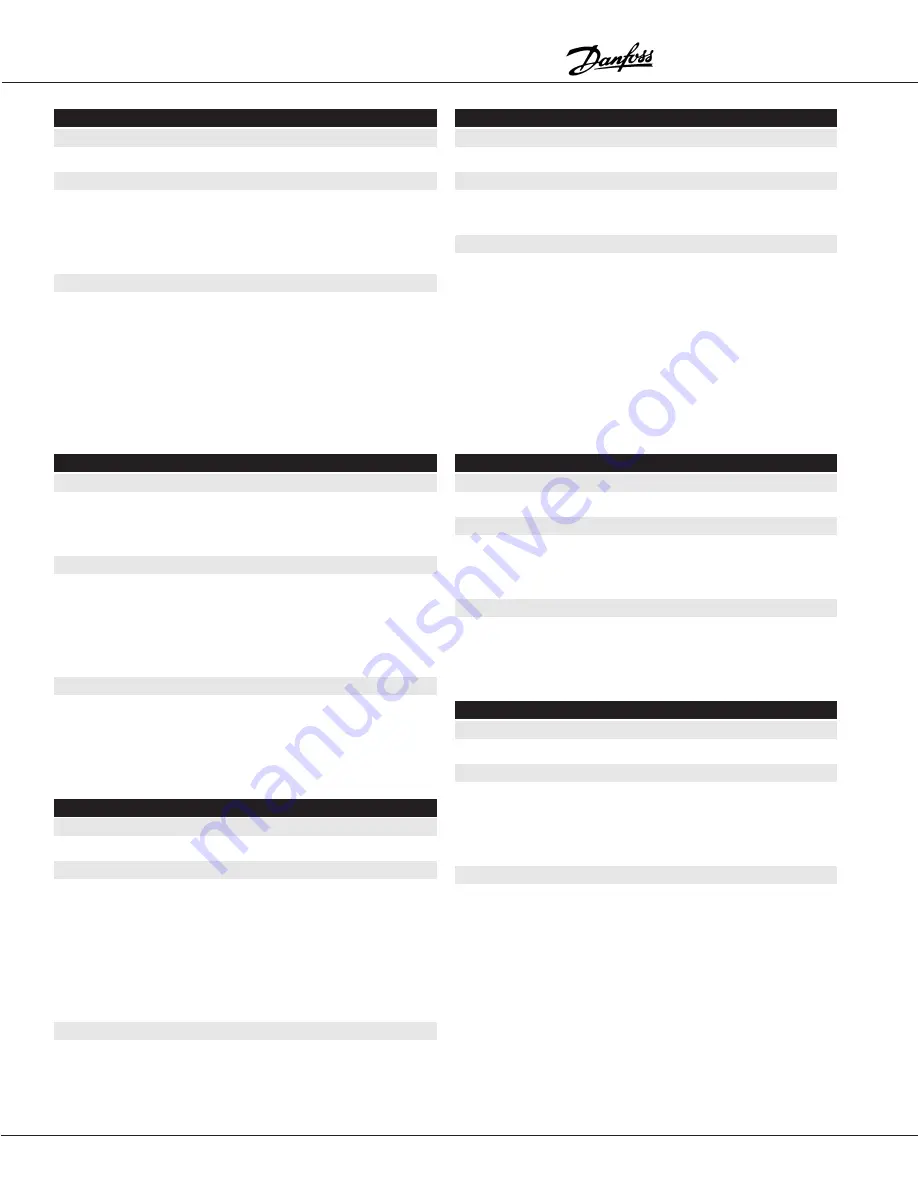
20
★
= ROM default setting. Text in ( ) = display text. Figures in [ ] are used when communicating with the bus.
Programming
VLT
®
Series 2000
112 Slip Compensation (SLIP COMP.)
Value:
0.0 - 20 Hz
Function:
Slip Compensation increases the output frequency and
voltage of the VLT adjustable frequency drive with an
increasing load to compensate for the motor's increasing
slip (loss). This achieves a load-independent speed.
Description:
Choose a value so that the speed remains constant when
the load increases. If the value is too high the speed
increases with the load. This may lead to unstable motor
operation.
When you use synchronous motors and motors connected
in parallel, set slip compensation to 0 Hz. Slip
compensation should be avoided in case of high dynamics.
114 Feedback Signal (FEEDBACK T)
Value:
Voltage (VOLTAGE)
[0]
★
Current (CURRENT)
[1]
Pulses (PULSES)
[2]
Function:
This parameter allows a choice of process feedback signal
in a closed loop system, as chosen in parameter 101. It has
no effect if parameter 101 is set to OPEN LOOP.
For further information, see the section on the PID
controller.
Description of choice:
If a PID controller is used, one of the inputs on terminal 29
(parameter 405), terminal 53 (parameter 412) or terminal
60 (parameter 413) must be used for the feedback signal.
The same type of signal cannot be the reference signal.
119 FF Factor (FEED FWD F)
Value:
0 to 500%
★
100%
Function:
This parameter is used in connection with a PI controller.
The FF factor makes a large or small part of the reference
signal around the PID controller so that the PI controller
only affects part of the control signal. Any change of the
setpoint will affect the motor rpm directly. The FF factor
gives high dynamics at changes of the setpoint and less
overswing.
Description of choice:
You can choose the required % value in the interval f
MIN
-f
MAX
Choose a value above 100% if the setpoint variations are
only minor.
120 Control Range (CONTRL RAN)
Value:
0 to 100%
★
100%
Function:
The regulator range (bandwidth) limits the output from the
PID controller as a % of f
MAX
.
Description of choice:
A desired % value of f
MAX
can be selected. If the regulator
range is reduced, speed variations will become smaller
during initial adjustment.
121 Proportional Gain (PROPRT/L G)
Value:
0.01 to 10.00
★
0.01
Function:
The proportional gain sets the amplification factor of the
error (the difference between the feedback signal and the
setpoint).
Description of choice:
Quick regulation is obtained at a high amplification, but if
the amplification is too high, the process may become
unstable due to overshoot.
122 Integral Time (INTEGRAL T)
Value:
0.01 to 7200 sec.
★
OFF
Function:
The integral time determines how long the PI controller
takes to correct the fault. The integral time results in a delay
of the signal, and therefore has a dampening effect that will
improve stability.
Description of choice:
Quick regulation is obtained through a short integral time.
However, if this time is set too short, the process will
become unstable. If the integral time is set long, regulation
becomes unnecessarily slow.
Off means that the function is
inactive.
∆
!
WARNING: The output frequency is limited by
0.9 x f
MIN
and 1.1 x f
MAX
no matter what the band
width setting is. The controller can therefore be
active without affect the output frequency can
exceed f
MAX
by 10%.
Artisan Technology Group - Quality Instrumentation ... Guaranteed | (888) 88-SOURCE | www.artisantg.com