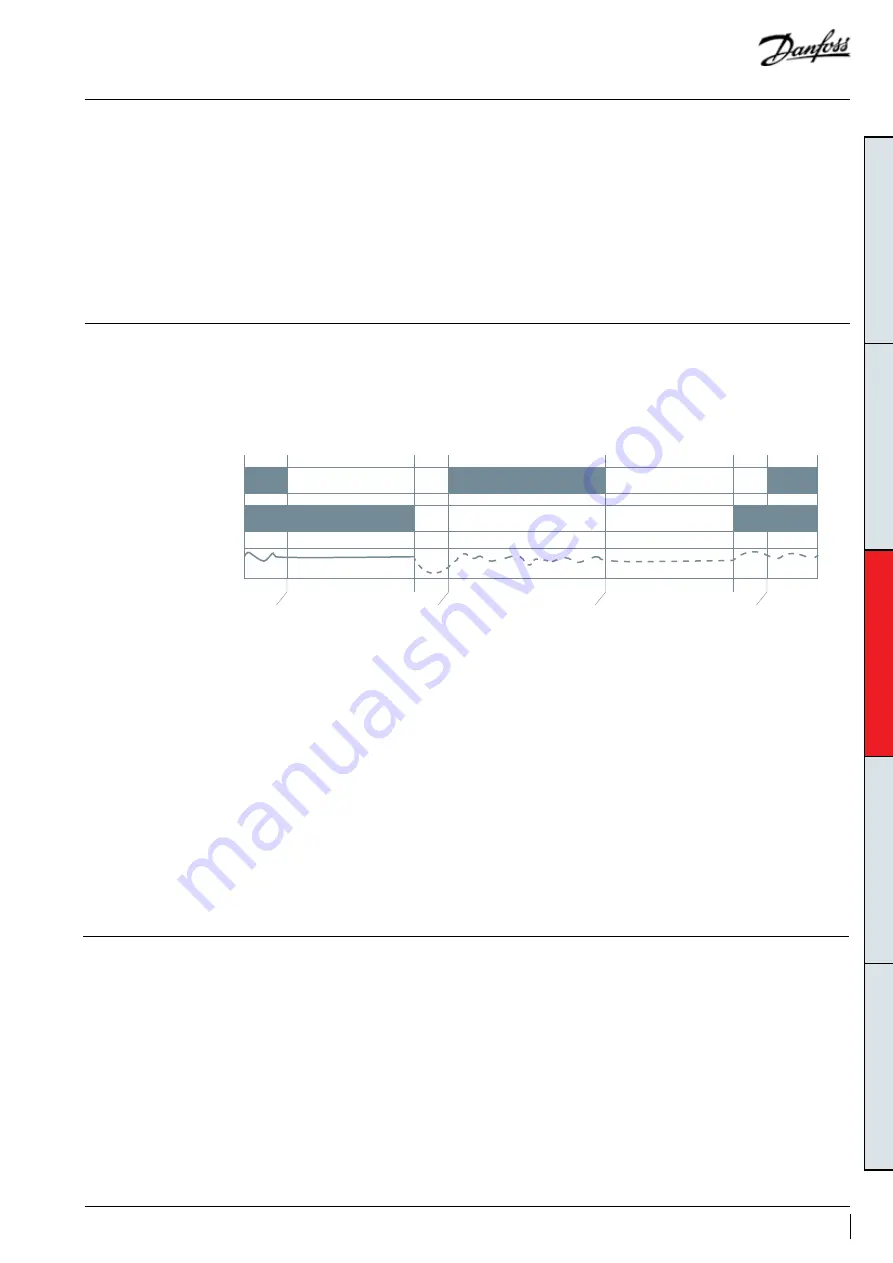
GENER
AL INFORMA
TION
PR
ODUC
T INFORMA
TION
SY
STEM DESIGN
INTEGR
ATION INT
O SY
STEM
ORDERING INFORMA
TION
Control logic
Pump-down logic
recommendations
Pump down is initiated prior to shutting
down the last compressor on the circuit by
de-energizing a liquid line solenoid valve
or closing electronic expansion valve. When
suction pressure reaches the cut-out pressure,
compressor is stopped, and liquid solenoid valve
or electronic expansion valve remains closed.
Two types of pump-down exist:
• One shot pump down (preferred): when
last compressor of the circuit stops, suction
presssure is decreased 1.5 bar below nominal
evaporating pressure. Even if suction pressure
increases again, the compressor will not restart.
• Continuous pump-down: traditional pump-
dow, Compressor restarts automatically when
suction pressure increases up to 4 cycles
maximum. A non-return valve in the discharge
line is recommended.
Defrost cycle logic
In reversible systems, the defrost logic can be
worked out to limit liquid flood back effect by:
1. Running full load during defrost to share liquid
refrigerant between all compressors.
2. Transferring liquid refrigerant from one
exchanger to the other one thanks to pressures.
* EXV Opening degree and time have to be set
to keep a minimum pressure for 4 way valve
moving.
Danfoss recommend above defrost cycle logic,
but the control logic is also system specified.
In any case, defrost logics must respect
requirements and tests described in “Manage
superheat” and “Manage operating envelope”.
The following defrost logic combines both
advantages:
Defr
ost
star
t.
St
op
the
compr
essor
4 W
ay
Valv
e (4W
V) sta
ys in hea
ting mode
.
EX
V opened t
o tr
ansf
er liquid fr
om
out
door t
o indoor ex
changer thanks t
o
pr
essur
e diff
er
enc
e
W
hen pr
essur
es ar
e almost balanc
ed
,
change 4W
V t
o c
ooling mode
.
W
hen pr
essur
es ar
e almost balanc
ed
,
change 4W
V t
o hea
ting mode
.
Star
t the c
ompr
essor
, run the
compr
essor a
t 50r
ps f
or 1min.
Af
ter
w
ar
ds
, go t
o the set speed
.
Star
t the c
ompr
essor
Defr
ost end
. St
op the c
ompr
essor
4 W
V sta
ys in c
ooling mode
.
EX
V opened t
o tr
ansf
er liquid
from indoor t
o out
door ex
changer
thanks t
o pr
essur
e diff
er
enc
e
Defr
ost
Compressor
4WV
EXV
ON
Heating
100%
Short cycle protection
Short cycling protection requirements need to be
implemented in OEM unit controller:
Meantime, the factory default setting needs to
be disabled( 28-00 short cycle protection change
from default setting “enable” to “disable”).
- 3 minutes minimum running time: in order to
get oil return back from circuit to compressor
sump
- 12 starts maximum per hour: to avoid threaten
the life time of motor and other mechanics due
to frequent starts, OEM needs to limit the starts
cycles within 12 times per hour.
- 10s minimum OFF time: to make sure discharge
valve is closed and motor is stopped before next
start, OEM needs to set the minimum off time as
10 seconds.
SY
STEM DESIGN
39
AB237586440343en-000601