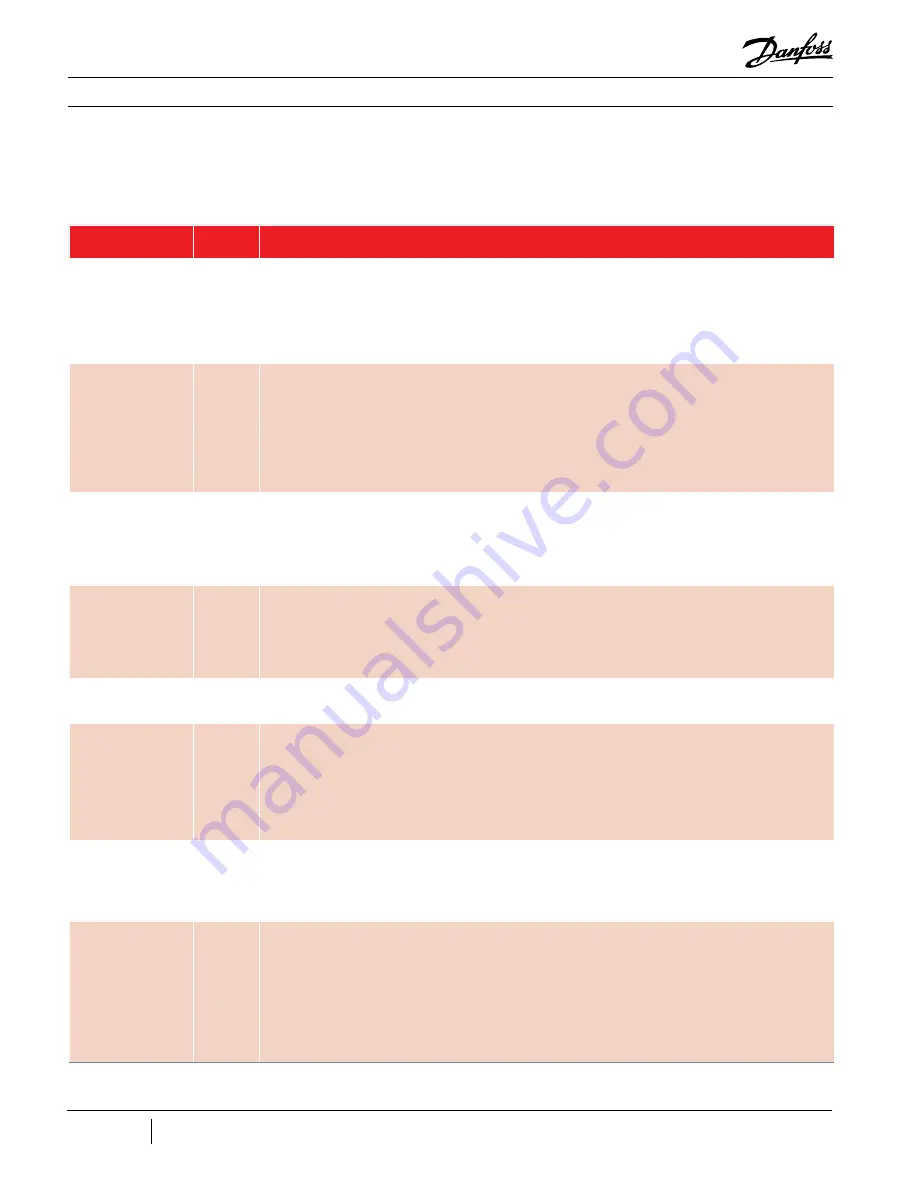
102 of 132
M-SV-001-EN Rev.E
Troubleshooting
4.2.2 Motor
Faults/System Status
Table 23 - Motor Faults
Motor Fault
Description
Trigger
Method
Troubleshooting
Motor Single Phase
Overcurrent Fault
AFT
One phase of the Inverter to motor is generating high current.
Review Fault and Event Log details to determine conditions related to the fault. This fault can be a result of liquid
carryover, a loss of shaft magnetic strength, see Back EMF is Low fault, or Inverter failure, see Inverter Error fault.
Verify the Stator. See Section 3.8.4.
Verify the Inverter and the Inverter cable connections. See Section 3.7.3.
This fault can be related to BMCC Inverter switching control. Verify the BMCC. See Section 3.14.3. If fault/event
logs show occurrence of Single Phase Over-Current fault after one Inverter Error, the Inverter should be verified
and may require replacement.
DC Bus Overvoltage
Fault
AFT
Suggests that the DC bus voltage is above the Maximum DC Bus Voltage.
Measure the incoming main AC voltage.
