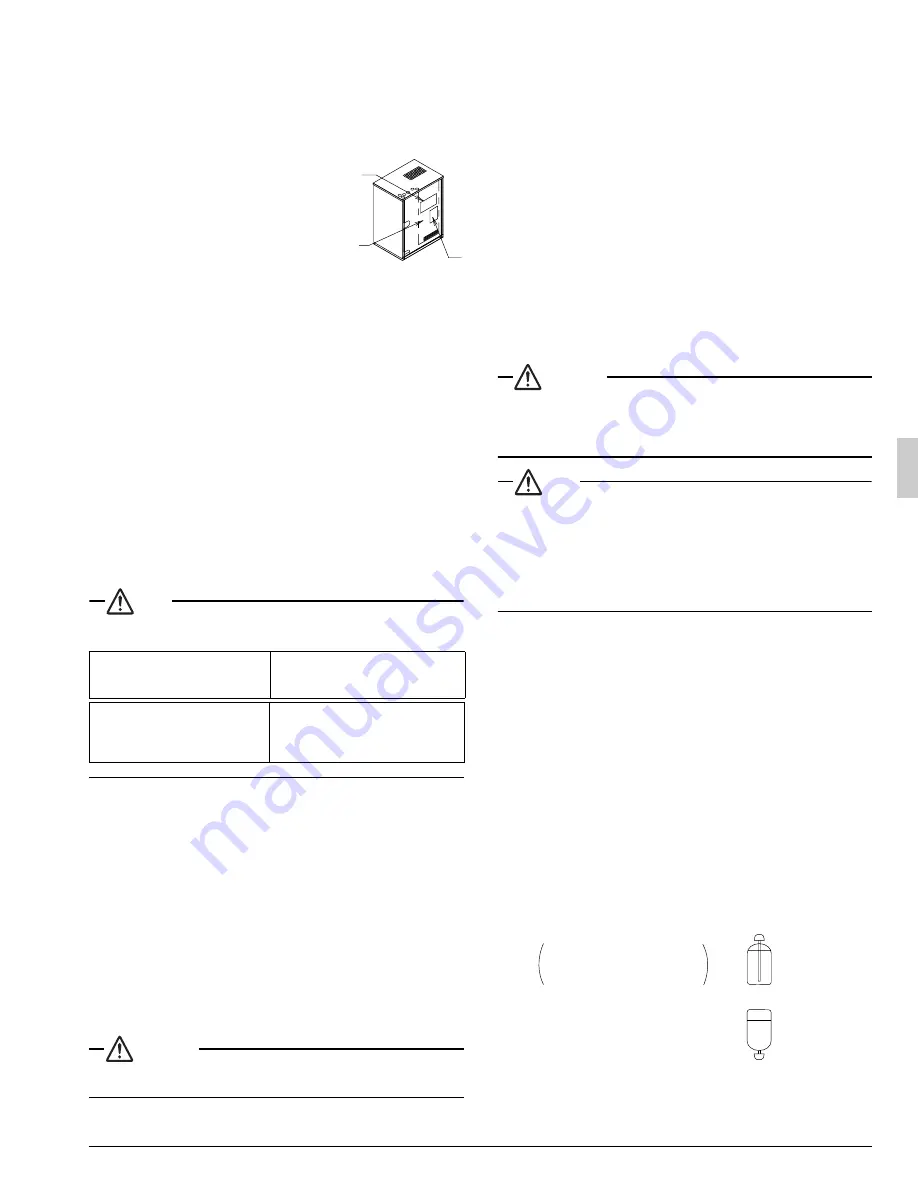
English
14
9-6 Air tight test and vacuum drying
The units were checked for leaks by the manufacturer.
Confirm that the valves are firmly closed before Air tight test or vacuum
drying.
To prevent entry of any impurities and ensure sufficient pressure resis-
tance, always use the special tools dedicated for R410A.
•
Air tight test:
Make sure to use nitrogen gas.
(For the service port location, refer to the
“Caution” label attached on the front panel
[right] of the outside unit.)
(Refer to figure)
1.
[Service precautions] Label
2.
Electrical components box lid
3.
[Caution] Label
Pressurize the liquid and gas pipes to 450 psi
(do not pressurize more than 450 psi). If the
pressure does not drop within 24 hours, the
system passes the test. If the pressure drops, check where the nitro-
gen leaks from.
•
Vacuum drying:
Use a vacuum pump which can evacuate to
–14.6 psi.
1.
Evacuate the system from the liquid and gas pipes by using a
vacuum pump for more than 2 hours and bring the system to
–14.6 psi or less. After keeping the system under that condition
for more than 1 hour, check if the vacuum gauge rises or not. If it
rises, the system may either contain moisture inside or have
leaks.
