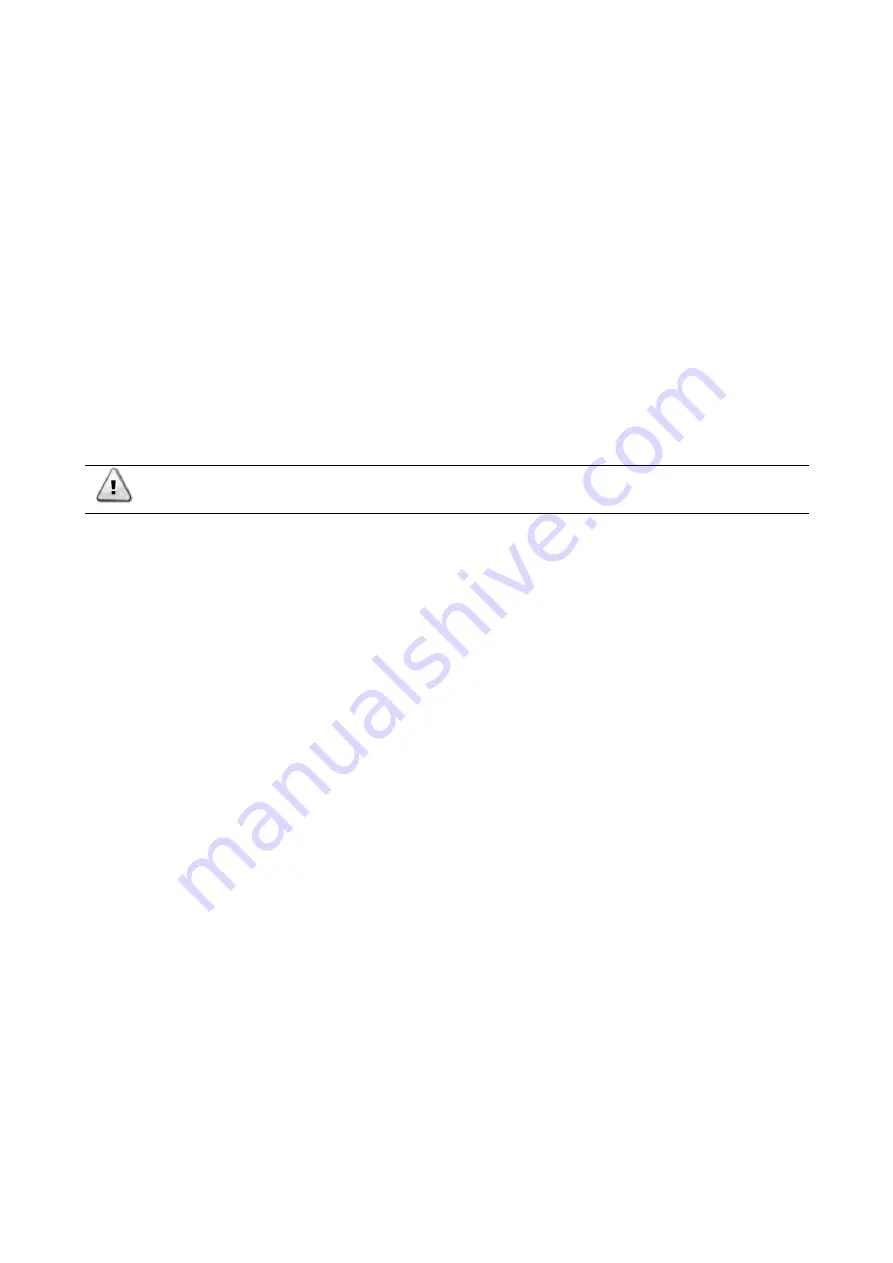
D
–EIMWC00803-21_01EN - 37/57
pump the system down, close all liquid line valves. With all liquid line valves closed and water flowing, start the compressor.
Set the MicroTech control to the manual load. The vanes must be open while pumping down to avoid a surge or other
damaging condition. Pump the unit down until the MicroTech controller cuts out at approximately 20 psig. It is possible that
the unit might experience a mild surge condition prior to cutout. If this should occur, immediately shut off the compressor.
