poor
welding should be no more than 20% of the solder ball's diameter, with no single
poor welding on the surface; if many poor welding may exist, the total should be no
more than 20% of the solder ball's diameter.
(2)Desoldering spots
No desoldering spots.
(3)Bridging and short-circuit.
When there is extra solder or the solder is not put on the right place, bridging
and short-circuit may happen. So no bridging or short-circuit.
(4)None paraposition.
The X-ray image will show very clearly whether the BGA solder ball is aimed
at the welding pad on PCB.
(5)Broken circuit and cold welding
When solder don't touch the relevant pad or the solder doesn’t flow very well, there
will be broken circuit or cold welding. It is absolutely not allowed.
4. BGA rework process
Most of the semiconductor device’s heat-resistant temperatures are between
240°C and 600 °C. Therefore, the control of the temperature and uniformity are very
important to BGA rework systems. BGA rework process as follows:
a. Printed Circuit Board and BGA preheating
Printed Circuit Board and BGA’s preheating is meant to wipe off the moisture. If
the moisture was little, this step can be omitted.
b. Remove BGA
If the BGA will not be reused, and the PCB can endure high temperature, we can
use high temperature (shorter heating period) to remove it.
c. Clean the pad.
Pad cleaning is mainly clearing the solder paste and scaling powder remained on the
surface of PCB after BGA removal. For that process, it must use standard cleaning agent. To
ensure the reliability of the BGA solders, generally we cannot use the remained solder
paste in the pad, and we must clear away the used solder paste, except that solder balls reform on
the BGA. Because of the small size of BGA, especially CSP (or µBGA smaller), it is always
difficult to cleaning the pad, so when reworking CSP, it needs to use Rinse-free Flux if
5
Содержание ZM-DGC900
Страница 26: ...26...