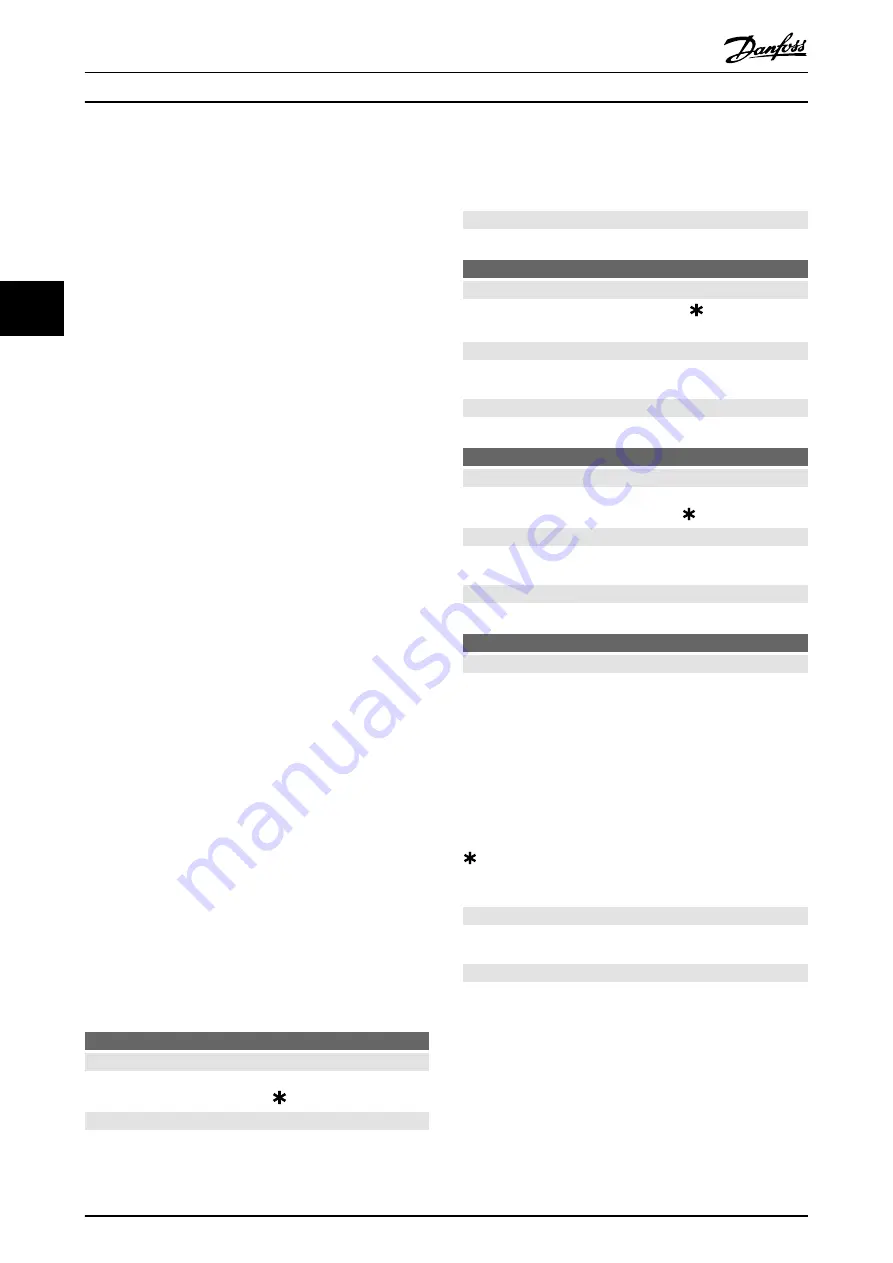
DC link voltage [V]
gives the intermediate circuit voltage of
the frequency converter.
Thermal load motor [%]
gives the calculated/estimated load
on the motor. 100 % is the cut-out limit.
Thermal load [%]
gives the calculated/estimated thermal
load on the frequency converter. 100 % is the cut-out limit.
