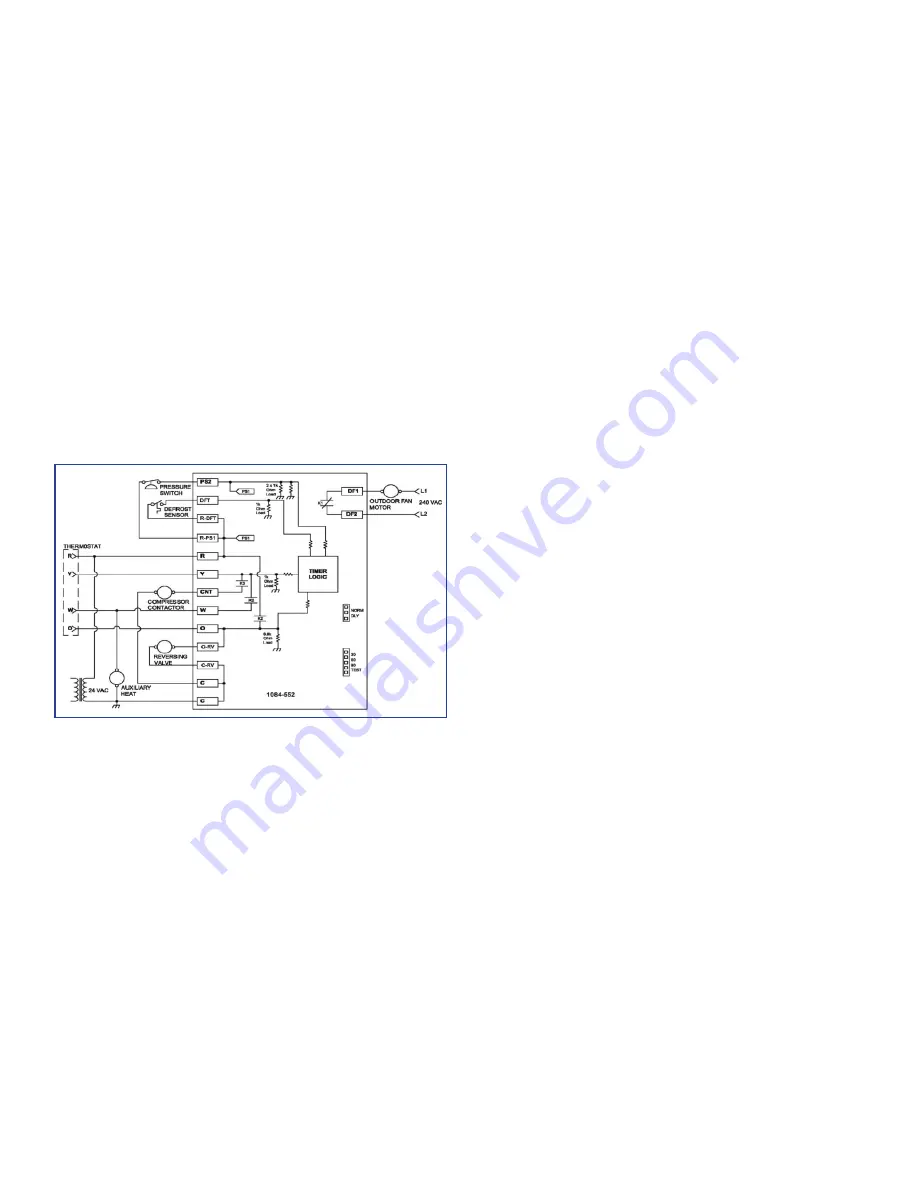
16
defrost control board.
2.
Remove jumper from timer pins and jump across test
pins on defrost control board.
NOTE:
Do not use screwdriver or field
supplied jumper to test the control.
3. Set thermostat to call for heating. System should go
into defrost within 21 seconds.
4. Immediately remove jumper from test pins.
5. Using VOM check for voltage across terminals “C &
O”. Meter should read 24 volts.
6. Using VOM check for voltage across fan terminals
DF1 and DF2 on the board. Should read line voltage
(208-230 VAC) indicating the relay is open in the
defrost mode.
7. Using VOM check for voltage across “W”/”W2” & “C”
terminals on the board. Should read 24 volts.
8. If not as above, replace control board.
9. Set thermostat to off position and disconnect power.
Remove jumper from defrost thermostat and replace
timer jumper to the desired defrost time.
NOTE: Remove jumper across defrost thermostat
before returning system to service.
Defrost Control Wiring Schematic
Testing Defrost Thermostat
1.
Install a thermocouple type temperature test lead on
the tube adjacent to the defrost control. Insulate the
lead point of contact.
2. Check the temperature at which the control closes its
contacts by lowering the temperature of the control.
It should close at approximately 30°F.
3. Check the temperature at which the control opens its
contacts by raising the temperature of the control. It
should open at approximately 60°F.
4. If not as above, replace control.
REVERSING VALVE TROUBLESHOOTING
Checking Reversing Valve and Solenoid
Reversing valve used in heat pumps could potentially leak
internally. Discharge gases can leak into the suction inside
the valve. Compound gages will give the same symptoms
as bad compressor valves or broken scroll flanks. The
temperature between true suction and the suction line after
the valve should not be greater than 4 degrees. Note: The
center tube is always the suction line and should be cold.
Troubleshooting the Reversing Valve for
Electrical Failure
1. Place unit into the cooling mode. Test for 24 volts at
the solenoid. If there is no voltage present at coil,
check the control voltage.
2.
If voltage is present, loosen the nut on the top of
the coil. Remove the coil, there should be slight
resistance.
3. If the slight resistance is felt, remove the coil. As
you remove the coil listen carefully, an audible
click should be detected. The clicking is due to the
movement of the pilot valve plunger. The absence of
a clicking sound indicates the plunger is stuck.
Troubleshooting Mechanical Failures on a
Reversing Valve by Pressure
1.
Troubleshooting the reversing valve can be done by
pressure and touch.
2. Raise the head pressure. In the cooling mode block
the fan exhaust. Once head pressure has been
raised, cycle between cooling and heating and see if
the piston can be freed.
Troubleshooting Mechanical Failures on a
Reversing Valve byTemperature
1. When operating properly the valve contains
refrigerant gases at certain temperatures.
2.
The discharge line should be the same temperature
after the valves discharge line.
3.
The true suction should be the same as the suction
line after the valve. If there is a 4-degree difference,
valve is leaking
When stuck in the mid-position, part of the discharge gas
from the compressor is directed back to the suction side,
resulting in excessively high suction pressure. An increase
in the suction line temperature through the reversing
valve can also be measured. Check operation of the valve
by starting the system and switching the operation from
COOLING to HEATING cycle.
If the valve fails to change its position, test the voltage
(24V) at the valve coil terminals, while the system is on the
COOLING cycle.
If voltage is registered at the coil, tap the valve body lightly
while switching the system from HEATING to COOLING,
etc. If this fails to cause the valve to switch positions,
remove the coil connector cap and test the continuity of
the reversing valve solenoid coil. If the coil does not test
continuous - replace it. If the coil test continuous and 24
volts is present at the coil terminals, the valve is inoperative
- replace it.
Содержание M Series
Страница 18: ...18 Wiring Example Electric Heat Wiring Example...
Страница 25: ...25 THIS PAGE INTENTIONALLY LEFT BLANK...
Страница 26: ...26 THIS PAGE INTENTIONALLY LEFT BLANK...
Страница 27: ...27 THIS PAGE INTENTIONALLY LEFT BLANK...