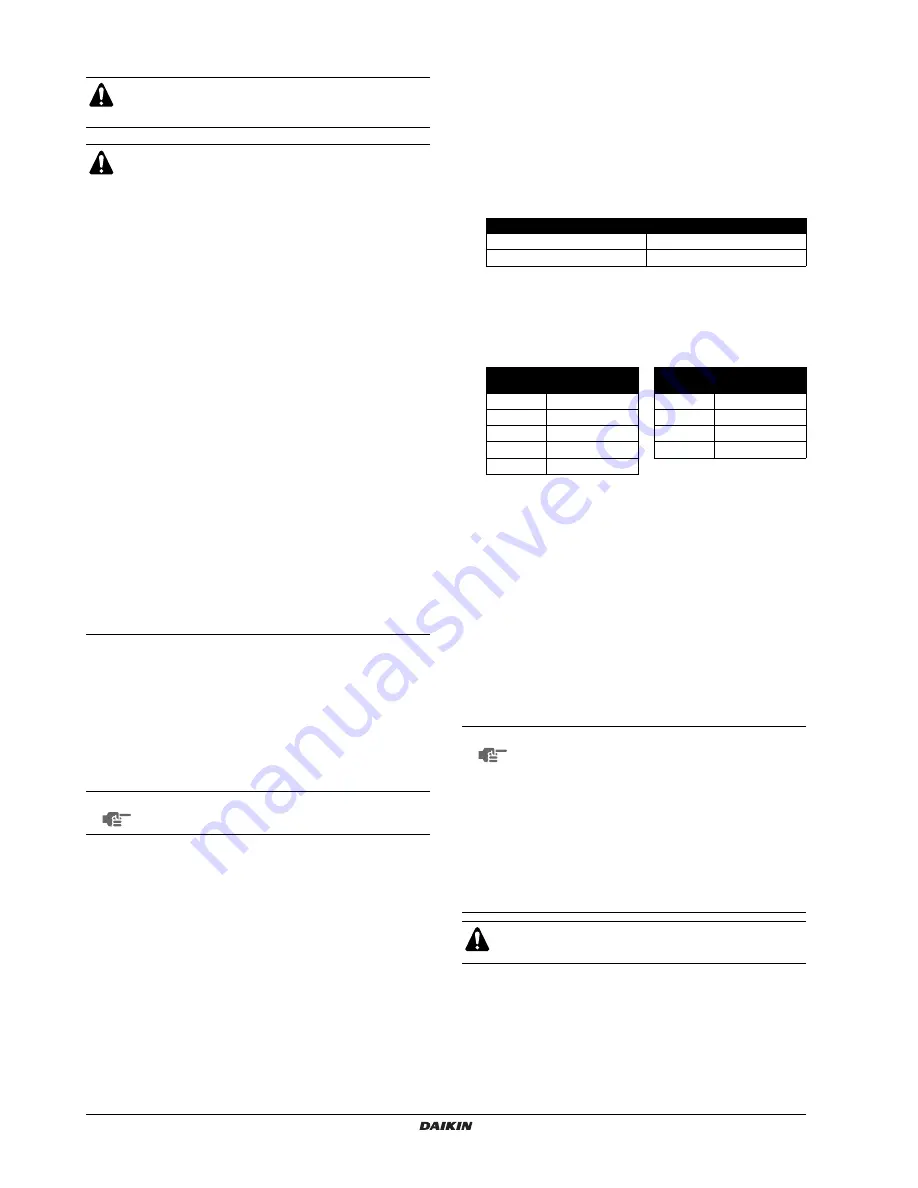
Installation manual
5
R REMQ10~16P8 + REMHQ12P8Y1B
VRVIII System air conditioner
4PW48463-1A
6.
R
EFRIGERANT
PIPING
6.1.
Installation tools
Make sure to use installation tools (gauge manifold charge hose,
etc.) that are exclusively used for R410A installations to withstand the
pressure and to prevent foreign materials (e.g. mineral oils such as
SUNISO and moisture) from mixing into the system.
