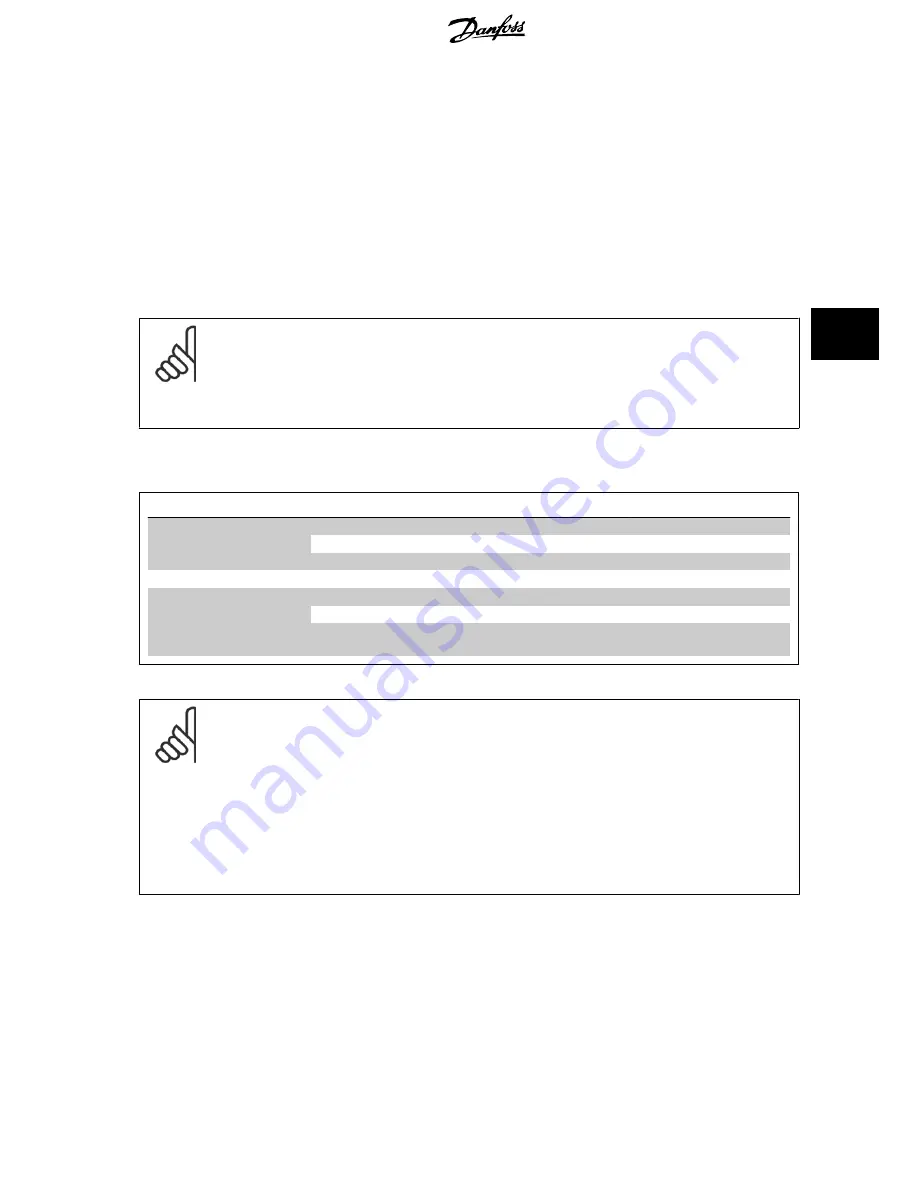
5.2.7 Cooling and Airflow
Cooling
Cooling can be obtained in different ways, by using the cooling ducts in the bottom and the top of the unit, by taking air in and out the back of the unit
or by combining the cooling possibilities.
Duct cooling
A dedicated option has been developed to optimize installation of IP00/chassis frame frequency converters in Rittal TS8 enclosures utilizing the fan of
the frequency converter for forced air cooling of the backchannel. The air out the top of the enclosure could but ducted outside a facility so the heat loses
from the backchannel are not dissipated within the control room reducing air-conditioning requirements of the facility.
Please see
Installation of Duct Cooling Kit in Rittal enclosures
, for further information.
Back cooling
The backchannel air can also be ventilated in and out the back of a Rittal TS8 enclosure. This offers a solution where the backchannel could take air from
outside the facility and return the heat loses outside the facility thus reducing air-conditioning requirements.
NB!
A doorfan(s) is required on the Rittal cabinet to remove the loses not contained in the backchannel of the drive. The minimum doorfan(s)
airflow required at the drive maximum ambient for the D3 and D4 is 391 m^3/h (230 cfm). The minimum doorfan(s) airflow required
at the drive maximum ambient for the E2 is 782 m^3/h (460 cfm). If the ambient is below maximum or if additional components, heat
loses, are added within the enclosure a calculation must be made to ensure the proper airflow is provided to cool the inside of the
Rittal enclosure.
Airflow
The necessary airflow over the heat sink must be secured. The flow rate is shown below.
Enclosure protection
Frame size
Door fan / Top fan airflow
Airflow over heatsink
IP21 / NEMA 1
IP54 / NEMA 12
D1 and D2
170 m
3
/h (100 cfm)
765 m
3
/h (450 cfm)
E1
340 m
3
/h (200 cfm)
1444 m
3
/h (850 cfm)
IP21 / NEMA 1
F1, F2, F3 and F4
700 m
3
/h (412 cfm)*
985 m
3
/h (580 cfm)
IP54 / NEMA 12
F1, F2, F3 and F4
525 m
3
/h (309 cfm)*
985 m
3
/h (580 cfm)
IP00 / Chassis
D3 and D4
255 m
3
/h (150 cfm)
765 m
3
/h (450 cfm)
E2
255 m
3
/h (150 cfm)
1444 m
3
/h (850 cfm)
* Airflow per fan. Frame size F contain multiple fans.
Table 5.2: Heatsink Air Flow
NB!
The fan runs for the following reasons:
1.
AMA
2.
DC Hold
3.
Pre-Mag
4.
DC Brake
5.
60% of nominal current is exceeded
6.
Specific heatsink temperature exceeded (power size dependent).
Once the fan is started it will run for minimum 10 minutes.
5.2.8 Gland/Conduit Entry - IP21 (NEMA 1) and IP54 (NEMA12)
Cables are connected through the gland plate from the bottom. Remove the plate and plan where to place the entry for the glands or conduits. Prepare
holes in the marked area on the drawing.
VLT
®
AQUA Drive Design Guide
5 How to Install
MG.20.N5.02 - VLT
®
is a registered Danfoss trademark
117
5
Содержание VLT AQUA Drive Series
Страница 38: ...3 VLT AQUA Selection VLT AQUA Drive Design Guide 38 MG 20 N5 02 VLT is a registered Danfoss trademark 3...
Страница 106: ...5 How to Install VLT AQUA Drive Design Guide 106 MG 20 N5 02 VLT is a registered Danfoss trademark 5...
Страница 150: ...5 How to Install VLT AQUA Drive Design Guide 150 MG 20 N5 02 VLT is a registered Danfoss trademark 5...
Страница 168: ...7 RS 485 Installation and Set up VLT AQUA Drive Design Guide 168 MG 20 N5 02 VLT is a registered Danfoss trademark 7...
Страница 194: ...8 Troubleshooting VLT AQUA Drive Design Guide 194 MG 20 N5 02 VLT is a registered Danfoss trademark 8...