Measure the DC bus voltage using the DC Bus Test Harness. See Section 3.6.3.1.
Compare the measured voltages to the displayed readings in the Compressor Monitor Tool and details in the Fault
and Event Log to determine conditions related to the fault.
Correct the incoming main AC voltage if it is higher than the maximum recommended value for the application.
If the measured DC bus voltage exceeds the Maximum DC Bus Voltage and incoming main AC voltage is correct,
verify the Soft Start. See Section 3.4.3.1.
All 3-phase voltage information displayed in the SMT is calculated from DC bus voltage, as measured by the
Inverter, verify the Inverter and its connections. See Section 3.7.3.1.
Motor Overcurrent
Fault
AFT
Suggests AC input voltage is too low or the compressor is overloaded.
If this fault occurs three times within a 30-minute period, a Lock-Out Fault will occur.
Verify the 3-phase AC input voltage is above the minimum recommended value for the application.
Heavy, saturated gas can cause the motor to overwork and generate high current. Ensure superheated gas is
entering the compressor suction port.
Verify the Inverter. See Section 3.7.3.1.
Verify the Stator. See Section 3.8.4.
Inverter Error
INS
Indicates there is an error within the Inverter Control Board or no BMCC communication with the Inverter.
If this fault occurs three times within a 30-minute period, a Lock-Out Fault will occur.
Verify the Inverter and the Inverter cable connections. See Section 3.7.3.1. If the Inverter Error fault persists after
the Inverter is verified, it should be replaced.
Review the Fault and Event Log for recorded occurrences of this fault. Any occurrence of Single Phase Over-
current, Back EMF is Low or Rotor May Be Locked faults immediately following an Inverter Error fault most likely
indicates a bad Inverter.
Bearing Fault Active
INS
If a bearing fault type is present, the Bearing Error is triggered.
This is not an actual fault, only an indication that a fault has occurred in the Bearing section. See Table 21 (Bearing
Fault Types).
Rotor Starting Torque
Fault
INS
At low speed (startup) rotor angular position is not at correct value for a given speed, caused by low shaft magnet
strength, liquid flooded compressor or damaged touchdown bearings/physical contact of rotating components.
If this fault occurs three times within a 30-minute period, a Lock-Out Fault will occur. If fault or event logs show
occurrence of Rotor May Be Locked fault after one Inverter Error, the Inverter should be verified and may require
replacement. See Inverter Error or Single Phase Over-Current.
Verify the bearing calibration and levitation.
Verify the Inverter. See Section 3.7.3.1.
Verify the Stator. See Section 3.8.4.
Review Fault and Event Log details to determine conditions related to the fault.
Low Inverter Current
Fault
AFT
Suggests the compressor has no load, verify load is available. Minimum magnetizing power not absorbed for
given speed at the Inverter.
Compressor is not pumping. Usually seen in open-air run.
Review the Fault Log for the level of Motor Current in the fault record.
Zero motor current at zero RPM indicates a problem with the Inverter. Verify the Inverter. See Section 3.7.3.1.
Verify the Stator. See Section 3.8.4.
DC Bus Under/Over
Voltage Fault
DFT
At 0 RPM: If the measured DC Bus voltage is lower than Soft Start charge voltage, a DC bus voltage fault is
recorded. All 3-phase voltage information displayed in the SMT is calculated from DC bus voltage, as measured by
the Inverter.
Typically, this fault is recorded when power to the compressor is removed.
Measure the incoming main AC voltage.
Compare the measured voltages to the displayed readings in the Compressor Monitor Tool and Fault and Event
Log details to determine conditions related to the fault.
Measure the DC bus voltage using the DC Bus Test Harness. See Section 1.9.2.
Verify the Soft Start. See Section 3.4.3.
Verify the SCRs. See Section 3.5.3.
Verify the connections to the Inverter.
Содержание Turbocor TG230
Страница 2: ...THIS PAGE INTENTIONALLY LEFT BLANK ...
Страница 4: ...4 of 132 M SV 001 EN Rev E THIS PAGE INTENTIONALLY LEFT BLANK ...
Страница 12: ...12 of 132 M SV 001 EN Rev E THIS PAGE INTENTIONALLY LEFT BLANK ...
Страница 28: ...28 of 132 M SV 001 EN Rev E Compressor Fundamentals Figure 18 Compressor Energy and Control Flow Block Diagram ...
Страница 61: ...61 of 132 M SV 001 EN Rev E Compressor Components Figure 56 Stator Thermistor R T Curve 1 ...
Страница 120: ...120 of 132 M SV 001 EN Rev E THIS PAGE INTENTIONALLY LEFT BLANK ...
Страница 130: ...130 of 132 M SV 001 EN Rev E Notes ...