2.
Following should be executed if there is a possibility of moisture
remaining inside the pipe (if piping work is carried out during the
raining season or over a long period of time rainwater may enter
the pipe during work).
After evacuating the system for 2 hours, pressurize the system to
7.25 psi (vacuum break) with nitrogen gas and evacuate the sys-
tem again using the vacuum pump for 1 hour to –14.6 psi or less
(vacuum drying). If the system cannot be evacuated to –14.6 psi
within 2 hours, repeat the operation of vacuum break and vacuum
drying.
Then, after leaving the system in vacuum for 1 hour, confirm that
the vacuum gauge does not rise.
NOTE
Make sure to perform air tight test and vacuum drying using the service
ports of the stop valve shown in the table below.
9-7 Pipe insulation
After finishing the leak test and vacuum drying, the piping must be insu-
lated. Take into account the following points:
• Make sure to insulate the connection piping and refrigerant branch
kits entirely.
• Be sure to insulate the liquid-side, suction gas-side and discharge
gas-side piping for the inter-unit piping and the refrigerant branch kits.
Not insulating them may cause leaking. (The gas piping can reach
temperatures of 250 °F. Be sure the insulation used can withstand
such temperatures.)
• If you think the humidity around the cooling piping might exceed
86 °F and RH80%, reinforce the insulation on the cooling piping (at
least 13/16” thick). Condensation might form on the surface of the
insulation.
• If there is a possibility that condensation on the stop valve might drip
down into the indoor unit through gaps in the insulation and piping
because the outside unit is located higher than the indoor unit, etc.,
this must be prevented by caulking the connections, etc.
WARNING
• Be sure to insulate connection piping, as touching them can cause
burns.
9-8 Checking of device and installation conditions
Be sure to check the followings.
1.
Make sure there is no faulty power wiring or loosing of a nut.
See “
”.
2.
Make sure there is no faulty transmission wiring or loosing of a nut.
See “
”.
3.
Make sure there is no faulty refrigerant piping.
See “
”.
4.
Make sure piping size is correct.
See “
9-1 Selection of piping material
”.
5.
Make sure insulation work is done.
See “
6.
Make sure insulation resistance of main power circuit is not deterio-
rated.
Using a megatester for 500V, check that the insulation resistance of
2M
Ω
or more is attained by applying a voltage of 500V DC between
power terminals and earth. Never use the megatester for the trans-
mission wiring (between outside and indoor unit, outside and COOL/
HEAT selector and etc.).
9-9 Additional refrigerant charge
WARNING
• To avoid injury always use protective gloves and eye protection
when charging refrigerant.
•
To avoid injury do not charge with unsuitable substances. Use only
the appropriate refrigerant.
NOTE
•
Refrigerant cannot be charged until field wiring has been com-
pleted.
Refrigerant may only be charged after performing the leak test and
the vacuum drying (see above).
When charging a system, care shall be taken that its maximum per-
missible charge is never exceeded, in view of the danger of liquid
hammer.
Refrigerant containers shall be opened slowly.
TO AVOID COMPRESSOR BREAKDOWN. DO NOT CHARGE THE
REFRIGERANT MORE THAN THE SPECIFED AMOUNT TO RAISE
THE CONDENSING PRESSURE.
• This outside unit is factory charged with refrigerant and depending
on pipe sizes and pipe lengths some systems require additional
charging of refrigerant.
• Determine the amount of refrigerant to be added by referring to the
table, write it down on the included “Added Refrigerant” plate and
attach it to the rear side of the front cover.
Note: refer to the example of connection for the amount to be added.
Additional refrigerant charge procedure (1)-normally
• Charge the refrigerant to the liquid pipe in its liquid state. Since
R410A is a mixed refrigerant, its composition changes if charged in
a state of gas and normal system operation would no longer be
assured.
• Make sure to use installation tools you exclusively use on R410A
installations to withstand the pressure and to prevent foreign materi-
als from mixing into the system.
1.
Before charging, check whether the tank has a siphon attached or not.
How to charge with the siphon tank.
Other ways of charging with the tank.
One outside unit installed
Liquid line stop valve
Discharge gas line stop valve
Suction gas line stop valve
Multiple outside units installed
Liquid line stop valve
Discharge gas line stop valve
Suction gas line stop valve
Oil-equalizing line stop valve
1
3
2
There is a siphon tube
inside, so there is no need
to turn the tank upside-down.
Charge with the tank upright.
Charge with the tank upside-down.