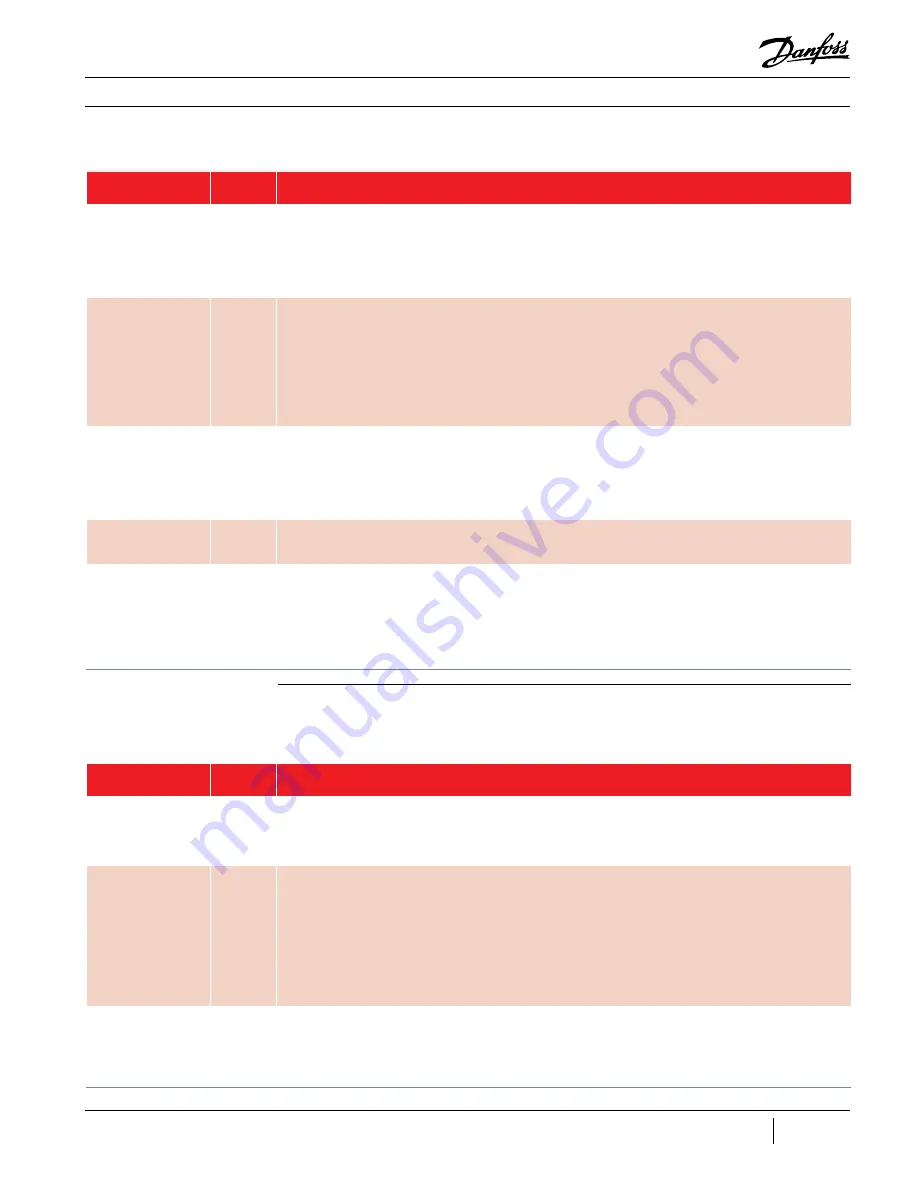
103 of 132
M-SV-001-EN Rev.E
Troubleshooting
Table 23 - Motor Faults
(Continued)
Table 24 - Bearing Status
Motor Fault
Description
Trigger
Method
Troubleshooting
24VDC Under/Over
Voltage Fault
RFT
Suggests the measured 24VDC supply voltage is out of range.
Measure the 24VDC test points at the Backplane.
Compare the measured voltages to the displayed readings in the Compressor Monitor Tool and Fault and Event
Log details to determine conditions related to the fault.
If the measured voltage is incorrect, verify the DC/DC Converter. See Section 3.9.3.
Determine that one of the modules is not draining energy. See Section 4.5.2.
If the fault occurs when the compressor is given the demand to run, the Inverter may be causing the 24VDC fault.
Low Motor Back EMF
Fault
DFT
The calculated magnetic strength of the shaft has fallen below the minimum limit. This can be a temporary effect
due to high load and elevated temperatures (will recover when cavity temperature cools) or due to a permanent
demagnetization of the shaft.
If this fault occurs three times within a 30-minute period, a Lock-Out Fault will occur.
