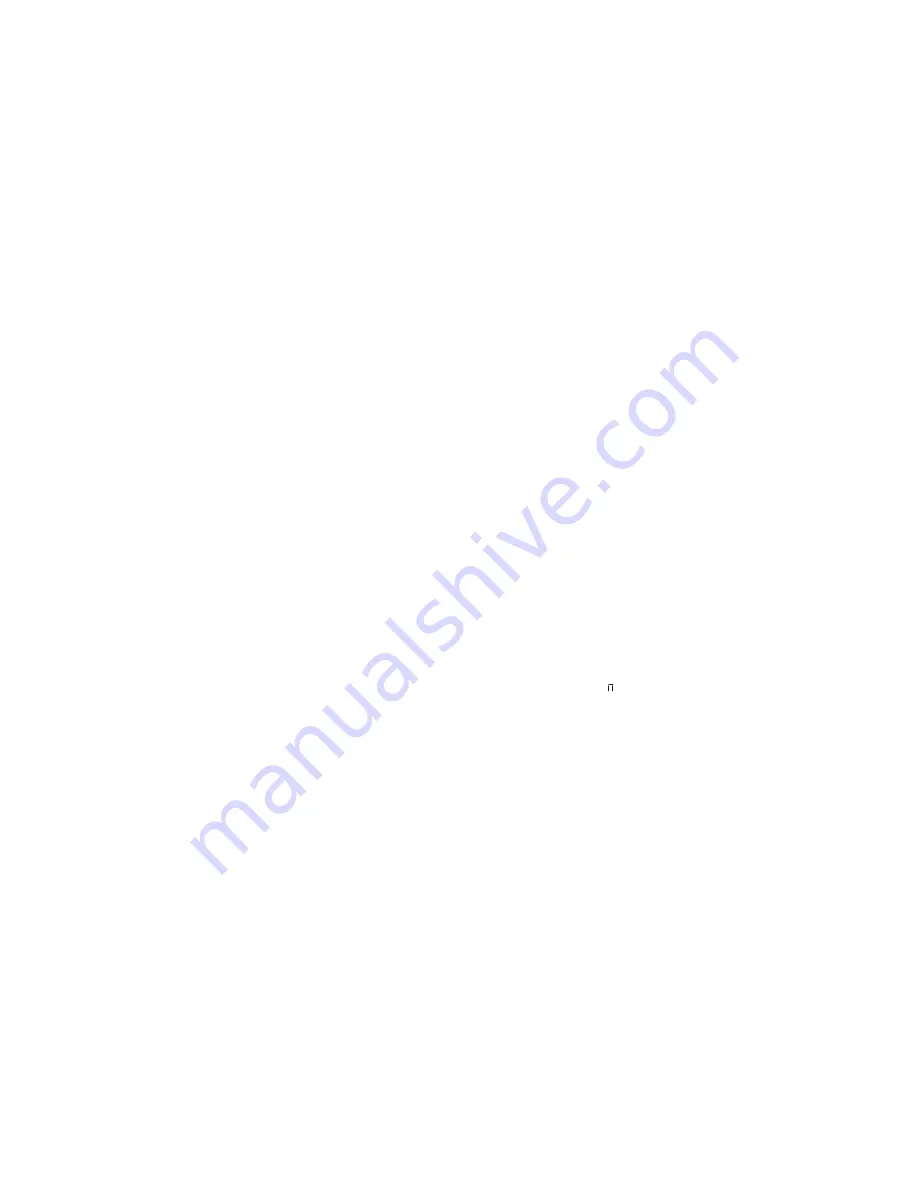
43
T
HERMOSTAT
M
ENU
If this furnace is installed with a communicating compatible
heat pump, the system is recognized as a dual fuel system.
The balance point temperature should be set via the
thermostat.
D
IAGNOSTICS
Accessing the furnace’s diagnostics menu provides ready
access to the last six faults detected by the furnace. Faults
are stored most recent to least recent. Any consecutively
repeated fault is stored a maximum of three times.
Example: A clogged return air filter causes the furnace limit
to trip repeatedly. The control will only store this fault the
first three
consecutive
times the fault occurs. Navigate to
the diagnostics menu as described above in the thermostat
installation manual.
NOTE:
It is highly recommended that the fault history be
cleared when performing maintenance or servicing the
furnace.
N
ETWORK
TROUBLESHOOTING
Communications is achieved by taking the difference
between two dc signals. The signals and transmission lines
are referred to as “data 1” and “data 2”. The voltage
difference between data 1 and data 2 is typically 0.6 Vdc.
The ComfortNet™ system is a fully communicating system,
and thus, constitutes a network. Occasionally the need to
troubleshoot the network may arise. The integrated furnace
control has some on-board tools that may be used to
troubleshoot the network. These tools are: red
communications LED, green receive (Rx) LED, and learn
button.
•
Red communications LED – Indicates the status of the
network. The table below indicates the LED status
and the corresponding potential problem.
•
Green receive LED – Indicates network traffic. The
table below indicates the LED status and the
corresponding potential problem.
•
Learn button – Used to reset the network. Depress
the button for approximately 2 seconds to reset the
network.
S
YSTEM
T
ROUBLESHOOTING
NOTE:
Refer to the instructions accompanying the
ComfortNet compatible outdoor AC/HP unit for
troubleshooting information.
Refer to the Troubleshooting Chart in the back of this manual
for a listing of possible furnace error codes, possible causes
and corrective actions.
F
AULT
R
ECALL
S
EQUENCE
•
Only allowed in standby mode while display is
showing ON.
•
Hold fault recall push-button for 2-5 seconds (until
display is blank) and then release.
•
Display will then be blank for 2 seconds before
displaying faults stored in history.
•
All faults are displayed one time, from most recent
to least recent.
•
A maximum of 3 consecutive faults of the same type
will be logged.
•
Each error is displayed for 2-seconds, with a blank
screen for 1 second in between.
•
When all errors have been displayed, the display
returns to ON.
F
AULT
C
LEAR
S
EQUENCE
•
Only allowed in standby mode while display is showing
ON.
•
Hold fault recall push-button for 5-10 seconds (until
display starts flashing “_”) and then release.
•
All faults in the history will have been cleared, and
display returns to ON.
•
If the button is held for longer than 10 seconds, the
display will return to ON and the faults will not be
cleared.
N
ORMAL
S
EQUENCE
OF
O
PERATION
P
OWER
U
P
The normal power up sequence is as follows:
•
115 VAC power applied to furnace.
•
Integrated control module performs internal checks.
•
Integrated control module displays
8 8
on dual 7-
segment display LED’s.
•
Integrated control module monitors safety circuits
continuously.
•
Furnace awaits call from thermostat. Dual 7-segment
LED’s display
O
while awaiting call from thermostat.
H
EATING
M
ODE
The normal operational sequence in heating mode is as
follows:
•
R and W1 (or R and W1/W2) thermostat contacts
close, initiating a call for heat.
•
Integrated control module performs safety circuit
checks.
•
Induced draft blower is energized on high speed for
a 15-second prepurge. Humidifier terminal is
energized with induced draft blower.
•
Induced draft blower steps to low speed following
prepurge. Low stage pressure switch contacts are
closed.
•
Igniter warm up begins upon step to low speed and
presence of closed low stage pressure switch
contacts.
•
Gas valve opens at end of igniter warm up period,
delivering gas to burners and establishing flame.
•
Integrated control module monitors flame presence.
Gas valve will remain open only if flame is detected.
•
If the thermostat call is for low heat, gas valve and
induced draft blower will continue on low stage. If