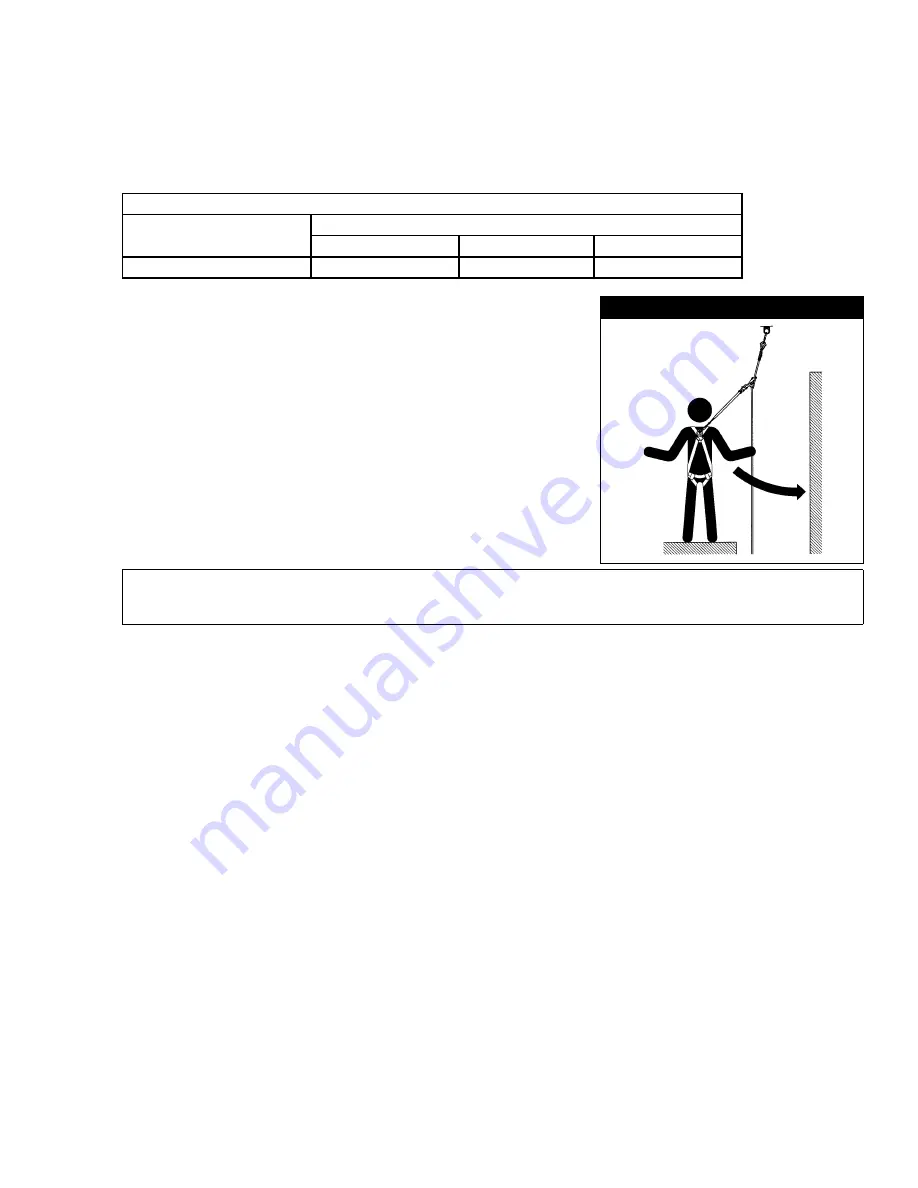
5
2.5 FALL
CLEARANCE:
Ensure suf
fi
cient clearance exists in your fall path to prevent striking an object during
a fall. The clearance required is dependent upon the subsystem (rope grab and lanyard, rope grab and
carabiner) and lifeline properties. Table 1 shows the approximate elongation for new DBI/SALA lifelines in
dry conditions. The elongation speci
fi
ed is for an applied static load of 1,800 lbs (8 kN). Lifeline elongation
must be considered when estimating fall clearance. Factors that affect fall clearance include:
•
Elevation of anchorage
•
Free fall distance
•
Worker height
•
Connecting subsystem length
•
Lifeline elongation. See Table 1:
•
Deceleration distance
•
Movement of harness attachment element
Table 1 - Life Line Elongation: ft (m)
Lifeline Type
Lifeline Lenght: ft (m)
25 (8) - 75 (23)
100 (30)
150 (46)
3/8” Wire Rope
—
0.43 (0.13)
0.65 (0.2)
2.6 SWING
FALLS:
Swing Falls occur when the anchorage point is
not directly above the point where a fall occurs (see Figure 4).
The force of striking an object in a swing fall may cause serious
injury or death. Minimize swing falls by working as close to the
anchorage point as possible. Do not permit a swing fall if injury
could occur. Swing falls will signi
fi
cantly increase the clearance
required when a SRL (self-retracting lifeline) or other variable
length connecting subsystem is used.
2.7 ENVIRONMENTAL
HAZARDS:
Use of this equipment in areas
with environmental hazards may require additional precautions
to prevent injury to the user or damage to the equipment.
Hazards may include, but are not limited to; heat, chemicals,
corrosive environments, high voltage power lines, gases, moving
machinery, and sharp edges.
Figure 4 – Swing Falls
Swing Fall Hazard
WARNING:
When working with tools, materials, or in high temperature environments, ensure that
associated fall protection equipment can withstand high temperatures, or provide protection for those
items.
2.8 COMPATIBILITY OF COMPONENTS:
Capital Safety equipment is designed for use with Capital Safety
approved components and subsystems only. Substitutions or replacements made with non-approved
components or subsystems may jeopardize compatibility of equipment and may effect the safety and
reliability of the complete system.
2.9 COMPATIBILITY OF CONNECTORS:
Connectors are considered to be compatible with connecting
elements when they have been designed to work together in such a way that their sizes and shapes do not
cause their gate mechanisms to inadvertently open regardless of how they become oriented. Contact Capital
Safety if you have any questions about compatibility.
Connectors (hooks, carabiners, and D-rings) must be capable of supporting at least 5,000 lbs (22.2 kN).
Connectors must be compatible with the anchorage or other system components. Do not use equipment
that is not compatible. Non-compatible connectors may unintentionally disengage (see Figure 5). Connectors
must be compatible in size, shape, and strength. If the connecting element to which a snap hook (shown) or
carabiner attaches is undersized or irregular in shape, a situation could occur where the connecting element
applies a force to the gate of the snap hook or carabiner. This force may cause the gate (of either a self-
locking or a non-locking snap hook) to open, allowing the snap hook or carabiner to disengage from the
connecting point. Self- locking snap hooks and carabiners are required.
Содержание LAD-SAF 5000338
Страница 2: ...2 ...
Страница 10: ...10 8 0 LABELING This Identification Label must be present and completely legible ...