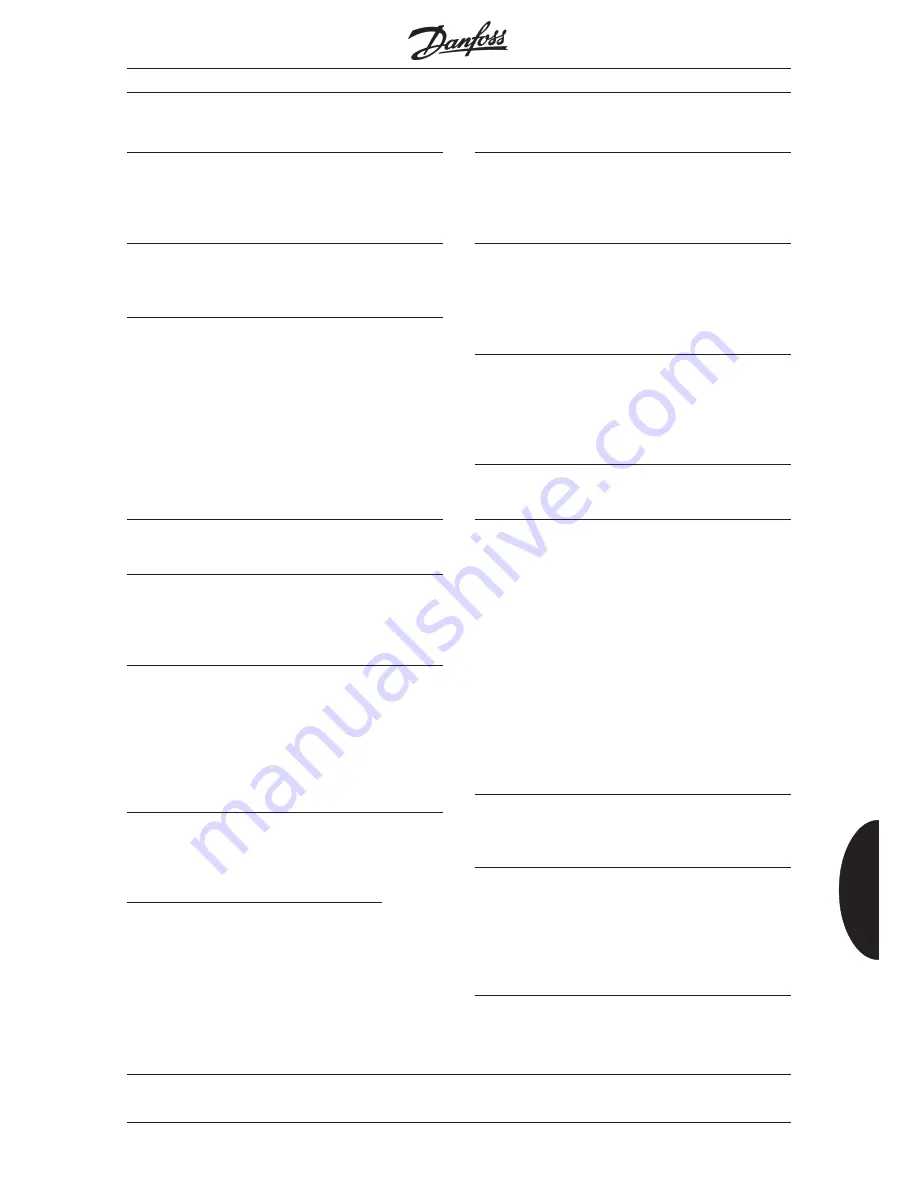
MG.20.B6.02 – VLT is a registered Danfoss trademark
63
VLT
®
2000 Series
Section 1
Section 2
Section 3
103 Motor power
(MOTOR POWER)
Value:
Under size
[0]
✭
Nom. size
[1]
Over size
[2]
Function:
Using this parameter you can select the kW value
closest to the motor’s rated output.
The frequency converter has three preset kW values.
The exact kW value will depend on unit type.
Description:
Read the rated motor power on the type plate of the
motor and choose the relevant factory setting for the
motor size. Parameters 107, 108, 109, 110, 111 and
112 change automatically when the value in parame-
ter 103 is changed.
104 Motor voltage
(MOTOR VOLTAGE)
Value:
Only 200-240 V units
200 V (200 V)
[0]
208 V (208 V)
[1]
✭
220 V (220 V)
[2]
230 V (230 V)
[3]
240 V (240 V)
[4]
Only 380-460 V units
380 V (380 V)
[0]
✭
400 V (400 V)
[1]
415 V (415 V)
[2]
440 V (440 V)
[3]
460 V (460 V)
[4]
Function:
Using this parameter you can select the rated voltage
closest to the motor’s voltage.
Description:
You can choose among different voltage values. The
value is selected on the basis of the data on the mo-
tor plate.
Parameters 107, 108, 109, 110 and 111 are changed
automatically when the value of parameter 104 is
changed.
✭
= Factory setting. Text in ( ) = Display text. The figures in [ ] are used in bus communication.
Description of parameters
101 Speed control
(SPEED CONTROL)
Value:
Open loop (OPEN LOOP)
[0]
✭
Slip comp. (SLIP COMP)
[1]
Closed loop (CLOSED LOOP)
[2]
Function:
You can choose among three different kinds of speed
control:
Open loop
,
Slip compensated
and
Closed loop
.
Description:
Choose
Slip compensation
for normal operation, where
the speed must be constant no matter what the load is.
Choose
Open loop
when the motors used are paral-
lel-connected in parallel or when synchronous motors
are used.
Choose
Closed loop
when you want operation with
process feedback. For closed loop operation you
must choose the feedback type in parameter 114
(current, voltage or pulses). See also the section on PI
controller, page 53.
102 Current limit control (
CURRENT LIMIT)
Value:
✭
Preprogrammed value (PROGRAM SET)
[0]
Voltage signal (10 VDC SIGNAL)
[1]
Current signal (20 mA SIGNAL)
[2]
Function:
You can choose to control the speed by means of the
current limit. This makes indirect torque control
possible.
The current limit can be set in parameter 209 or by
means of a current or voltage signal in parameter 412
or 413.
Description:
Choose between controlling the current limit via para-
meter 209 or one of the analogue inputs, terminal 53
or 60.
10 V / 20 mA
corresponds to 160 % current
(2030: 140 %).
Do not select the same signal for PI control.
■
■
■
■