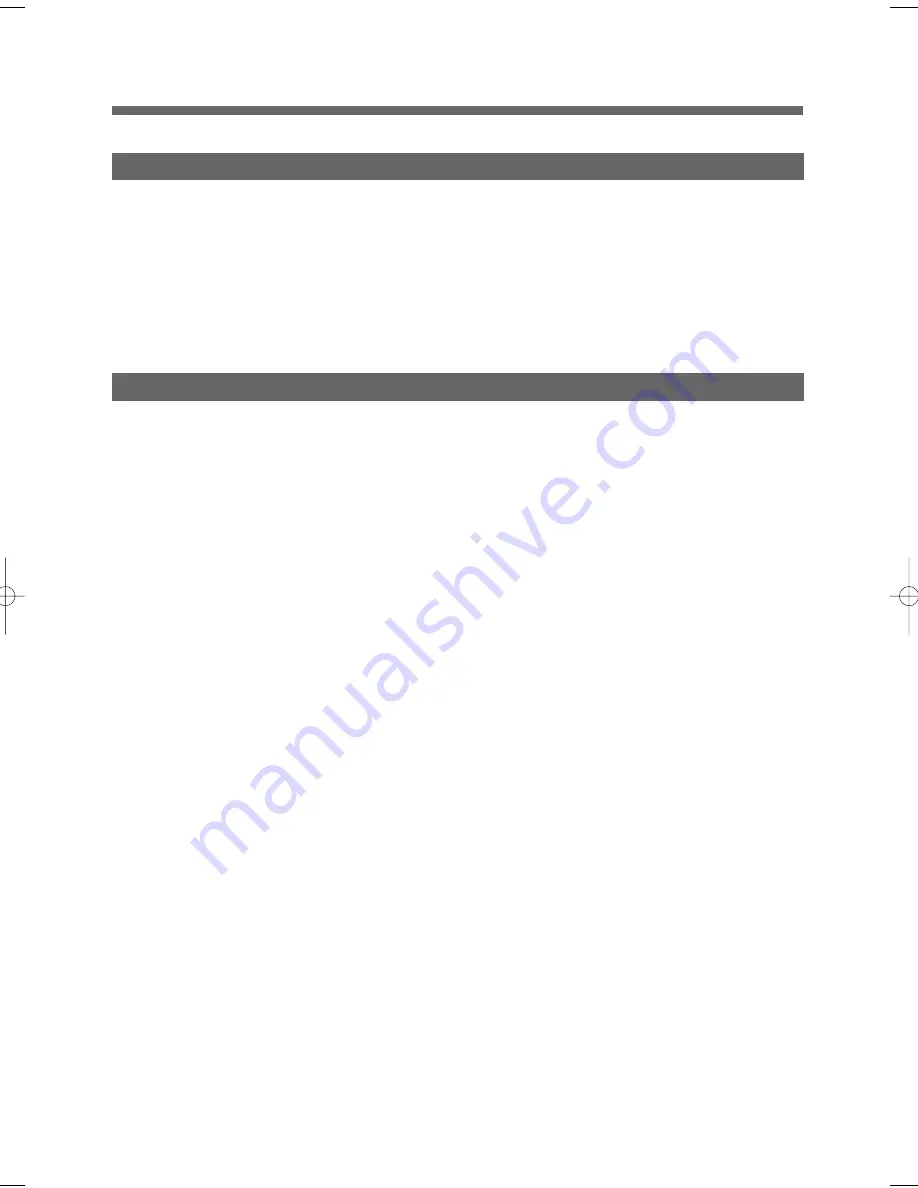
2
Water consumption is reduced by using the power of the laundry falling (free-fall) created when rotating
the drum resembling a sieve net. With temperature control system, this drum washing machine saves
energy and improves washing performance at the same time.
"
What is Drum Washing Machine?
1. Drum Washing Machine
"
Note that some features are options.
#
Simultaneous supply of cold
$
hot water
As cold and hot water is supplied at the same time, heating time and energy is saved.
#
Top-quality popup dial
The top-quality popup dial is used only during washing process.
#
Dust filter
Filter to remove foreign substances, such as naps generated during washing, etc., is installed inside the
drum.
#
DD inverter motor
The direct-drive type, of which motor is directly connected to drum without an interim clutch,
significantly reduces noise and vibration.
#
Heating device is installed to enable boiling of the laundry.
#
Large door creates grand appearance and makes it easy to put in and out the laundry.
#
For pump drainage, the powerful pump speeds up drainage process.
2. Features of Drum Washing Machine
Содержание DWD-WD135 SERIES
Страница 48: ...47 PCB PIN ARRANGEMENT ...
Страница 60: ...59 BLDC Motor Power Transmission System of BLDC Motor ...
Страница 65: ...64 Wiring Diagram ...
Страница 71: ...70 PLATE TOP ASS Y 1 Remove 3 screws 2 Remove 4 screws ...
Страница 73: ...72 VALVE 3WAY 1 Remove 4 screws 2 Separate 3 connectors 3 Separate 3 hose clamps ...
Страница 74: ...73 MAIN PCB ASS Y 1 Separate harness and separate PCB cover 2 Separate connector 3 Remove 1 screw ...