Running hours [Hours]
gives the number of hours that the
motor has tun since the last reset in
parameter 619 Reset of
running hours counter
.
Digital input [Binary code]
gives the signal status from the 5
digital inputs (18, 19, 27, 29 and 33). Terminal 18
corresponds to the bit on the extreme left. `0'=no signal,
`1'=signal connected.
Analog input 53 [V]
gives the voltage value of terminal 53.
Analog input 60 [mA]
gives the present value of terminal
60.
Pulse reference [Hz]
gives the reference in Hz connected to
terminal 33.
External reference [%]
gives the sum of external references
as a percentage (sum of analog/pulse/serial communi-
cation) in the range from Minimum reference, Ref
MIN
to
Maximum reference, Ref
MAX
.
Status word [Hex]
gives one or several status conditions in
a hex code. See
chapter 4.7 Serial communication
for
further information.
Heat sink temp.[°C]
gives the present heat sink temperature
of the frequency converter. The cut-out limit is 90-100 °C,
while cutting back in occurs at 70 ±5 °C.
Alarm word [Hex]
gives one or several alarms in hex code.
See
chapter 4.7 Serial communication
for further
information.
Control word [Hex]
gives the control word for the frequency
converter. See
chapter 4.8 Serial Communication Parameters
for further information.
Warning word [Hex]
gives one or several warnings in hex
code. See
chapter 4.8 Serial Communication Parameters
for
further information.
Extended status word [Hex]
gives one or several status
modes in hex code. See
chapter 4.7 Serial communication
for further information.
Communication option card warning [Hex]
gives a warning
word if there is a fault in the communication bus. Only
active if communication options are installed.
If there are no communication options, 0 hex is displayed.
Pulse count
gives the number of pulses that the unit has
registered.
Power [W]
gives the present power that the motor is
absorbing in W.
010
Small display line 1.1
Value:
See
par. 009 Large display
readout
Analog input 53 [V] [17]
Function:
In this parameter, the first of 3 data values can be selected
that is to be displayed in the LCP control unit display, line
1, position 1. This is a useful function, e.g. when setting
the PID regulator, as it gives a view of process reactions to
reference changes. Press [Display Status] to activate the
display readout.
Description of choice:
See
parameter 009 Large display readout
.
011
Small display readout 1.2
Value:
See
parameter 009 Large display
readout
Motor current [A]
[6]
Function:
See the functional description given in
parameter 010 Small
display readout
.
Description of choice:
See
parameter 009 Large display readout
.
012
Small display readout 1.3
Value:
See
parameter 009 Large display
readout
Feedback [unit] [3]
Function:
See the functional description given under
parameter 010
Small display readout
.
Description of choice:
See
parameter 009 Large display readout
.
013
Local control
Value:
Local not active (DISABLE)
[0]
Local control and open loop without slip compen-
sation
(LOC CTRL/OPEN LOOP)
[1]
Remote-operated control and open loop without
slip compensation
(LOC+DIG CTRL)
[2]
Local control as
parameter 100 Configuration
(LOC CTRL/AS P100)
[3]
Remote-operated control as
parameter 100 Config-
uration
(LOC+DIG CTRL/AS P100)
[4]
Function:
This is where the required function is selected if
[1] Local
operation
has been selected in Parameter 002.
Description of choice:
If
[0] Local not active
is selected, it is not possible to set a
reference via
parameter 003 Local reference
.
To enable a shift to
[0] Local not active
, set
parameter 002
Local/remote operation
to
[0] Remote operation
.
Select
[1] Local control and open loop
if the motor speed is
to be set via
parameter 003 Local reference
. When this
selection is made,
parameter 100 Configuration
automat-
ically shifts to
[0] Speed regulation, open loop
.
[2] Remote-operated control and open loop
functions in the
same way as
[1] Local control and open loop
; however, the
Programming
Design Guide
64
Danfoss A/S © Rev. May/2014 All rights reserved.
MG27E402
4
4