Compare the Back EMF value to the displayed readings in the Compressor Monitor Tool and Fault and Event Log
details to determine conditions related to the fault.
Permanent damage to Back EMF can be caused by insufficient motor cooling, repeated overheating of cavity,
faulty Inverter, faulty BMCC, repeated Rotor May Be Locked or Single phase Over-Current faults. See Inverter Error.
Verify the Inverter. See Section 3.7.3.1.
Verify the Stator. See Section 3.8.4.
Generator Mode
Active
DFT
Indicates, at greater than 0 RPM, the measured actual DC Bus voltage has fallen below the Generator Mode
Enabled Level value. Also, could be electronic “noise” when no actual drop in voltage has occurred.
Measure the incoming main AC voltage.
Measure the DC bus voltage using the DC Bus Test Harness.
Compare the measured voltages to the displayed readings in the
Compressor Monitor Tool
and Fault and Event
Log details to determine conditions related to the fault.
Typically, this fault is recorded when power to the compressor is removed while it is running.
EEPROM Checksum
Fault
INS
Indicates there is an error reading the EEPROM in the BMCC.
Perform a bearing calibration and save to EEPROM, cycle the power.
If the error is still present, the BMCC must be replaced.
SCR Ripple Voltage
Fault
AFT
Indicates that a voltage imbalance may exist between the incoming AC phases.
Measure the difference in current and voltage between the phases.
If there is a current imbalance (more than 5%) between the phases, verify the incoming AC power supply.
Review the Compressor Monitor Tool for SCR Voltage Ripple readings at the time of the fault.
Phase imbalance can be caused by a faulty SCR, SCR Gate, Gate control from the Soft Start Board or a faulty power
capacitor.
Verify the SCRs. See Section 3.5.3.
Verify the Soft Start Board. See Section 3.4.3.
Bearing Fault
Description
Trigger
Method
Troubleshooting
Startup Calibration
Check Fault
INS
During compressor start-up, the stored bearing calibration is verified. Indicates that the calibration
failed during compressor start-up. Manually calibrate the bearings and save to EEPROM, cycle the power.
Review the calibration report to determine conditions related to the fault.
If the bearings cannot pass calibration after three attempts, verify the PWM (see Section 3.16.3), bearing sensors
(see Section 3.18.3) and bearings (see Section 3.17.3).
Bearing Displacement
Fault
INS
The shaft position has been measured outside the bearing displacement maximum in one of the five
bearing positions.
This fault can be the result of system-related issues, such as EXV control issues (i.e., starving the
evaporator or pumping liquid), operating at the surge line, check valve failure, or IGV failure.
Review
Fault and Event Log
details to determine conditions related to the fault. Using the
Compressor
Configuration tool
, set the Control Mode to Manual. Using the
Compressor Monitor
, levitate the shaft and record
the bearing forces. Greater than 2A indicates a bearing issue.
Manually calibrate the bearings, save to EEPROM and identify if bearing forces improve.
If the bearings cannot be calibrated after three attempts, verify the PWM (see Section 3.16.3), bearing sensors (see
Section 3.18.3) and bearings (see Section 3.17.3).
Review the calibration report to determine conditions related to the fault.
Bearing Overcurrent
Fault
INS
Indicates that the current drawn by the bearing exceeds the maximum amps in one of the five bearing
positions.
Using the
Compressor Configuration
tool, set the Control Mode to Levitate Only Mode. Using the
Compressor Monitor
,
levitate the shaft and record the bearing forces. Greater than 2A indicates an issue.
Manually calibrate the bearings, save to EEPROM and identify if bearing forces improve.
If the bearings
cannot be calibrated after three attempts, verify the PWM (see Section 3.16.3), bearing sensors (see Section 3.18.3)
and bearings (see Section 3.17.3).
Review the calibration report to determine conditions related to the fault.
4.2.3 Bearing Status
Содержание Turbocor TG230
Страница 2: ...THIS PAGE INTENTIONALLY LEFT BLANK ...
Страница 4: ...4 of 132 M SV 001 EN Rev E THIS PAGE INTENTIONALLY LEFT BLANK ...
Страница 12: ...12 of 132 M SV 001 EN Rev E THIS PAGE INTENTIONALLY LEFT BLANK ...
Страница 28: ...28 of 132 M SV 001 EN Rev E Compressor Fundamentals Figure 18 Compressor Energy and Control Flow Block Diagram ...
Страница 61: ...61 of 132 M SV 001 EN Rev E Compressor Components Figure 56 Stator Thermistor R T Curve 1 ...
Страница 120: ...120 of 132 M SV 001 EN Rev E THIS PAGE INTENTIONALLY LEFT BLANK ...
Страница 130: ...130 of 132 M SV 001 EN Rev E Notes ...