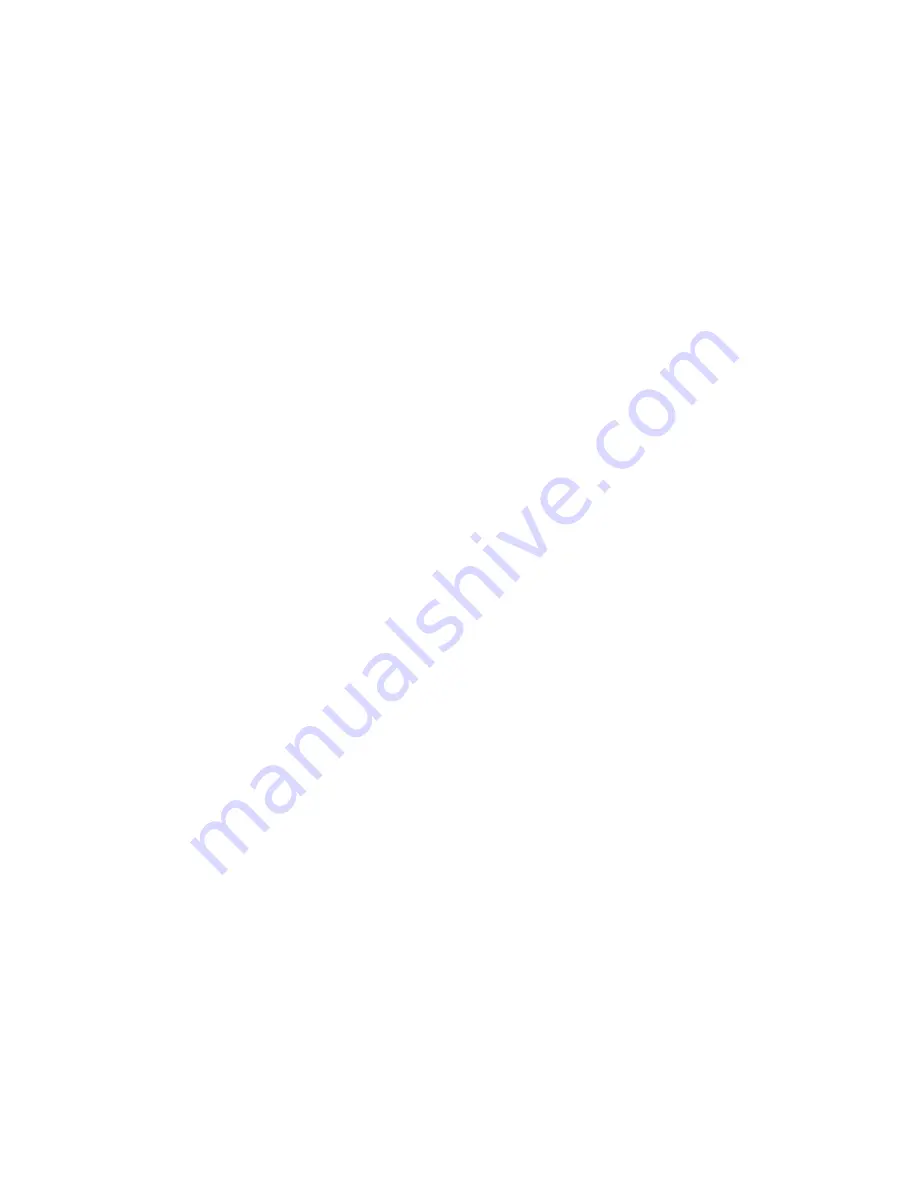
24
I.B. 8926-1A
locking bar recessed in the handle may be extended
and padlocked with from one to three padlocks. See
Figure 34.
With the door open and the disconnect device OFF,
the operating handle is mechanically interlocked to
prevent inadvertently being pushed ON. To defeat
this interlock, the bar on the top of the mechanism
should be pushed in slightly, allowing the handle to
move upward to the ON position.
WARNING: IF
FULLY INSERTED, THE POWER AND CONTROL
CITCUITS WILL BE ENERGIZED.
Padlocking to
prevent this handle movement may be accomplished
by the same method as described above.
Separate control sources of power must also be
disconnected. If control power is used during
maintenance, take steps to prevent feedback of a
hazardous voltage through a control
transformer. Be alert to power factor correction
capacitors that may be charged. Discharge them
before working on any part of the associated
power circuit.
Cleaning.
Soot, smoke, or stained areas (other than
inside arc chutes), or other unusual deposits, should
be investigated and the source determined before
cleaning is undertaken. Vacuum or wipe clean all
exposed surfaces of the control component and the
inside of its enclosure. Equipment may be blown
clean with compressed air that is dry and free from
oil. (Be alert to built-in oilers in factory compressed
air lines!) If air blowing techniques are used, remove
arc covers from contactors and seal openings to
control circuit contacts that are present. It is
essential that the foreign debris be removed from
the control center, not merely rearranged. Control
equipment should be clean and dry. Remove dust
and dirt inside and outside the cabinet without using
liquid cleaner. Remove foreign material from the
outside top and inside bottom of the enclosure,
including hardware and debris, so that future
examination will reveal any parts that have fallen off
or dropped onto the equipment. If there are liquids
spread inside, determine the source and correct by
sealing conduit, adding space heaters, or other
action as applicable.
Mechanical checks.
Tighten all electrical
connections. Look for signs of overheated joints,
charred insulation, discolored terminals, etc.
Mechanically clean to a bright finish (don’t use
emery paper) or replace those terminations that
have become discolored. Determine the cause of
the loose joint and correct. Be particularly careful
with aluminum wire connections. Aluminum wire is
best terminated with a crimp type lug that is attached
to the control component. When screw type lugs
(marked CU/AL) are used with aluminum wire, joint
should be checked for tightness every 200
operations of the device.
Wires and cables should be examined to eliminate
any chafing against metal edges caused by
vibration, that could progress to an insulation failure.
Any temporary wiring should be removed, or
permanently secured and diagrams marked
accordingly.
The intended movement of mechanical parts, such
as the armature and contacts of electromechanical
contactors, and mechanical interlocks should be
checked for freedom of motion and functional
operation.
Wrap-up.
Check all indicating lamps, mechanical
flags, doors, latches, and similar auxiliaries and
repair, if required.
Log changes and observations into record book
before returning equipment into service. Do not
remove any labels or nameplates. Restore any that
are damaged.
SLIDER OPERATOR MECHANISM –
(6 Inch Units) (See Figure 35)
The following features are found on 6-inch units with
circuit breaker operators.
A.
Door Interlock
The operator mechanism is factory adjusted and
normally does not need field adjustment. The
door interlock mechanism engages a hook that
is mounted to the welded bracket. This allows
the unit door to open when the operator handle
is in the “off” (right) position. With the handle in
the “on” (left) position, the door is interlocked
and should not open. If the door hook and the
mechanism do not engage properly, the
positioning of the door hook on the bracket may
need adjustment. The door hook can be
adjusted left or right by loosening the screw (see
photograph). After adjustment, tighten screw to
20 lb.-in. [2.2 N
•
m]. See Figure 38 insert.
B.
Defeater Screw
Turning the defeater screw clockwise allows you
to open the unit door (access to the panel
mounted components) with the operator handle
(padlocked or not) in the “on” (left) position.
C.
Padlocking (See Figures 36, & 37)
The operator handle can be padlocked in the
“off” position with up to three 3/8” [19.5 mm]
(Max.) shank padlocks.
Содержание Freedom 2100 Series
Страница 31: ...31 I B 8926 1A Part 11 PLAN VIEWS...