(The screw specifications differ for R410A and R407C.)
Use a 2-stage vacuum pump with a non-return valve which can
evacuate to –100.7 kPa (5 Torr, –755 mm Hg).
6.2.
Selection of piping material
1.
Foreign materials inside pipes (including oils for fabrication)
must be 30 mg/10 m or less.
2.
Use the following material specification for refrigerant piping:
■
Size: determine the proper size referring to chapter
"6.6. Example of connection" on page 9
.
■
Construction material: phosphoric acid deoxidized seamless
copper for refrigerant.
■
Temper grade: use piping with temper grade in function of the
pipe diameter as listed in the table below.
■
The pipe thickness of the refrigerant piping should comply
with relevant local and national regulations. The minimal pipe
thickness for R410A piping must be in accordance with the
table below.
3.
Make sure to use the particular branches of piping that have
been selected referring to chapter
"6.6. Example of connection"
on page 9
.
4.
In case the required pipe sizes (inch sizes) are not available, it is
also allowed to use other diameters (mm sizes), taken the
following into account:
■
select the pipe size nearest to the required size.
■
use the suitable adapters for the change-over from inch to
mm pipes (field supply).
6.3.
Pipe connection
Be sure to perform a nitrogen blow when brazing and to read the
paragraph
"Caution to be taken when brazing refrigerant piping" on
page 5
first.
Do not insert fingers, rods or other objects into the air
inlet or outlet. When the fan is rotating at high speed, it
will cause injury.
Use R410A to add refrigerant.
All field piping must be installed by a licensed refrigeration
technician and must comply with relevant local and
national regulations.
Caution to be taken when brazing refrigerant piping
Do not use flux when brazing copper-to-copper refrigerant
piping. (Particularly for the HFC refrigerant piping)
Therefore, use the phosphor copper brazing filler metal
(BCuP) which does not require flux.
Flux has extremely harmful influence on refrigerant piping
systems. For instance, if the chlorine based flux is used, it
will cause pipe corrosion or, in particular, if the flux
contains fluorine, it will damage the refrigerant oil.
Be sure to perform a nitrogen blow when brazing. Brazing
without releasing nitrogen into the piping will create large
quantities of oxidized film on the inside of the pipes,
adversely affecting valves and compressors in the
refrigerating system and preventing normal operation.
After completing the installation work, check that the
refrigerant gas does not leak.
Do not open stop valves until all field wiring is according to
the specifications (refer to
"8. Field wiring" on page 12
),
the checking of the unit has been completed and all
installation conditions are fulfilled (refer to
"10. Checking of
unit and installation conditions" on page 17
).
Toxic gas may be produced if the refrigerant gas leaks into
the room and comes in contact with a source of fire.
Ventilate the area immediately in the event of a leak.
In the event of a leak, do not touch the leaked refrigerant
directly. Frostbite may be caused.
NOTE
Make sure the pump oil does not flow oppositely into
the system while the pump is not working.
Pipe Ø
Temper grade of piping material
≤
15.9
O
≥
19.1
1/2H
O = Annealed
1/2H = Half hard
Pipe Ø
Minimal thickness
t (mm)
Pipe Ø
Minimal thickness
t (mm)
6.4
0.80
22.2
0.80
9.5
0.80
28.6
0.99
12.7
0.80
34.9
1.21
15.9
0.99
41.3
1.43
19.1
0.80
NOTE
The pressure regulator for the nitrogen released when
doing the brazing should be set to 0.02 MPa or less.
(See figure 10)
Do not use anti-oxidants when brazing the pipe joints.
Residue can clog pipes and break equipment.
1
Refrigerant piping
2
Location to be brazed
3
Nitrogen
4
Taping
5
Manual valve
6
Regulator
7
Nitrogen
Содержание REMQ8P9Y1B
Страница 36: ...4PW48463 1A Copyright Daikin...