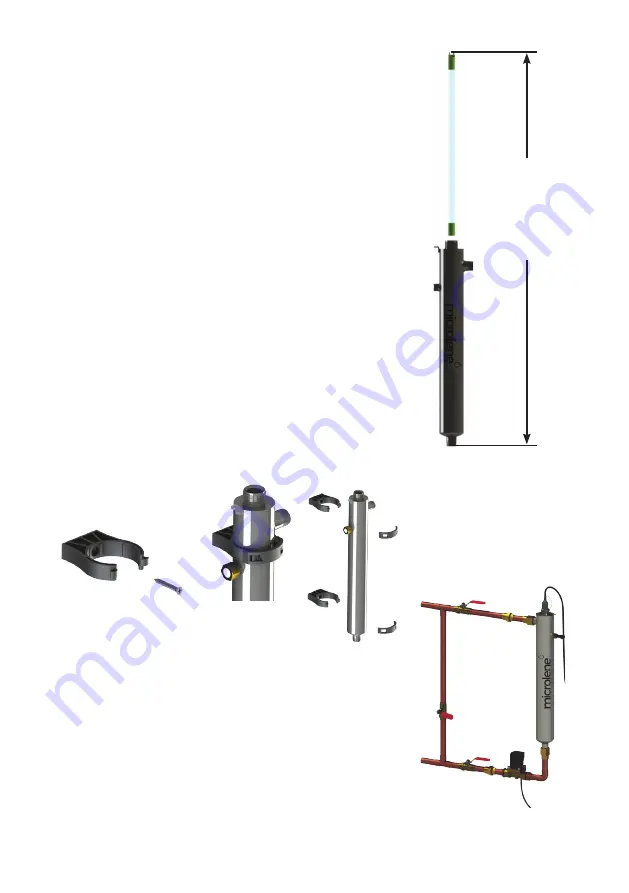
8
Installation
Step 1:
The chamber can be installed either horizontally,
or vertically using the clamps provided. Vertical installation
is the preferred method with the inlet at the bottom (lamp
connection at the top) as it allows any air that may be in the
lines to be easily purged from the system.
If the chamber is being mounted horizontally, it should be
mounted so that water flows out of the threaded outlet upwards.
This ensures the chamber is completely full of water before
existing the chamber, allowing the water maximum exposure
time to the UV light.
Step 2:
The use of a by-pass assembly is recommended as
it will allow you to isolate the UV chamber. This will allow for
easier access in case maintenance is required (See Figure
4).
Step 3:
Fasten chamber clamps to wall with screws
provided. The screws must anchor securely into solid wood,
concrete, or steel structure for adequate strength. Do not
attempt to secure screws into drywall (Figure 3a). Install
Chamber into clamps (Figure 3b).
Step 5:
It is recommended to have a licensed plumber
connect the UV chamber to the water supply and may be a
requirement depending on where you are located.
Figure 3a. Fasten
clamps to wall
Figure
3b. Install
chamber into
champs
Figure 2.Lamp
Removal Spacing
leave at least
an additonal
reactor length
to facilitate
lamp and
sleeve removal
Figure 4. By-pass
assembly
Note: Installation of your
Microlene UV Disinfection
System shall comply with
applicable provincial/state
& local regulations.