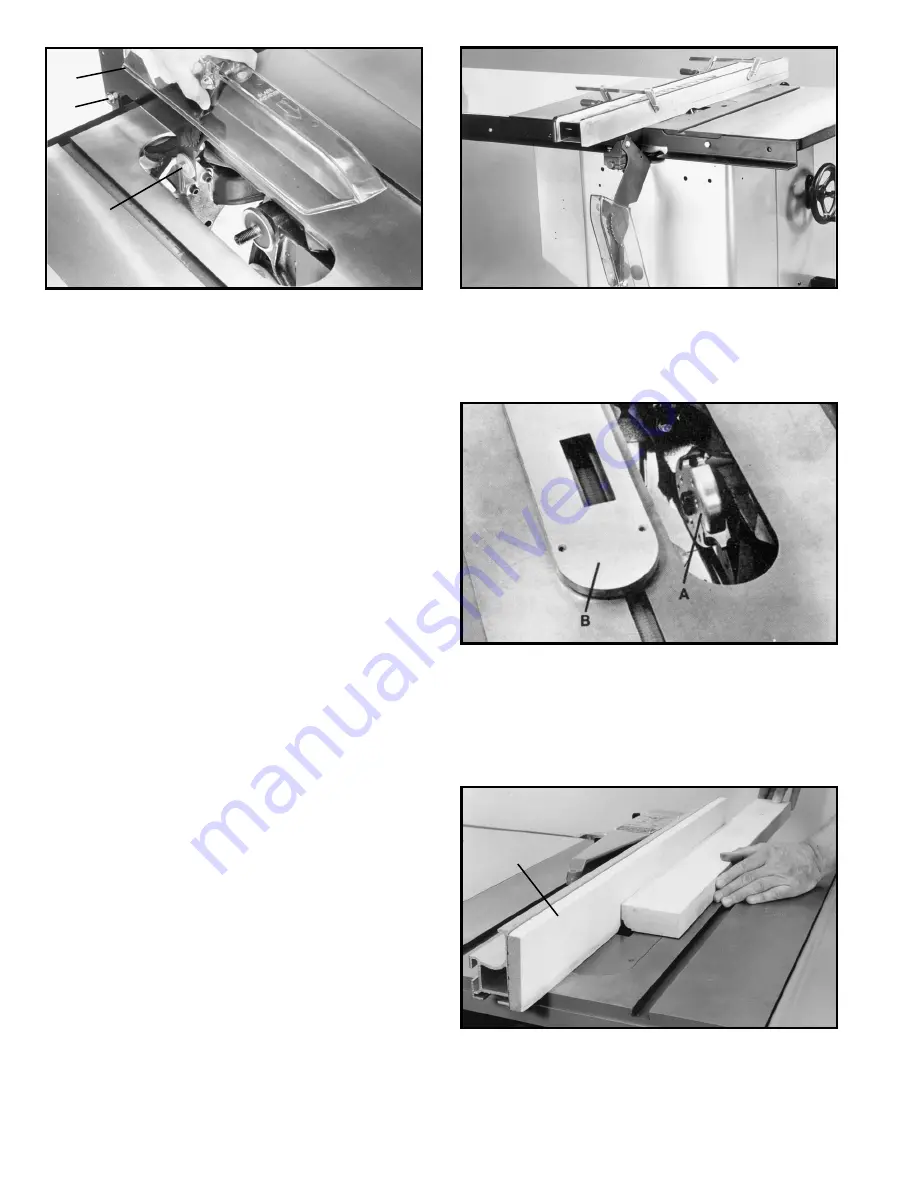
24
different knife shapes available make it possible for the
operator to produce almost any kind of mouldings, such as
various styles of corner moulds, picture frames, table
edges, etc.
The moulding head consists of a cutterhead in which can
be mounted various shapes of steel knives, as shown in
Fig. 83. Each of the three knives in a set is fitted into a
groove in the cutterhead and securely clamped with a
screw.
The knife grooves should be kept free of sawdust,
which would prevent the cutter from seating properly.
IMPORTA N T: For certain cutting operations such as
dadoing and moulding where you are not cutting
completely through the workpiece, the blade guard and
splitter assembly cannot be used. Loosen screws (G) and
(H) Fig. 84. Lift up and swing blade guard and splitter
assembly (W) Fig. 84, to the rear of the saw as shown in
Fig. 85. CAUTION: Always return and fasten the blade
guard and splitter assembly to its proper operating
position for normal thru-sawing operations.
The moulding cutterhead (A) Fig. 86, is assembled to the
saw arbor as shown. Also, the accessory moulding
cutterhead table insert (B), must be used in place of the
s
tandard table insert.
It is necessary when using the moulding cutterhead to add
wood-facing (C) to the face of the rip fence, as shown in
Fig. 87. The wood-facing is attached to the fence with two
clamps, as shown in Fig. 85. When attaching wood facing
to a fence,
3
/
4
inch stock is usually suitable for most work,
although an occasional job may require 1 inch facing.
Position the wood-facing over the cutterhead with the
cutterhead below the surface of the table. Turn the saw on
and raise the cutterhead. The cutterhead will cut its own
groove in the wood-facing. Fig. 87, shows a typical
moulding operation. NEVER USE MOULDING CUTTER-
HEAD IN A BEVEL POSITION.
IMPORTA N T: NEVER RUN THE STO C K
BETWEEN THE FENCE AND THE MOULDING
CUTTERHEAD AS IRREGULAR SHAPED
Fig. 84
Fig. 85
Fig. 86
Fig. 87
W
G
H
C