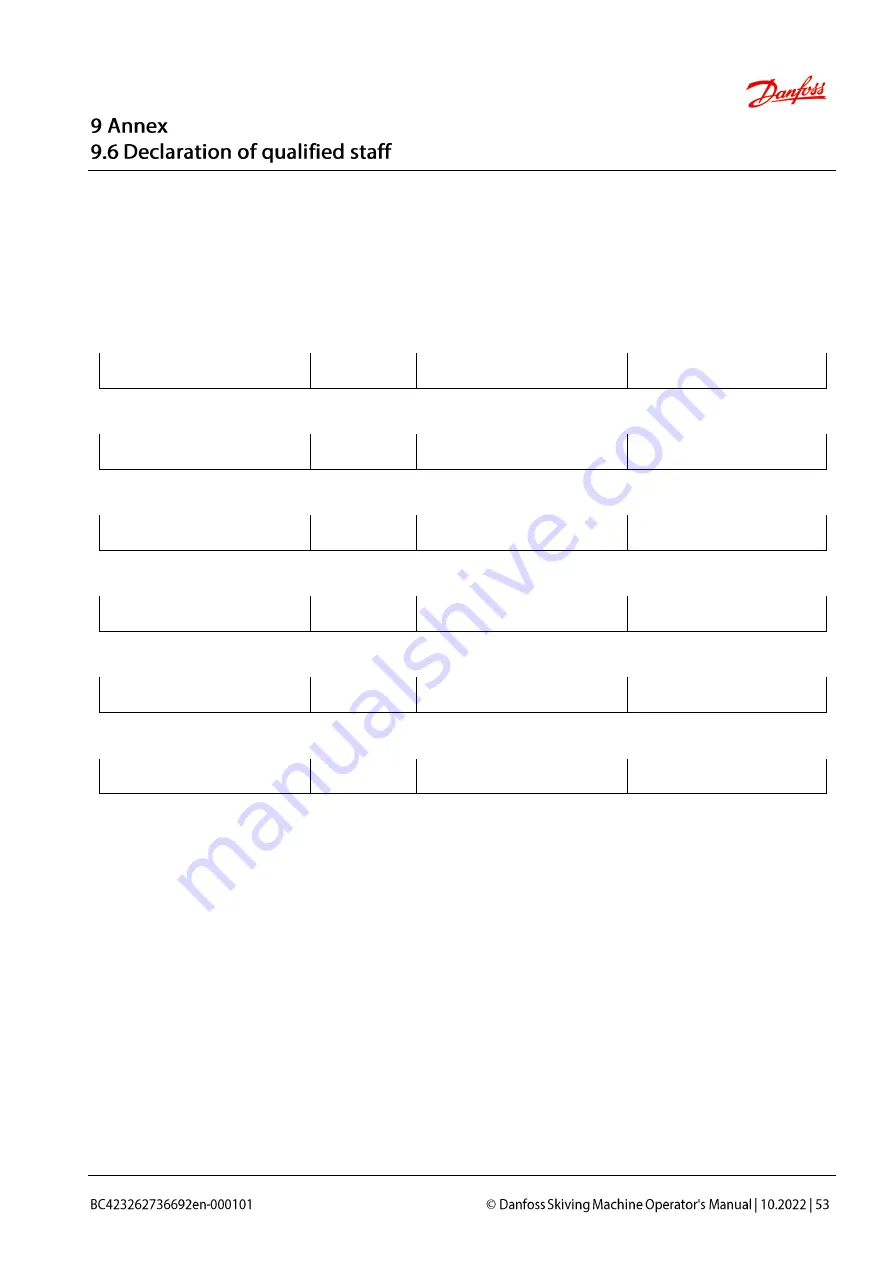
9.6 Declaration of qualified staff
I herewith declare that I have attended an internal training for the op-
eration of the UNIFLEX machine and have been informed on all
safety-related details. In addition I declare that I have read and under-
stood this Operation Manual completely.
City
Date
Name
Signature
City
Date
Name
Signature
City
Date
Name
Signature
City
Date
Name
Signature
City
Date
Name
Signature
City
Date
Name
Signature
Содержание ET6110
Страница 1: ......
Страница 3: ......
Страница 9: ...1 3 Name plate The name plate is fixed near the power cable...
Страница 31: ...10 Pull the skived workpiece out of the skiving machine...
Страница 48: ...Position Anzahl Artikelnummer Bezeichnung 14 1 307 257 3 Pulley...
Страница 50: ...9 3 Spare parts set Quantity Part code Designation 1 307 053 Spare part set...
Страница 51: ...9 4 Electric diagram...
Страница 52: ...9 5 Maintenance log Inside skiving knife Outside skiving knife Remark Date Signature...
Страница 54: ......
Страница 55: ......
Страница 56: ......