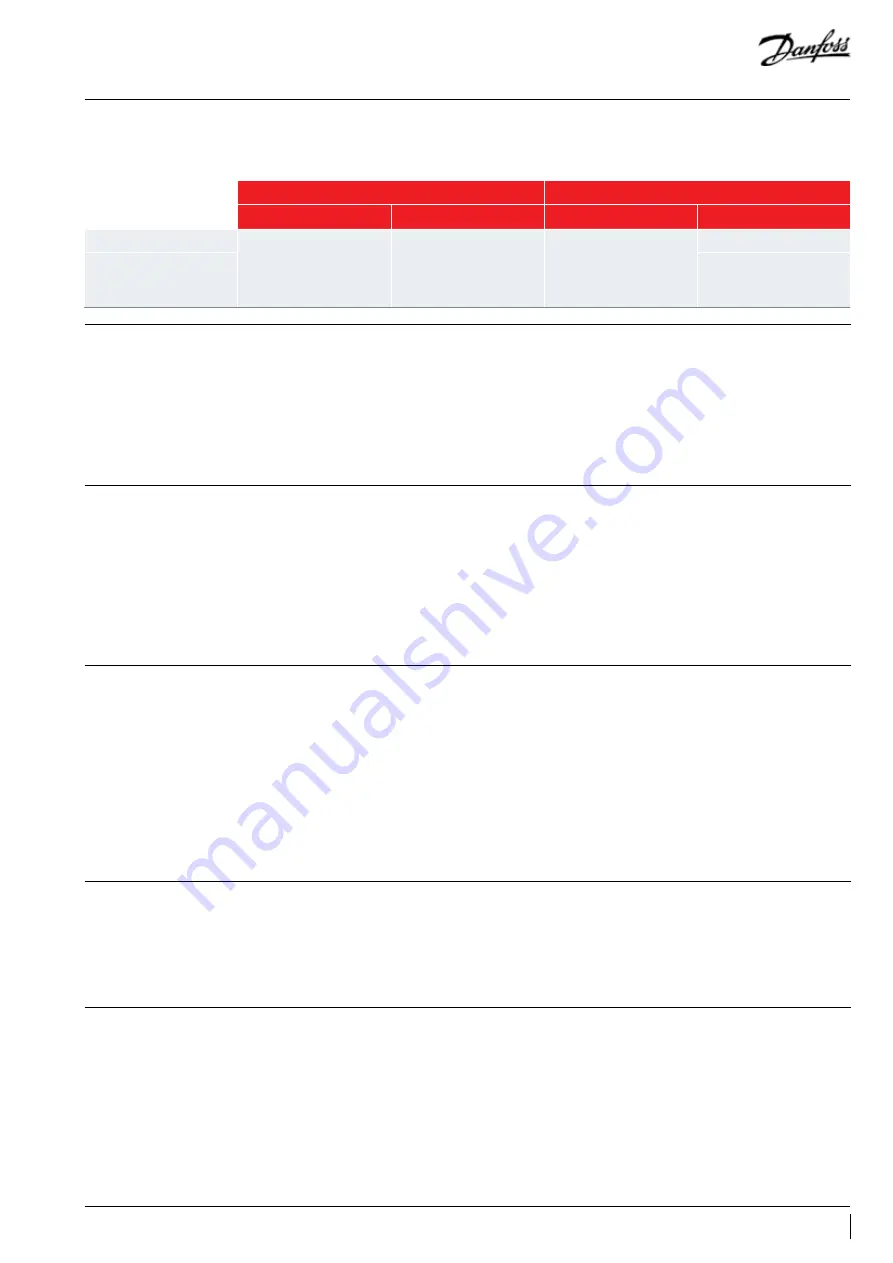
Control logic
Safety control logic
requirements
Tripping conditions
Re-start conditions
Value
Time
Value
Time
HP switch
See Pressure settings table
from section “Manage
operating envelope”
Immediate, no delay.
No by- pass
Conditions back to normal.
Switch closed again
Manual reset
LP safety switch
Maximum 5 auto reset during
a period of 12 hours, then
manual reset.
High pressure
According to EN378-2, a high-pressure (HP) safety
switch is required to shut down the compressor.
The high-pressure switch can be set to lower
values depending on the application and
ambient conditions. The HP switch must either be
placed in a lockout circuit or consist of a manual
reset device to prevent cycling around the
high-pressure limit. If a discharge valve is used,
the HP switch must be connected to the service
valve gauge port, which must not be isolated.
For CDS803 drive, HP switch can be connected to
STO (Safe Torque Off) input 37 or to an external
contactor placed between drive and compressor.
Must remove the jumper (factory supplied)
before connecting HP switch on terminals T37
and T12.
Low pressure
A low-pressure (LP) safety switch must be
used. Deep vacuum operations of a scroll
compressor can cause internal electrical arcing
and scroll instability. VLZ compressors exhibit
high volumetric efficiency and may draw very
low vacuum levels, which could induce such a
problem. The low-pressure switch must be set at
or above “Minimum Low pressure switch setting”.
The switch can be integrated directly in the safety
chain of the compressor or it can be treated by
the unit controller.
If the LP switch is connected to Terminal 27
Digital Input, it is necessary to keep a parameter
of 5.12 to default value “coast inverse” to make
sure LP cut-out has a higher priority than internal
minimum run time function.
Electronic expansion valve
Reverse rotation protection
With variable capacity systems, an electronic
expansion valve (EXV) is the strongly
recommended solution to handle refrigerant
mass flow variations. Danfoss recommends the
use of ETS products. Ramp-up and ramp-down
settings, of both EXV and compressor, must be
done with great care.
Ramp-up of the EXV must be shorter than
the ramp-up of the compressor, to avoid any
low pressure operation on suction side of the
compressor. The EXV can also be opened, up
to a certain degree, before the startup of the
compressor.
Ramp-down of the EXV must be longer than the
ramp-down of the compressor, also to avoid low
pressure operation (except with pump-down).
EXV should be closed, and remain closed,
when the compressor is off, to avoid any liquid
refrigerant entering the compressor.
Due to drive protection, compressors could work
properly even if the power connection between
the drive and mains are dis-matched. However,
the wires between compressor and drive must be
connected accordingly. To protect compressors
from reverse rotation, pressure difference could
be checked as a reference value. Use pressure
sensors to monitor pressure difference between
discharge and suction of the compressor, and for
normal operation, discharge pressure should be
at least 1 bar higher than suction pressure within
30 s running after compressor starting.
Short cycle protection
Short cycling protection requirements need to be
implemented in OEM unit controller:
Meantime, the factory default setting needs to
be disabled( 28-00 short cycle protection change
from default setting “enable” to “disable”).
- 3 minutes minimum running time: in order to
get oil return back from circuit to compressor
sump
- 12 starts maximum per hour: to avoid threaten
the lifetime of motor and other mechanics due
to frequent starts, OEM needs to limit the starts
cycles within 12 times per hour.
- 10s minimum OFF time: to make sure discharge
valve is closed and motor is stopped before next
start, OEM needs to set the minimum off time as
10 seconds.
35
AB444226142054en-000101
Содержание VLZ065
Страница 2: ......
Страница 53: ...53 AB444226142054en 000101...