Use a portable condensing unit to complete the pump down, condense the refrigerant, and pump it into the condenser or
pumpout vessel using approved procedures.
A pressure regulating valve must always be used on the drum being used to build the system pressure. Also, do not exceed
the test pressure given above. When the test pressure is reached disconnect the gas cylinder.
8.5.3
Pressure Testing
No pressure testing is necessary unless some damage was incurred during shipment. Damage can be determined upon
a visual inspection of the exterior piping, checking that no breakage occurred or fittings loosened. Service gauges should
show a positive pressure. If no pressure is evident on the gauges, a leak may have occurred, discharging the entire
refrigerant charge. In this case, the unit must be leak tested to determine the location of the leak.
8.5.4
Leak Testing
In the case of loss of the entire refrigerant charge, the unit must be checked for leaks prior to charging the complete system.
This can be done by charging enough refrigerant into the system to build the pressure up to approximately 10 psig (69 kPa)
and adding sufficient dry nitrogen to bring the pressure up to a maximum of 125 psig (860 kPa). Leak test with an electronic
leak detector. Halide leak detectors do not function with R-134a, R-513A and R-1234ze. Water flow through the vessels
must be maintained anytime refrigerant is added or removed from the system.
WARNING
Do not use oxygen or a mixture of refrigerant and air to build up pressure as an explosion can
occur causing serious personal injury.
If any leaks are found in welded or brazed joints, or it is necessary to replace a gasket, relieve the test pressure in the
system before proceeding. Brazing is required for copper joints.
After making any necessary repair, the system must be evacuated as described in the following section.
8.5.5
Evacuation
After it has been determined that there are no refrigerant leaks, the system must be evacuated using a vacuum pump with
a capacity that will reduce the vacuum to
at least 1000 microns of mercury
.
A mercury manometer, or an electronic or other type of micron gauge, must be connected at the farthest point from th e
vacuum pump. For readings below 1000 microns, an electronic or other micron gauge must be used.
The triple evacuation method is recommended and is particularly helpful if the vacuum pump is unable to obtain the desired
1 millimeter of vacuum. The system is first evacuated to approximately 29 inches of mercury. Dry nitrogen is then added
to the system to bring the pressure up to zero pounds.
Then the system is once again evacuated to approximately 29 inches of mercury. This is repeated three times. The first
pulldown will remove about 90% of the noncondensables, the second about 90% of that remaining from the first pulldown
and, after the third, only 1/10-1% noncondensables will remain.
8.5.6
Charging the System
DWSC water chillers are leak tested at the factory and shipped with the correct charge of refrigerant as indicated on the
unit nameplate. In the event the refrigerant charge was lost due to shipping damage, the system should be charged as
follows after first repairing the leaks and evacuating the system.
1. Connect the refrigerant drum to the gauge port on the evaporator shutoff valve and purge the charging line between
the refrigerant cylinder and the valve. Then open the valve to the mid -position.
2. Turn on both the cooling tower water pump and chilled water pump and allow water to circulate through the condenser
and the chiller. (It will be necessary to manually close the condenser pump starter.)
3. If the system is under a vacuum, stand the refrigerant drum with the connection up, and open the drum and break the
vacuum with refrigerant gas to a saturated pressure above freezing.
4. With a system gas pressure higher than the equivalent of a freezing temperature, invert the charging cylinder and
elevate the drum above the evaporator. With the drum in this position, valves open, water pumps operating, liquid
refrigerant will flow into the evaporator. Approximately 75% of the total requirement estimated for the unit can be
charged in this manner.
5. After 75% of the required charge has entered the evaporator, reconnect the refrigerant drum and charging line to the
service valve on the bottom of the condenser. Again purge the connecting line, stand the drum with the connection
up, and place the service valve in the open position.
IMPORTANT
: At this point, the charging procedure should be interrupted and prestart checks made before attempting to
complete refrigerant charge. The compressor must not be started at this time. (Preliminary check must first be completed.)
NOTE
: It is of utmost importance that all local, national, and international regulations concerning the handling and emission
of refrigerants are observed.