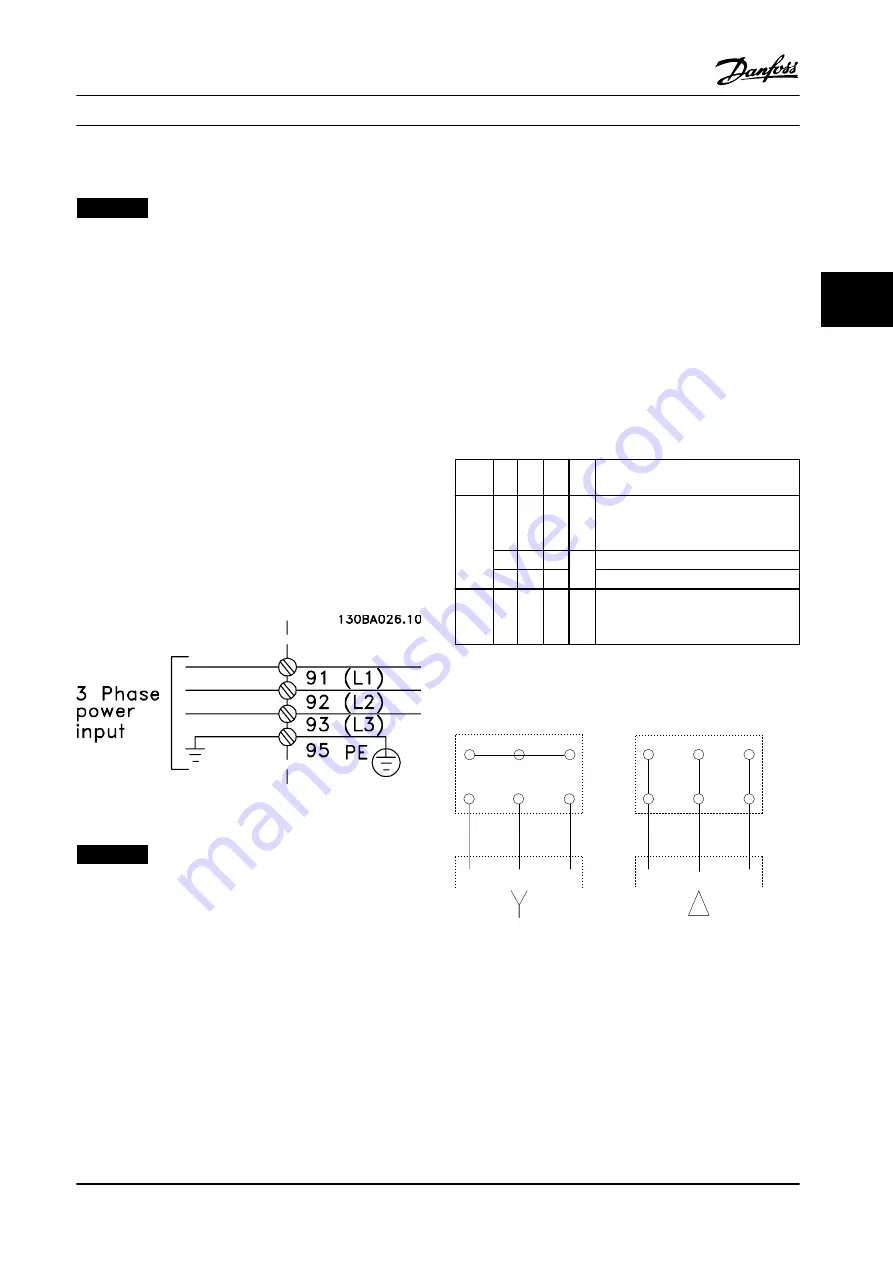
4.3 Power Connections
NOTICE!
Cables–General Information
All cabling must comply with national and local
regulations on cable cross-sections and ambient
temperature. UL applications require 167°F [75
°
C] copper
conductors. For non-UL applications, 167°F and 194°F
[75° and 90
°
C] copper conductors are thermally
acceptable.
The power cable connections are situated as shown in
. Dimension cable cross-section in accordance
with the current ratings and local legislation. See
chapter 8.3.1 Cable lengths and cross-sections
for details.
To protect the adjustable frequency drive, use the
recommended fuses if there are no built-in fuses. Fuse
recommendations are provided in
. Ensure
that proper fusing is made according to local regulation.
The AC line input connection is fitted to the line power
switch if included.
Figure 4.2 Power Cable Connections
NOTICE!
To comply with EMC emission specifications, shielded/
armored cables are recommended. If a non-shielded/
armored cable is used, see
Control Wiring for Non-shielded Cables
See
for correct dimensioning of
motor cable cross-section and length.
Shielding of cables
Avoid installation with twisted shield ends (pigtails). They
spoil the shielding effect at higher frequencies. If breaking
the shield is necessary to install a motor isolator or
contactor, continue the shield at the lowest possible HF
impedance.
Connect the motor cable shield to both the decoupling
plate of the adjustable frequency drive and to the metal
housing of the motor.
Make the shield connections with the largest possible
surface area (cable clamp). Use the installation devices
within the adjustable frequency drive.
Cable length and cross-section
The adjustable frequency drive has been EMC tested with a
given length of cable. Keep the motor cable as short as
possible to reduce the noise level and leakage currents.
Switching frequency
When adjustable frequency drives are used together with
sine-wave filters to reduce the acoustic noise from a motor,
the switching frequency must be set according to
parameter 14-01 Switching Frequency
.
Term.
no.
96 97 98 99
U
V
W PE
1)
Motor voltage 0–100% of AC line
voltage.
3 wires out of motor
U1 V1 W1
PE
1)
Delta-connected
W2 U2 V2
6 wires out of motor
U1 V1 W1 PE
1)
Star-connected U2, V2, W2
U2, V2, and W2 to be interconnected
separately.
Table 4.1 Terminal Connections
1)
Protected Ground Connection
U
1
V
1
W
1
175ZA114.11
96
97
98
96
97
98
FC
FC
Motor
Motor
U
2
V
2
W
2
U
1
V
1
W
1
U
2
V
2
W
2
Figure 4.3 Y and Delta Terminal Configurations
4.4 Grounding
Note the following basic issues for electromagnetic
compatibility (EMC) during installation:
•
Safety grounding: The adjustable frequency drive
has a high leakage current and must be
grounded appropriately for safety reasons. Always
follow local safety regulations.
•
High-frequency grounding: Keep the ground wire
connections as short as possible.
Electrical Installation
Installation Manual
MG37A322
Danfoss A/S © Rev. 04/2015 All rights reserved.
37
4
4
Содержание VLT AutomationDrive FC 302
Страница 2: ......
Страница 127: ...Index Installation Manual MG37A322 Danfoss A S Rev 04 2015 All rights reserved 125...